High-density polyethylene (HDPE) pipe fittings are a critical component in modern piping systems, renowned for their resilience, flexibility, and cost-effectiveness. This guide is designed to provide a comprehensive overview of HDPE pipe fittings, examining how they function, their applications across various industries, and the key advantages they offer over traditional materials. From understanding the properties of HDPE to exploring different types of fittings and their installation methods, this article will equip readers with the knowledge needed to make informed decisions for their projects.
What are HDPE pipe fittings and why are they important?
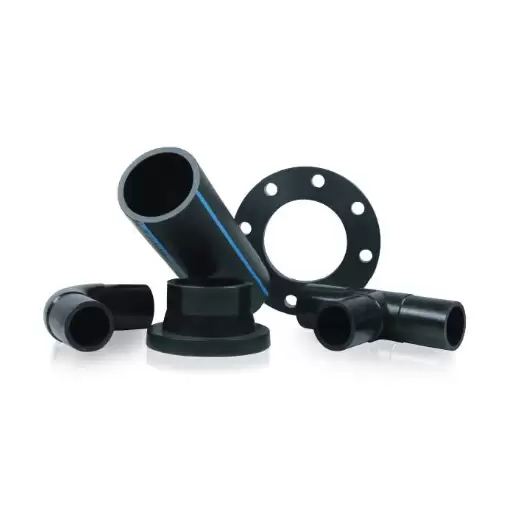
Understanding the basics of HDPE pipe fittings
HDPE pipe fittings are components manufactured from High-Density Polyethylene (HDPE), a robust and flexible thermoplastic material known for its high strength-to-density ratio. These fittings are critical for creating secure and durable connections in piping systems used in water supply, gas distribution, sewage systems, and industrial applications. They serve as the junctions, transitions, and terminators in pipeline configurations, enabling smooth transmission of fluids under various operational conditions.
- Density: HDPE has a density range of approximately 0.93–0.97 g/cm³, offering lightweight yet reliable structural integrity.
- Thermal Resistance: Capable of withstanding temperatures from -40°F to 140°F (-40°C to 60°C), making them suitable for diverse environmental conditions.
- Pressure Ratings: Common pressure ratings include SDR 11 and SDR 17, supporting 160 PSI and 100 PSI respectively for water applications, ensuring adaptability to high and low-pressure systems.
- Corrosion Resistance: HDPE is resistant to chemicals, corrosion, and biological degradation, ensuring longevity even in harsh operational environments.
- Flexural Modulus: Typically ranging from 0.8 to 1.5 GPa, which provides the material with flexibility under stress while maintaining its shape.
These characteristics make HDPE pipe fittings crucial for reliable, cost-effective, and environmentally safe pipeline solutions.
Key benefits of using HDPE fittings in piping systems
- Durability and Longevity: HDPE fittings have a service life of more than 50 years under normal situations thanks to their resistance to abrasion, impact, and environmental stress cracking.
- Lightweight and Flexible: Compared to metals, HDPE fittings are lighter, which consequently minimizes transportation and installation expenses. Also, they are flexible enough to be bent with a radius of up to 20 times the outer diameter of the pipe, making them easier to incorporate into intricate piping designs.
- Leak-Free Connections: With fusion welding processes like butt fusion and electrofusion, reliable and leak-tight joints are made which minimizes the possibility of losing or contaminating water.
- High Chemical Resistance: As a consequence of being highly resistant to various acids, bases, and other organic compounds, HDPE fittings are perfect for industrial uses that involve aggressive chemicals.
- Pressure Rating: Depending on the standard, HDPE fittings can withstand pressures of as high as 25 bar at 20 degrees Celsius. This makes the fittings perfectly adequate for high-pressure systems.
- Environmental Sustainability: With a carbon footprint that is incomparable to that of traditional materials such as concrete and steel, HDPE is 100% recyclable which further solidifies its relationship with sustainable development.
These technical advantages highlight HDPE fittings as a critical component for modern piping solutions that emphasize reliability, efficiency, and environmental responsibility.
Comparing HDPE fittings to other materials like PVC and steel
Numerous core considerations are given to material properties when comparing what service HDPE fittings provide in contrast to PVC and steel HDPE services.
