HDPE pipe extrusion is a distinct and advanced operation critical in producing various pipes used in multiple fields. Whether water supply networks or gas pipelines, HDPE pipes comprise all the necessary properties, including strength, bending, and deformation without failure, even in extreme conditions. This article will focus on the details above, such as an extrusion line for manufacturing pipes, how the process takes place, and the major reasons why HDPE pipes remain the best choice for most structural works today. Suppose you are one of the practitioners in this field or are just interested in it. In that case, this blog will provide you with essential information and understanding about the technology and innovations of HDPE pipe manufacturing.
What is an HDPE Pipe Extrusion Line?
hdpe pipe extrusion line
HDPE pipe extrusion line is a state-of-the-art manufacturing arrangement for producing high-density polyethylene pipes which is critical owing to many infrastructure applications. The line commences with a feed of HDPE resin, which goes into the extruder to be melted and mixed. The mass is formed into a pipe shape by forcing it through a die, after which the pipe is cooled and accurately sized through a calibration procedure. A typical extrusion line has several components, which include a vacuum calibration tank, cooling tanks, a haul-off machine, a cutter, and others that are efficiently integrated to produce quality pipes. These lines are also efficient since they bring forth the desired qualities of flexibility, strength, corrosion resistance, and chemical resistance of the pipes fabricated with great ease for applications ranging from potable water supply to natural gas transmission.
Understanding the HDPE Pipe Extrusion Process
To appreciate the intricacies of HDPE pipe extrusion, it is helpful to delve into the processes involved, as noted by various leading online sources. The procedure typically seizes several significant phases, and these include:
- Material Feeding: The commencement of the process is marked by the loading of high-density polyethylene granules into an extruder hopper. These granules will then be mechanically softened sequentially as they traverse the barrel of the extruder.
- Extrusion and Die Process: The extruder has a screw where the HDPE material is subjected to sufficient imagination to melt it down and apply a metered pressure to the screw content to make sure the liquid polymer blend is result oriented in every aspect. It further goes through a die, which shapes it into a pipe.
- Calibration and Cooling: Newly formed products from the die, such as pipes, are cooled in a vacuum calibration tank, which is subsequently followed by cooling tanks. This stage is very important in preserving the geometry and strength of the pipe.
- Haul-off and Cutting: The pipe is then controlled by a haul-off machine and moved in the direction of the extrusion line until the entire length is formed. After that, a tapering device cuts the finished pipe into lengths as specified.
Technical Parameters
- Melt Temperature: In most circumstances, 180 degrees centigrade and 240 degrees centigrade are the temperatures maintained to facilitate the melting of substances into the polymer without damaging the polymer.
- Screw Speed: Depends on the diameter of the pipe made, which often ranges between 20 to 120 RPM for most variables.
- Vacuum Calibration Pressure: Around 0.3 MPa to ensure an accurate size.
- Cooling Water Temperature: This should preferably be 10-30oC to facilitate quick and even cooling.
These parameters are critical in producing high-quality HDPE pipes that align with industrial strength and shock resistance requirements. The extrusion technology and parameters follow the knowledge obtained from industry leaders to produce optimal pipes for several applications.
Components of a Pipe Extrusion Line
From my understanding, a regular HDPE pipe extrusion line typically has several essential units or sections, such as piping equipment with definite technical parameters focused on pipe output:
- Screw Extruder: The extruder is where the HDPE resin might arrive and be oil in liquid form and blended through this section. The extruder incorporates differing length and diameter visitation ratios to length ratios, with an L/D ratio usually of about 24:1 to 36:1, and adequate melting and mixing of the material is also offered.
- Die Head: The head is equipped with a cylindrical die so that the heat-softened polymer is pushed outwards in the shape of a pipe. It is also important to design the die head to avoid inconsistencies in wall thickness or wall shape. The calibration sleeve in this stage is critical in setting the dimensions of the pipe immediately after it has been sported out of the extrusion die.
- Vacuum Calibration Tank: This effect is used in shaping and cooling the pipe. Vacuum is used to pull the pipe in so that a neat shape and smooth surface are attained. Most vacuum tanks are made from stainless steel since it is corrosion-resistant.
- Cooling Tanks: In this component, several additional cooling tanks finalize the ivy to be either moderately Roosevelt or entirely immersed in water spray to harden the pipe further. The rate of hot water removal and the rate of control of water temperature are of high significance in this operation. Standard lengths for such tanks, normally ranging from 6 to 12 meters, are well known.
