High-density polyethylene (HDPE) pipes are widely recognized for their durability, flexibility, and cost-efficiency, making them a preferred choice for various industries, including water distribution, gas transmission, and industrial applications. Understanding the costs associated with HDPE pipes, including material prices and installation expenses, is critical for project planning and budgeting. This guide provides a comprehensive breakdown of HDPE pipe costs, covering price lists based on pipe dimensions, material grades, and supplier variations, as well as an in-depth examination of the factors impacting installation costs, such as site preparation, labor requirements, and specialized equipment.
What Factors Affect HDPE Pipe Prices?
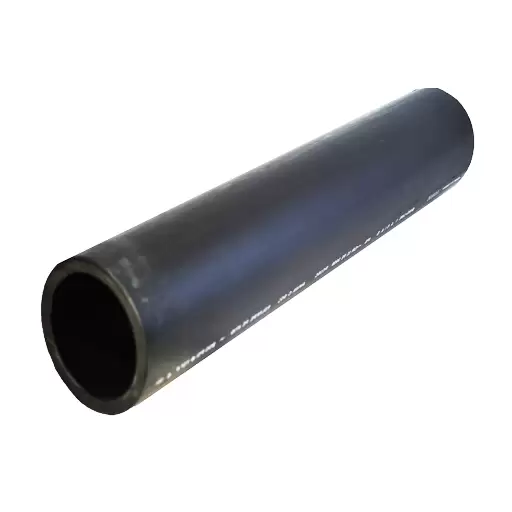
How Size and Wall Thickness Impact HDPE Pipe Cost
The cost of HDPE pipes increases significantly alongside its diameter and wall thickness as those features dictate the amount of material needed for manufacturing. Thicker wall dimensions require greater amounts of raw HDPE resin, which means increased costs in pipe diameters greater than 12 inches – which is thicker than 2-inch pipes.
- Pipe diameter: Most 2-inch and 6-inch pipes are relatively cheaper than those of larger diameters.
- Wall thickness: SDR 11 pipes are thicker than SDR 17 pipes and therefore more expensive due to the greater amount of materials needed for construction.
The use of these factors is warranted based on abrasion economics or operational needs since greater diameter and wall thickness are more often than not correlated with greater pressure requirements.
How Material Grade and Quality Influence Price
These factors greatly impact the durability and performance. Therefore, the material grade and quality of a pipe have a direct relation to its cost. For instance, PE100 and PE4710 grade materials used in polyethylene pipes have exceptional characteristics such as enhanced mechanical properties of hydrostatic strength and resistance to environmental stress cracking. Even though these materials are best fitted for high-pressure uses, they increase the cost of production because of the sophisticated manufacturing processes, raw materials needed, and high costs of production.
- Molecular Weight: When it comes to highly graded pipes, these materials tend to have a high number of grade components which means that other elementary components are much more dominant. In addition, the components add great expense to the overall production complexity.
- Density and Flexural Modulus: Higher-density materials such as HDPE pipes have added strength under pressure and increased rigidity, then they would be more expensive as well.
- Resistance to Corrosion and Chemicals: Treatment or formulation of materials in manufacturing them with enhanced resistance to chemicals or corrosion does increase cost as well.
In the end, the balance achieved between requirements in application and quality determines cost, while the operational demands such as temperature, pressure, and the medium being transported determine the selection of material grade.
Why Location and Shipping Affect Your Final HDPE Pipe Cost
Given the costs of transportation, logistics, and regional pricing variations, the location of the buyer and the shipping services required have a huge influence on the cost of HDPE pipes. For example, greater distances result in higher costs attributed to freight because of fuel pricing, shipment modes (truck, rail, or sea), and volumetric freight.
- Pipe Dimensions and Weight: Increased shipping costs are proportional to heavier shipping and the volumetric space occupied, whether the walls are thicker or the diameters are larger.
- Batch Size: Per-unit shipping costs are lower in bulk for consolidated shipments, thus, economically efficient in transporting.
- Distance and Transportation Mode: For very long distances cost may be lower for freight via rail or sea when compared to trucking, however, time for delivery will vary.
- Special Handling Requirements: Cost is directly affected due to pipes that need to be climate-controlled or more protective packaging.