- Durability: Regarding corrosion, abrasion, and chemical exposure HDPE fittings outperform all alternatives. Furthermore, unlike steel, HDPE works better in places that have high acidity or moisture. PVC can corrode, but its resistance is only helpful when impacts are minimal and UV exposure is limited. On the other hand, steel fittings are solid, but rusty when not maintained well.
- Flexibility and Strength: The HDPE ductility property gives it the strength to undergo significant ground movement without rupture caused by vibrations. Unlike steel, which is rigid and creates numerous issues in seismic HDPE applications due to joint failure, HDPE has better performance. In comparison to HDPE, PVC is strictly non-uniform and cannot bend or shift without breaking.
- Weight and Installation: Since HDPE is the lightest out of all alternatives, it is by far the most cost-effective, reducing both time and labor for transportation and installation. Additionally, whereas PVC is lightweight too, it does not provide effective support under high-pressure systems which affects its usage. Similarly, steel is heavy and constrains the application of HDPE because it increases both the cost and time required for installation.
- Sustainability: The biggest advantage of HDPE fittings is the lower-value energy eliminates all forms of waste associated with production. In contrast, steel is much more energy-consuming because it requires waste recycling and PVC has controversial environmental problems because of its production and waste disposal processes.
Overall, HDPE fittings stand out due to their adaptability, cost-efficiency, and reduced environmental impact, making them a preferable choice for many modern engineering applications.
How do I choose the right HDPE fittings for my project?
Factors to consider when selecting HDPE pipe fittings
In the choice of HDPE pipe fittings for the materials of my project, I pay close attention to several considerations that determine how the pipe performs and its durability.
- Pipe Size and Dimensions: Like any construction project, I look at the measurements for the pipes such as their diameter and wall thickness (SDR ratings), which will determine their compatibility with the fittings. The fitting selected should conform to the pipe dimension to sustain the system requirements.
- Pressure Rating: the requirements for the pressure in the system are evaluated together with the rating of the pipe fittings (e.g., PN10 or PN16). This is done to ascertain whether the system can work with the operating pressure set without system failure.
- Environmental Conditions: I look at the application environment ceiling such as the temperature extremes, UV exposure, and chemicals. For instance, an HDPE’s operating temperature is commonly considered to be between -40˚F to 140˚F and it also exhibits great resistance to most chemicals.
- Jointing Method: Depending on the method of installation, I will select electrofusion, butt fusion, or mechanical fittings. These methods have their benefits and are meant for different approaches to the project.
- Standards and Certifications: Within the fittings, I check if they are compliant with industry standards such as ASTM, ISO or AWWA for performance and quality standards.
- Cost and Availability: I evaluate the effectiveness of the fittings in terms of their cost without compromising on quality and make sure that they are available on time to meet the schedule.
By reviewing these factors given the project specifications and environmental limitations, I select the HDPE fittings that are optimal for the project.
Common types of HDPE fittings and their applications
- Electrofusion Fittings: This specific type of piping fitting is used in gas and water piping systems which require high pressure and high temperature conditions. Its construction consists of a pipe with a built-in electric coil and piping fittings, which heat a closed cavity containing the part.
- Butt Fusion Fittings: Large bore pipework utilized in water and gas systems uses these fittings to create joints resting at high pressure. They offer long-term connection and embedment in the pipe network. These fittings are bonded under 200 to 220 degrees Celsius, therefore, precise temperature management tools are recommended for use with SDR11 and SDR17 pipes.
- Flange Adapters and Backing Rings: This fitting creates detachable connections, especially for valve and pump connections. Compliant with ANSI B16.5 and ISO 9624 standards, these flange adapters are designed for use with mechanical structures of various pressure classes such as PN 10, PN16, and Class 150.
- Reducing Tees and Reducers: Often used in pipeline systems with lower pressure requirements and higher cross-section changes, these parts are crucial for regulating flow in a piping system. Reliable service compliance requires the proper selection of these parts based on flow and pressure drop coefficients, making ISO 4427 the standard for dimensions.
- Compression Fittings: These fittings are quite popular in irrigation and low-pressure systems as they can easily be installed without using any tools. They usually have a standard pressure rating of 10 bar and are manufactured by ISO 17885.