- Haul-Off Machine: This particular apparatus is meant for the pipe to travel along the line without applying any means of contraction that would change its shape. It works best when synchronized with the pipe output speed, which is rather adjustable between 1 and 25 meters per minute on the regular settings of traction speed.
- Cutter: The cutter cuts regular sections in a pipe with a defined length. Either planetary saws or chipless cutters are used, which promote the balanced optimum dimensions of the pipes and wall thickness in order to produce clean cuts.
All these components combine, and therefore, HDPE pipes possess certain engineering strengths and dimensional, mechanical, and physical flexibility features that justify their integration within infrastructural applications.
The Role of a Single Screw Extruder
The production of thermoplastic materials, such as HDPE pipes, will always carry along the use of single screw extruders. Their main job involves melting and mixing of plastic before they are forced out through the die head. Following are the basic features and the technical specifications of single screw extruders:
1. Function and Applications: Single screw extruders are multifunctional and used for products in which other materials are processed by extrusion. They can effectively mix and pump the molten through the die head and maintain uniformity of the end product.
2. Key Technical Parameters:
- Screw Diameter and Length: Usually, from 25 mm to 150 mm, screw diameters with a screw length-to-diameter ratio of 20:1 to 36:1 affect the production rate as well as the degree of material processing.
- Screw Speed: The screw speed ranges between 10 to 150 revolutions per minute (RPM), sometimes referred to as the rotational speed, which affects the amount and quality of the output, generally the extrusion.
- Temperature Control: Particular and important extruder temperatures allow for the processing of different polymers ranging from room temperature to more than 300 degrees Celsius (570 degrees Fahrenheit). Extruders incorporate such precise temperature zones for different materials and polymers.
- Output Rate: Due to the schnecken Konstruktion and polymer type, the output can usually range from 5 kg/h to over 1000 kg/h, which is suitable for both low-scale and industrial production.
3. Advantages: These extruders are relatively simpler to operate and maintain than any other type, which means they are favorable in the majority of production processes.
These attached elements cooperate to keep the material within the single screw extruder to ensure that it has been properly prepared to achieve the right performance level that meets use in the construction industry.
How to Choose a High-Quality HDPE Pipe Extrusion Line?
In the case of choosing a high-performance HDPE pipe extrusion line, several important factors need to be paid attention to. First, it is the manufacturer’s reputation and whether or not they abide by some quality norms such as ISO, CE, etc. Remember that a vital supplier will give appropriate assistance and training to maximize its operation. Second, such a line should be examined in terms of its technology and features, where advanced automatic controls will be needed for improved performance. Besides that, choose energy-efficient machines, good extruders, die heads, and calibration equipment. Last but not least, factors such as the dead flexible line and upscaling are used to meet different pipe diameters and custom designs. Proper scrutiny of these factors will guarantee the purchase of an excellent quality HDPE pipe extrusion line that satisfies your production requirements.
Critical Factors in Selecting an Extrusion Line
When choosing an extrusion line, aspects such as quality, technology, and technical specifications must be considered to promote optimal engagement in the operations offered. An analysis of the best resources in the industry recommends paying attention to the following three cubical parameters:
- Quality of Components: Most of the internet pages that seek trouble-free business operations include the importance of buying quality extruders, die heads, calibration units, and other tools. Such components must be sourced from certified ISO or CE manufacturers, which guarantees effective retention.
- Advanced Technology and Features: There is a need for modern technology to be brought on board. Always check for extrusion lines that have been automated to a very high level, using energy-efficient materials, processes, and controls. Efficiently operating energy-saving features, energy-efficient materials, and methods can improve efficiency levels significantly. Under this consideration also, the fact that the screw diameter and L/D ratios determine the functional and mating characteristics of the extrusion line must be stated.
- Scalability and Customization: An efficient extrusion line system is anticipated to be firm yet flexible to accommodate different sizes and specifications of pipe products. The capability to vary production conditions to suit diverse specifications and changes in markets ensures that the line grows in line with the business’s needs.
Taking these factors into consideration, plus an uninterrupted guarantee of support from the suppliers and thorough post-purchase support, will help one make an informed judgment concerning the choice of an extrusion line that meets the production objectives as per the industry requirements.