It is possible to source from suppliers nearby for material and shipment quality, which greatly reduces procurement costs while maintaining efficient order quantity.
How Much Does HDPE Pipe Cost Per Foot?
Cost Comparison Between Standard and High-Density Polyethylene Pipes
Some approaches can be taken into account while estimating the pricing of conventional polyethylene pipes about high-density polyethylene (HDPE) pipes. Standard polyethylene pipes are generally cheaper on a per-unit basis because they are less complicated to manufacture and have a lower material weight. Yet, high-density polyethylene (HDPE) pipes are more expensive because they offer greater durability, longevity, and resistance to extremely high and low temperatures and pressure.
- Maximum Pressure: Excluding the wall thickness and width, HDPE pipes have a maximum pressure of 150 PSI making them greatly useful in high-pressure applications.
- Heat Deflection: HDPE pipes also have a great strength from temperatures of -40 to 140F degrees ensuring harsh weather conditions damaging them.
- Impact Resistance: Compared to standard pipes, HDPE pipes have greatly superior impact strength and therefore can withstand shocks during movement and setting up the pipes.
- Service Life: In the case of HDPE pipes, their longevity of service life which ranges between 50 to 100 years notably exceeds that of typical polyethylene pipes which is lesser than HDPE pipe’s scope of application.
Although standard polyethylene pipes can be used in non-demanding situations, high-definition polyethylene pipes are more economical in the long run and useful because of their strength and flexibility.
Price Variations Between Different Brands and Manufacturers
Examining price differences between various brands or manufacturers of HDPE pipes requires a careful analysis of certain technical features to rationalize the price gaps. For instance, different brands vary in the quality of raw materials utilized most especially the grade of polyethylene resin which determines the pipe’s ability to withstand tensile stress, flexibly bend, and endure environmental stress crack damage. Expensive, higher-grade materials naturally cost more but perform much better.
Moreover, the precision of the extrusion and the enforcement of quality control can lead to price differentials. Responsible manufacturers are always guided by stringent requirements like ISO 4427 or ASTM D3350 that guarantee accuracy in the dimensions and a longer useful life. The wall thickness of the pipe (sits under SDR or Standard Dimension Ratio) is another cost component, pipes with low SDR values are thicker and have higher rated pressure limits, which explains their expense.
Finally, exposure to various brands of pipes results in differing prices due to changes in mark UV protection additives and chemical resistance coating, along with other post-manufacturing treatments like annealing for stress relief.
What Are the Installation Costs for HDPE Pipe Projects?
Equipment and Fusion Welding Costs for HDPE Installation
In terms of costs related to equipment and hydraulic pipeline installation, my approach considers several elements. Fusion machine butt, electro, and socket fusion are a prerequisite issue isolating specification and rental availability. The selection between these fusion machines is based on pipe diameter and joint type requirements. For instance:
- Butt Fusion Machines: These fusion machines have a reliability rate of ideal for pipes with 4-plus-inch diameters. Their costs range depending on the machine’s capacity which is usually between $5,000 and $20,000.
- Electrofusion Machines: They tend to be the cheaper option and are preferred when fittings are required or during installations in compacted areas. Their prices average between $1,500 and $6,000.
- Socket Fusion Tools: These tools are for the smaller under 4-inch diameter pipes, they are socket fusion tools so their price is between $300 and $2,000.
Electric saws also known as pipe cutters, alignment clamps, and electric saws are ancillary equipment I also account for functioning to ensure the fusion welds are accurate and precise. Their cost is important because trained operators have to idle at precise temp, pressure, and timing for joined integrity on opt. This comprehensive analysis assists in tailoring the equipment mitigating project costs without sacrificing quality.
Labor Rates for Professional HDPE Pipe Installation
The charges associated with the professional installation of HDPE piping vary with the skill level, local labor market, and how intricate the installation job is. From what I know, highly skilled workers normally charge between $50 and $150 for their services across the board. The accurate execution of the various fusions, along with the preservation of the required parameters for optimal joint integrity, explains the difficulty associated with the execution of these costs.