Resources that include fittings are selected based on how much pressure, temperature, mechanical strength, and ease of installation there is for each specific project. Each fitting serves an operational purpose which ensures compliance to the standards.
What are the different methods for joining HDPE pipe fittings?
Butt fusion: The most common method for large-diameter pipes
A butt fusion machine can heat and fuse the ends of HDPE pipes using specialized equipment. This approach is extremely effective in achieving joints in large pipes which are usually used with water, gas, or even in some industrial applications. The procedure involves the heating of pipe ends through the use of a heating plate which softens the material. The two ends are pressed together at a controlled temperature which is maintained during fusion so that the material cools down and hardens completely.
- Alignment Tolerance: Joints can only have less than 10% of the wall thickness of the pipe in alignment discrepancy to have structural integrity.
- Heating Plate Temperature: Recommended heat for the plates is usually between 400 – 450 °F (204 – 232°C), depending on the condition of the environment and the grade of the material.
- Fusion Pressure: When fusing, pressure should always remain between 20 to 30 PSI (1.4 to 2.1 Bar) per manufacturer specifications.
- Cooling Time: Time must be allowed for cooling depending on the size of the pipe and temperature, but an adequate amount ensures that the joint has full strength before being handled.
Since girders and other structural elements pose considerable loading on ductile iron pipes, butt fusion is always the best and safest method. It is cheap, reliable, and meets international standards such as ASTM F2620 which is why it is preferred for important infrastructure works.
Electrofusion: A reliable option for tight spaces and repairs
Electrofusion, an innovative and advanced method of joining polyethylene pipes, involves the application of an electric current through a coil within a fitting. The current produces heat which melts the fitting and the tip of the pipe, resulting in a strong and leak-free joint. While butt fusion is effective, electrofusion does prove to be more efficient in achieving exact repairs in tight spaces.
- Voltage Range: Various fittings may vary depending on the specification, but 40-48 volts is the typical range.
- Heating time: Depends on the electrified pipe diameter. Generally, the time ranges from 60 seconds to 240 seconds and the duration is preset using the electrofusion processor.
- Cooling time: Cooling is imperative to assure joint strength and generally cools down from 10 to 20 minutes while taking the pipe diameter and environment into account.
- Alignment: The pipes have to hold within ø1° to prevent weak joints while complying with ISO 12176-1 standards.
Electrofusion is a go-to in applications in high-precision fields like pipeline repairs or installations within tight places. Meeting all the guidelines implies that electrofusion also meets standards like ASTM F1290 and EN 12201-03, ensuring the desired performance criteria is using all the required durable operational conditions.
How do I properly install HDPE pipe fittings?
Essential tools and equipment for HDPE fitting installation
The following tools and equipment are crucial for the correct fitting of HDPE pipes:
- Pipe Cutters or Saws: The HDPE pipes are cut using these tools and the length should be precise. Always ensure that the tools used make straight and clean cuts as it is pivotal for the joint’s strength.
- Pipe Scrapers or Peelers: This tool removes any oxidized material from the surface of the pipe as it is critical for strong electrofusion bonds
- Electrofusion Machine: This machine is used during welding and it does two things simultaneously: apply heat and current.
- Alignment Clamps: These will hold pipes in position during welding to avoid angular displacement.
- Power Generator: A generator serves as a power source for sites where electricity is hard to come by, allowing for the electrofusion machine to operate.
- Marking Tools: These are markers that allow the measuring and marking of correct depths to which fittings should be inserted.
- Personal Protective Equipment (PPE): For the installer, items such as gloves, eye protection, and clothing that can withstand high temperatures are heat shielding the installer from harm during heat-based processes.
So, in conjunction with all relevant standards compliance like EN 12201, ASTM F1290, and ISO 12176, proper installation of the HDPE fittings requires an outlined process which will, if followed in conjunction with the apparatus above, minimize the installation errors and provide optimal system effectiveness, performance and strive towards simple, yet durable system structures.
Tips for ensuring leak-free connections in HDPE piping systems
Following specific installation methods is important to achieve leak-free joints in HDPE piping. In addition, the following considerations need to be fulfilled.