Top Manufacturers of HDPE Pipe Extrusion Lines
In the ever-intensifying competitive landscape, several companies stand out as being among the best providers of HDPE pipe extrusion lines as identified by leading industry resources:
- KraussMaffei Group: Owing to their advanced instrumentation and engineering creativity, the KraussMaffei Group supplies extruders of all sizes and formats incorporating low energy consumption and high-speed automation features. This is because the equipment has intelligent controls that improve the production quality and minimize wastage. On the technical factors, they offer machines with customizable screw diameters as well as L/D ratios that are major for production and need to be long standardization and quality of the production process.
- Cincinnati Extrusion: Cincinnati Extrusion designs strong and multipurpose extrusion HDPE lines suitable for several uses. They are known for machines with solid parts and integration of modern technologies, including control and supervision systems. Among the key technical characteristics are proposed adjustable control units and developed extrusion equipment to increase the technology’s production volumes and vary the manufactured pipes’ sizes.
- Battenfeld-Cincinnati: This manufacturer is a prominent manufacturer of innovative and high-performance extrusion lines used in various HDPE applications. The products by Battenfeld and Cincinnati are very sophisticated as they feature parameters such as power-saving features and operating panels. The distinguishing feature of their extrusion lines is the intricacy of screw design coupled with L/D ratio changeable construction, which enables improved specificity and versatility in the products offered about varying category demands.
Such manufacturers not only supply advanced equipment but also offer many developments and service networks that extend the functioning and enhance the useful lives of HDPE pipe extrusion techniques.
Customization Options for Pipe Production Lines
In the case of manufacturers expanding the pipe production line, a wide array of customization is provided, which can satisfy particular operational and product requirements. As per various credible sources, a few notable customization options are:
- Flexible Screw Configurations: Adjustments to screw diameter and screw length provide the manufacturer with the ability to regulate flow rates and shear processing parameters, therefore allowing the machine to produce different kinds of polymers in diverse amounts.
- Interchangeable Extrusion Heads: Modifications to the design of extrusion heads make it possible to manufacture single- or multiple-layer pipes for different pressures and performance requirements.
- Sophisticated Calibrators: Such apparatus can be carefully tuned so that all the produced pipes have the same dimensions and conform to high-standard requirements.
- Dynamic Control Systems: Monitoring and control systems are applied in the manufacturing process, particularly in the production of polymer pipes, making it easy and effective for workers to work on site with low material spoilage.
- Heat-saving Technologies: The introduction of energy-conserving mechanisms and the use of better insulating materials is expected to reduce the cost of production and mitigate the ecological impact.
- Flexible Production Mould: Customers have production mold options that they can adapt based on demand, whether for small volume or mass production activities.
These technical parameters and features are crucial to the development of high-quality, effective, flexible, and robust processing lines for pipe manufacturing.
Benefits of Using HDPE Pipes
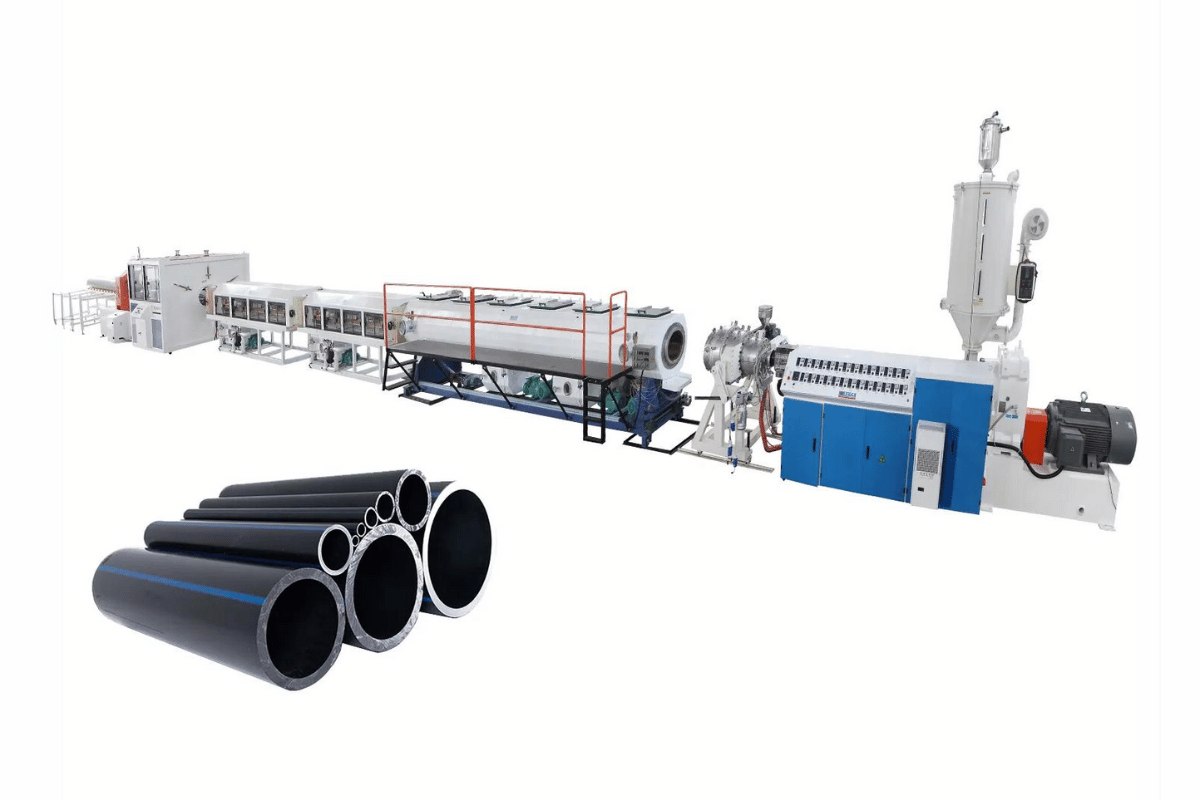