- Pipes and Fittings Preparation: Always remember that the pipe ends and fittings are clean, devoid of any grime, and dry before the process of fusion is purposed. McGrime can serve as a contaminant wherein they can put weak points that will affect the integrity of the bond. Employ HDPE-specific cleaning products, like isopropyl alcohol and lint-free rags, for better results.
- Proper Alignment: During pipe fusion, using these parameters guarantees the joints are even and placed correctly, thus avoiding any chances of leakage. Use pipe alignment clamps or welding jigs for accurate alignment. This guarantees that the molten metal flows evenly during fusion and prevents voids from being created in the joined area.
- Joint Quality Inspection: After installation, visually assess the joint to confirm that the strength of the joint is more than that of the adjoining welded pipes. A bead of higher strength and proper form shows a proper fusion made, while irregular and incomplete beads suggest the need for amputations.
- Gauge Test: Perform a hydrostatic pressure test or a pneumatic test to know the amount of leakage in the system after installation. Most popular standards set in ISO 4427 dictate a test measure of 1.5 times the working parameter for 4 to 24 hours to check for leaks.
After following these steps and justifying parameters as per field standards, you are ensured a robust and leak-free HDPE piping system that is within industry specifications.
What are the best practices for maintaining HDPE pipe fittings?
Routine inspection and maintenance of HDPE fittings
Periodic examinations and repairs of HDPE fittings, and maintenance, are both essential to achieving optimal performance as well as preserving the integrity of the piping system throughout its planned life cycle. To sustain the long lifespan of the system, it is important to routinely conduct inspections that examine the cracks and bends and even the color of the system as it works internally. Such extremes could hint at UV degradation, excess pressure internally, or stress through the environment. The debris and chemical residues have to be cleansed consistently otherwise it can corrupt the joint integrity.
Secondly, for mechanical joints check the Fitting and any coupling components for tightness. Check connections, as loose Fittings can create situations where the system fails, and if there is over-tightening then the fittings could break. There should be no signs of leaking at fitting connections, which is done by first applying some pressure on the system to test its operating capability, by the system and more importantly the ISO and ASTM standards.
Moreover, check that no wrongly applied loads are there in the form of bending or tensile stresses that would lead to system malfunction, and, if need be, pre-mature failure. Each inspection must be recorded carefully and always contains a set of performing thorough maintenance by the manufacturer’s instructions. For those piping systems to work properly, these guides must be followed to maintain any HDPE piping system and improve performance on the life of the system.
Addressing common issues with HDPE pipe connections
One of the more prominent concerns is the misalignment of joints which sometimes stems from poor handling or even a lack of adequate preparations before installation. In this case, I tend to clean all the pipe ends and ensure they are devoid of any debris. Moreover, I make sure that the ends are cut square and that they can align properly. Furthermore, I also check whether the assembly procedure follows relevant industry standards like the ASTM D2657 for butt fusion or the ASTM F1055 for electrofusion.
Also, leakage or pressure loss at the joints is another challenge. For this, I perform pressure testing in line with the ASTM F2164 standards. Of importance is to ensure the test pressure does not exceed 1.5 times the system design pressure. For most pours and plants that make use of HDPE, the test pressure usually rests between 150 and 200 psi based on the particulars of the system and the operational conditions in place.
A stress crack or premature failure is often caused by overburden loading or tensile stress, and for the less sophisticated cracks, it’s noticeable more often. To alleviate this, I ensure that I keep my eyes on the environmental factors and am confident that the installation of the pipe satisfies the recommendations from the manufacturer’s side specifically the burial depth which varies from site to site but commonly varies between 24-48 inches below grade and the backfill used in the trench.
By combining these methods with the calculation of the prescribed technical, I quite effectively reduce issues while ensuring that the system’s operational reliability is not compromised.
Extending the lifespan of your HDPE piping system
The HDPE piping system’s lifespan can be qualified tested based on properly followed design, installation, and maintenance procedures that comply with industry standards. In this case, the selection of pipe grade is done by correlating the material’s pressure rating SDR class with the system’s operating pressure and temperature for the correct selection of pipe grade. Moreover, industry standards regarding overburden stress mitigation are always followed by observing manufacturer suggestions on burial depths, which bottom out between 24 and 48 inches depending on the pipe diameter and type of soil.