The materials used in piping construction have grown in quality and variety over the years. One such advancement, gaining considerable popularity among engineers and other pipeline users, is introducing and using High-Density Polyethylene (HDPE) pipes in their works. This is mainly due to several reasons. First, they are solid materials with expected serviceability embracing more than fifty years, hence low replacement and maintenance expenses. Furthermore, they are non-corrosive and do not have any biological deposition; therefore, they pose no danger when used to carry clean water. HDPE pipes have good elongations, enabling them to perform under earth movements and vibrations without breaking, which is crucial in regional and active seismic zones. In addition to that, they are chemical resistant, which is appropriate for industries dealing with very toxic substances. They are light and, therefore, easy to transport and install, eliminating cost and time and making them an affordable and very flexible piping system for varied situations.
Durability and Longevity
In order to analyze the wear and service life of HDPE pipes, three factors really stand out in top industry publications: materials, environment, and design considerations.
1. Material Properties:
HDPE pipes need to be siphoned from the DC plugging component. The material has excellent resistance to crack failures and fatigue failure, although the pipes have considerable tensile strength and flexibility. In most scenarios, these properties help increase their life span, and in most cases, the pipes with high-density polyethylene can last for over or approximately a hundred years. The properties of the type of plastic polymer help enhance the moisture without significant chances of hydraulic or water degradation.
2. Environmental Influences:
Environmental concerns include exposure to UV, periodic temperature changes, and soil conditions, among other things that might shorten the life of the pipe. Where the pipes are used above the ground, the UV stability of HDPE is typically improved with added carbon black since the UV-damaged material remains stable even for above-ground use.
3. Design Considerations:
Similarly, industry standards such as ISO 4427 require proper design to choose the right pressure rating and the right wall thickness in relation to pressure, temperature, and surroundings. Considering the fact that there will be changes of distance and temperature enables the pipes to expand free while still intact for many years.
These factors account for the high-density polystyrene pipe, an aspect supported by scientifically proven parameters like tensile strength and environmental stress that make it applicable to long-lasting infrastructure.
Applications in Water Supply and Drainage
Owing to their effective properties and improvement of technology, HDPE pipes are versatile and invaluable to water supply and drainage systems. According to top industry sources, the critical applications are as follows:
1. Water Supply Systems:
- Corrosion Resistance: Unlike metal pipes, which corrode quickly, HDPE pipes do not suffer from internal and external corrosion, thereby allowing long service without changing out or repairing them.
- Flexibility: Their flexibility allows them to be set even in difficult geographical areas without risk of breakage or damage. This versatility reduces the connection between pipes and fittings and the number of places where leaks occur.
2. Drainage Systems:
- Performance in Aggressive Soil and Chemical Resonance: They are not affected by the aggressive soils and chemicals present in stormwater and wastewater applications. This capability to withstand different environmental conditions also prevents pipe failure and assures the system’s reliability.
- Low Resistance to Flow: Due to the smoothness of the HDPE pipes, flow rates are heightened to the extent that choking caused by soil settlement is reduced to manageable levels.
3. Technical Parameters:
- Tensile Strength: This figure is usually within the range of 22-37 MPa as their internal pressure tends to be greater than even the external pressure, rendering them unable to buckle when force is applied to them.
- Thermal Expansion Coefficient: This is normally around 1.5×10^-4/°C, which is a critical factor to consider, especially in installations that frequently undergo temperature changes, thus losing some pressure.
Due to these technical parameters and inherent material strengths, HDPE pipes are reliable in contemporary water supply and drainage structures.
Why HDPE is Preferred for Transportation of Fluids
HDPE, or High-Density Polyethylene, has gained universal acceptance when transporting fluids due to its exceptional strength and reliability. First, the specific feature that allows the plastic to withstand chemical attacks is a factor that makes this material useable in a broad scope, not limited to pipe systems for drug abuse or pipes for industrial effluent. Then, the weathering to be expected from using HDPE pipes is commendable since they do not rust like most metal pipes.
Technical parameters provide further examples of its benefits:
- High Tensile Strength: This property allows HDPE pipes to withstand the pressure of fluid transport without damage, which adds to the operational term of the pipes.
- Flexibility: This material property allows for soil movement and expansion due to temperature changes minimising chances of leaks and rupture.
- Smooth Internal Surface: The surface of the body of HDPE pipes contributes frictional resistance, enabling rapid fluid flow with minimal energy cost.
- Lightweight and Easy Installation: Because HDPE is lightweight, the material is easy to use and install, shipping advantageously with very few items and few workmen.
Such perceptions are evident in the top facts about HDPE, such as from Plastics Pipe Institute, HDPE Pipe & Fittings, and Engineering Toolbox, which advocate that HDPE’s technical and practical benefits warrant its use as a world-class fluid transportation system.
Common Issues and Troubleshooting in HDPE Pipe Extrusion
Numerous difficulties may arise during HDPE pipe extrusion, which can hurt the quality of the produced pipe as well as the efficiency of the process. A typical deficiency is the inconsistency in wall thickness, frequently linked to die misalignment or the speed and temperature of the screw variations. In that regard, examining the orientation of the die and fastening the screws and its settings should be done regularly without fail. This one is also associated with some surface impressions, such as roughness or waviness due to temperature malfunctioning or high extrusion speed. Changing the radiator’s conditions and perfecting the line’s speed would eliminate this defect. Another problem with the final product is melt fracture, which shows itself through the pipes’ irregular or rough surface. Overexerted extrusion pressure also results in surface melt fracture. To do this requires tightening temperature control and unity of movement of the material. Throughout the production process, people observe quality control measures and corrective actions to ensure that standards are maintained in producing HDPE pipes.
Handling Pipe Deformations
Anyhow, recall that in HDPE-pipe systems, there could be deformations in the shape of the pipe. One of the possible reasons for deformations in HDPE pipe systems is improper environmental conditions, poor mound handling, and unsuitable constructional practices. However, website information such as ePlastics, Performance Pipe, and PPI (Plastics Pipe Institute) suggests that preventing and correcting such deformations can be achieved through many strategies:
- Environmental Factors: Increasing or reducing temperatures and UV radiation exposure can cause HDPE pipes to expand or contract. In accordance with ASTM D3035: Standard Specification for the Polyethylene (PE) Pipe, the recommended rules of thermal expansion of the pipes, where limits of temperature and expansion rates are specified, must be adhered to.
- Handling and Installation: For example, incorrect handling or trench bedding forces a bend in the pipe, or the pipe is not circular as it should be, as in ovality. Performance Pipe states that these techniques will assist in reducing the cases of damage due to poor transport and pre-installation practices. If adequate bedding techniques are employed and the backfilled trench is compacted evenly, the deformations are controlled.
- Technical Parameters: An SDR (Standard Dimension Ratio) is one of the most vital parameters. They constitute thin walls that are too susceptible to deformation even with the slightest of stress; higher values of SDR do. It has to be designed pressure-wise, as described in PPI’s design manuals, to avoid transverse and buckling when the pipes are installed. Use of optimum wall thickness as specified by ASTM F714 pipe yes, a pipe standard should also yield low chances of deformation.
Ways and resources have been taken and pointed out, which, if followed, will ensure that the deformations are properly managed.