As for joint integrity, butt and electro-fusion are compliant and dependable methods I employ for establishing leak-proof joint connections alongside other jointing activities. Regular pressure testing assists in verifying system integrity under ASTM F2164 guidelines. Test pressures are kept below 1.5 times the system’s design pressure to ensure the system is operational. In normal circumstances, test pressures are anywhere between 150 to 200 psi.
To reduce the risk of stress cracking, my point of focus is on the tensile stresses produced by the environment or operational factors. This encompasses the Backfill quality such as the indentation grade that can sharp stones or debris engage in. Such items should not be included. Moreover, I take account of the soil movement and the thermal expansion and contraction while I design the expansion joints or flexible connections.
By taking these measures and utilizing the known technical rules, I attend to critical matters in the right way, but in the process, I also make sure that the performance and reliability of the HDPE piping systems over time is not compromised.
Reference sources
Frequently Asked Questions (FAQs)
Q: What are HDPE pipe fittings and why are they commonly used?
A: HDPE (High-Density Polyethylene) pipe fittings are connectors and components used to join HDPE pipes. They are commonly used due to their excellent durability, chemical resistance, and flexibility. HDPE fittings are ideal for various applications, including water supply, gas distribution, and industrial piping systems, as they offer superior performance and longevity compared to traditional materials.
Q: What are the main types of HDPE pipe fittings available?
A: HDPE pipe fittings come in various categories, including couplings, adapters, elbows, tees, reducers, and caps. Specialty fittings such as flanges, stub ends, and fabricated fittings are also available. Each type serves a specific purpose in creating a complete piping system, allowing for changes in direction, size, or connection to different materials.
Q: How are HDPE pipe fittings joined together?
A: HDPE pipe fittings can be joined using several connection methods. The most common techniques include heat fusion (butt fusion, socket fusion, and electrofusion), mechanical coupling, and threaded connections. Heat fusion is particularly popular as it creates a strong, leak-proof joint by melting and fusing the pipe and fitting materials.
Q: What is the difference between molded and fabricated HDPE fittings?
A: Molded HDPE fittings are manufactured using injection molding techniques, resulting in consistent, high-quality products suitable for standard sizes and configurations. Fabricated fittings, on the other hand, are custom-made by cutting, shaping, and joining HDPE pipe segments. Fabricated fittings offer more flexibility for unique or large-diameter applications but may have slightly lower pressure ratings compared to molded fittings.
Q: How do I select the right SDR (Standard Dimension Ratio) for HDPE pipe fittings?
A: Selecting the correct SDR is crucial for ensuring your HDPE pipe fittings can withstand the required pressure. SDR is the ratio of pipe diameter to wall thickness. A lower SDR number indicates a thicker wall and a higher pressure rating. Consider factors such as operating pressure, temperature, and the specific application when choosing the appropriate SDR. Consult with a supplier or expert for recommendations based on your project’s requirements.
Q: Are HDPE pipe fittings suitable for electrical conduit applications?
A: Yes, HDPE pipe fittings are suitable for electrical conduit applications. Their durability, corrosion resistance, and flexibility make them an excellent choice for protecting electrical wires and cables. HDPE fittings used in electrical applications are typically black with a red stripe to indicate their use as electrical conduits. Always ensure that the fittings meet local electrical codes and standards.
Q: How can I achieve cost savings when using HDPE pipe fittings?
A: To achieve cost savings with HDPE pipe fittings, consider the following strategies: 1) Use fusion joining methods to reduce the need for mechanical fittings, 2) Opt for fabricated fittings for large or custom applications, 3) Choose a reliable supplier with competitive pricing and bulk order discounts, 4) Rent fusion equipment instead of purchasing if it’s not frequently used, and 5) Properly design your system to minimize the number of fittings required while maintaining efficiency.
Q: What expertise is required for installing HDPE pipe fittings?
A: Installing HDPE pipe fittings requires specific expertise, particularly when using fusion joining methods. Technicians should be trained in proper fusion techniques, including the use of fusion equipment and understanding of fusion parameters. Knowledge of pressure testing, system design, and local codes is also essential. Many suppliers offer training programs or can recommend certified installers to ensure proper installation and long-term system performance.