Managing Extruder Melt and Cooling Processes
Lack of proper coordination of extruder melt and cooling management causes a threat to quality and efficiency. Kelly, Espinosa, and Kiparissides, who represent progressive companies in the polymer extrusion sector such as Nordson, Davis-Standard, and Milacron, all point out that there are several such parameters and techniques as possible designers call them:
- Melt Temperature Control: Melt temperature is also an important parameter that must be carefully monitored to ensure uniformity and avoid material degradation. HDPE’s suggested melt temperature range is 356 to 428 °F, 180 to 220 °C, but that again depends on some additive formulation.
- Screw Design and RPM: The screw geometry and its rpm, and rotation speed are designed to maximize the melting effectiveness and flexibility of the compound. To encourage homogenization and reduced shear heat for HDPE, a low compression ratio screw is mainly preferred.
- Cooling Systems: Adequate cooling methods are crucial to controlling the crystallinity of the extrudate after extrusion. A water bath is one common method applied to cooling pipes to ensure that their shape and strength are retained properly.
Adherence to these and periodic calibration and maintenance of equipment can lower erratic behavior in pipe making. For accurate management of these processes, reference to the instruction texts that primary manufacturers of extrusion technology provide is helpful. This method will ensure the quality and durability of HDPE pipe usage.
Maintaining Consistent Pipe Diameter
It’s always necessary to keep the diameter of the pipes throughout the different components that make up the HDPE pipe design, as it enhances their performance and reliability. Some of the factors involved in accomplishing this include:
- Extrusion Line Calibration: For example, bi-axial spinning should be used as an alternative wobbling sharpening policy to enforce consistency in the pipe diameter improvement suggestions. Frequent checking of alignment and settings can appreciably increase acceptance.
- Pressure Controls: Pipe extrusion involves providing heat and pressure with an extruder’s help, enabling one to create pipes of set duration. Monitoring systems must work and assist in making parameter corrections to avoid breakouts.
- Die Head Configuration: Productions with structural changes to the die head require regular adjustments to reduce variations in pipe cross-section. This is because the die head design and its status affect how the pipe flows and is formed.
- Post-Extrusion Monitoring: Systems designed to measure pipe geometries after extrusion are interlinked, allowing for less delay and a quick response to the need to restore a pipe’s geometrical properties. In such cases, pipes with laser extension systems will be used to increase accuracy.
- Material Consistency: Increasing the size of pipes is very dependent on factors such as the raw and chemical composition that envelopes the molding process and the temperature in each stage of the extrusion process.
All these measures, coupled with the constant enhancement of the parameters and standard procedures in relation to management updates sourced from leading manufacturers of extrusion equipment, allow […]producing organizations to reconcile diameter to different standards in each case.
Innovations and Trends in HDPE Pipe Extrusion Technology
Recent developments in HDPE pipe extrusion technology have been remarkable primarily due to extruders looking for better and more speedy resolutions. One of the prominent achievements includes the development of intelligent extruders. Such systems utilize sophisticated control methods involving sensors and real-time systems that ensure the system’s welfare is being extruded while minimizing waste. A new trend in the concepts uncovered is the introduction of biodegradable materials and additives to the process, which in turn leads to the improvement of the pipes’ self-improving performance. In addition, there is also a continuous integration of automation and robotics in lingering to extrusion systems, demonstrating increased efficiency and enhancing quality. Thus, such technological innovations are improving the efficiency of the processes employed in manufacturing HDPE pipes and transforming the entire industry toward sustainable development.
Advancements in Extrusion Machinery
While wandering through the process of designing an HDPE pipe, one thing can confidently be stated: the extrusion machinery may make further improvements since some pipe parameters seem undervalued or modestly improved. Looking into key sources of information, it is seen that the key enhancements are as follows:
- Advanced Operator Controls and Software: With the advent of advanced technology, hoạt động process control in extrusion machines has achieved a modern feat of modifying operating parameters like temperature and pressure, which optimizes operations in real-time. This principle helps maintain the production quality while reducing the cost of raw materials.
- Updated Cooling Methods: The enhanced cooling helps maintain the shape and mechanical properties of the pipes. Enhanced formation of a cold layer control during the process is already covered by the presence of various external high-strength air-cooling or water-bath systems, which shorten the cycle and increase the rate of production.
- Green and Efficient Motors: These new advanced extrusion apparatuses equip a highly efficient electrical energy system, which has greatly reduced power usage during machine operation. Such low operational costs and power systems are both eco-friendly and energy-saving methods of reaching sustainability in production.
In this way, extrusion machinery manufacturers and suppliers can respond to the growing market for ecologically friendly and li, newest generation pipes and be successful in troubleshooting pipe making on industrial struggles and in synergetic processes works to the worldwide geep—and energy-saving technology needs.
Modular Designs and Their Benefits
Due to its emphasis on flexibility, efficiency, and several other reasons that should be covered in a later section, modular design in HDPE pipeline extrusion machines has several benefits. Several vital sources speak of advantages as follows:
- Customization and Flexibility: Because machinery has a modular design, manufacturers can easily change the setting of the machinery according to changes in production needs, which does not lead to excessive downtime. This adaptability is important in meeting the various demands of the clients and increasing or reducing the output as necessary.
- Reduced Maintenance and Downtime: When modular and fiber optic networks are renovated, particular system components can be changed without rendering the entire machinery unserviceable. This method not only shortens the maintenance period but also improves the general performance of the operations, culminating in increased output.
- Cost Efficiency: Because modular designs enable carrying out the desired modification and repairs, they can, therefore, help lower the effects of future construction costs. They are advantageous in that industries will purchase parts of the different systems only when they require their use.
Technical Parameters:
- Interchangeable Parts: Manufacturers are encouraged to use common parts in modular designs for different products to promote easy incorporation into assembly lines.
- Retrofitting Capabilities: The design of these systems enables them to be built in a manner that makes them updateable without major reconstruction.
- Scalability: Modular machinery creates elastic production lines, as other units or capabilities may be added to fulfill the changing production requirements.
Incorporating modular design helps make manufacturing processes more efficient and is also in accordance with resource management principles that promote the reduction of waste.
Future Directions in the Pipe Extrusion Industry
In the coming years, the pipe extrusion sector will have even more reasons to be optimistic about embracing more advanced and eco-friendly production techniques. The fourth industrial revolution, where IoT and AI, among other technologies, find application in manufacturing, is rapidly progressing. This helps in better predicting and monitoring equipment and system functionality, thus minimizing downtime and enhancing work efficiency.
There is also an increasing trend towards the use of eco-friendly materials and processes. The industry is looking for alternative materials that can address the impact of plastic pipes. In this regard, there is an increasing demand for bio-based polymers and less energy-intensive forms of production.
Moreover, the evolution of technologies concerning automation and robotics is going to change the extrusion process of pipes. With a more efficient organizational structure, the company’s operations are performed by a smaller workforce and with greater accuracy and stability, reducing labor costs and enhancing the quality of the output.
Technical Parameters:
- Internet of Things: A method of enhancing productivity by installing smart devices for information gathering and production-related data analysis.
- Artificial Intelligence applications in production: Use machine learning to suggest repairing time or suggest process modifications to improve how the machine operates and how long it will last.
- Biodegradable materials: Plastic materials that are biologically synthesized and polymerized and other procedures to minimize plastic usage are often used in the production.
- Robotics Technology: Replacement of manual work with robotic technology to improve accuracy and reduce dependency on manpower.
These directions are indicative of the industry’s commitment to technology growth and environmental protection as prerequisites to future growth.
Frequently Asked Questions (FAQs)
What is the role of IoT in the pipe production industry?
The Internet of Things (IoT) is utilized in the pipe production industry to enable real-time monitoring and data collection from various stages of the manufacturing process. This allows for optimized production, enhanced maintenance schedules, and reduced unexpected downtimes, improving overall efficiency and product quality.
How does artificial intelligence (AI) enhance the production process?
AI is used for predictive maintenance and providing process recommendations to improve machinery performance. By analyzing data patterns and predicting potential issues before they occur, AI helps minimize maintenance costs and extend the lifespan of equipment.
What are some examples of sustainable materials used in the industry?
The industry is moving towards utilizing biodegradable and recyclable materials, such as bio-based polymers, to reduce the environmental footprint. These materials are designed to break down quickly and efficiently, minimizing waste and conserving resources.
How is automation transforming pipe extrusion?
Automation in the pipe extrusion process introduces robotic systems that offer high precision and consistency in production. This reduces the need for manual labor and reduces production costs while enhancing the quality and uniformity of the final products.
What are the benefits of integrating advanced robotics in manufacturing?
Advanced robotics improve production accuracy, ensure consistency, and boost overall efficiency. This integration allows for faster production cycles, reduced human errors, and significant cost savings, positioning the industry for competitive advantage.