- Temperature: Surfaces that are to be fused are heated to approximately 204 degrees Celsius to allow the required melting and bonding to take place.
- Pressure: A certain force must be applied in the joining process in order for proper bead agglomeration to take place.
- Timing: Complying with the specified times for heating and cooling by the manufacturer guarantees that the joint is sound.
These factors must always be taken in conjunction with the survivability and the functionality of the final installed structure; hence, operators must go through specific training and contractors must factor in the cost of skilled hands. With all in place, I make sure that the project is completed without sacrificing quality standards while being done in the most efficient manner possible.
How Does HDPE Pipe Compare to Other Piping Materials?
Cost Comparison: HDPE vs. Concrete and Other Popular Choices
It is important to analyze both the initial costs incurred as well as the economic benefits in the long run when evaluating the pricing of HDPE pipes in contrast to Concrete pipes, and other popular piping materials. Although the material cost of these HDPE pipes is much higher than that of the concrete-priced pipes, concrete pipes may save significant money over time due to lower installation expenses as well as decreased overall maintenance requirements. Additionally, savings can further be improved on the pipes due to their lightweight characteristics which enable easier handling and transportation.
- Installation Costs: Unlike concrete pipes, which require movement and placement of specialized equipment, HDPE pipes can be installed without heavy machinery to manipulate them. Not only does this procedure save on labor expenditures, but it also leads to quicker turnaround times for projects.
- Hydraulic Efficiency: It is much easier for a smaller diameter pipe capable of controlling the same volume of water to be utilized due to the smooth inner surface of HDPE pipes compared to concrete pipes, so much smoother is the internal surface of HDPE pipes (Manning’s coefficient of 0.009).
- Hydraulic Efficiency: As previously stated, HDPE pipes provide a much smoother flow compared to concrete pipes (Manning’s coefficient of 0.012-0.015).
- Longevity and Durability: Unlike concrete pipes that undergo steady corrosion-splitting over time, HDPE pipes have been known to sustain a life system of more than 50 years even in hostile soil and flow conditions.
- Maintenance Expenses: The ongoing maintenance requirements in terms of expenses between HDPE and concrete pipes are much more cost-efficient as HDPE pipes do not easily fall prey to chemical attacks, scaling, and deposition.
Considering these variables, I endorse the use of HDPE pipes for projects that value longevity, low maintenance, and ease of installation, external factors of the project.
Long-Term Cost Benefits of High-Quality HDPE Pipes
- Less Maintenance: With HDPE Pipes, Operational interruptions and ongoing maintenance along with costs can be significantly decreased due to the outstanding resistance to chemical corrosion, scaling, and deposition of these pipes. This durability can be quantified through their low abrasion coefficient (approximately 0.009-0.015) which greatly minimizes the wear and tear in high-velocity flow systems.
- Increased Life Span: Even under unfavorable soil and flow conditions, the lifespan of HDPE pipes exceeds fifty years. This is much higher than the average durability of traditional materials which means lower replacement intervals and lesser capital expenditures over time.
- Reduced Energy Costs: The smooth inner surface coupled with a low friction factor (Manning’s “n” = 0.009) allows fluid to flow with ease through HDPE Pipes. This allows for a reduction in the amount of energy that needs to be used for pumping overtime which in turn reduces expenses operationally and energy-wise.
- Streamlined Installation Process: The ability to seamlessly fuse alongside them being lightweight makes these pipes much easier to install. Fewer leaks at the joints also mean lower installation costs and time, especially with large-scale construction projects.
In light of these factors, I recommend utilizing highly durable HDPE pipes in particular projects that seek to maximize long-term economic and operational value. As long as the associated friction and the pipes’ lifetime offer a balance of value, their technical durability, confirms their reliability over time.
Performance and Durability Factors That Justify Higher Price
The features, durability, and performance that justify the elevated price of the HDPE pipes include their outstanding resistance to environmental stress cracking, exceptional toughness, and long service life. These pipes have been designed to function at high pressures and extreme temperatures which is crucial in more demanding functions.
- Stress Crack Resistance (SCR): HDPE pipes distinctly possess high SCR which guarantees that there is no catastrophic failure for a long period of mechanical loads. Over time, this reduces maintenance costs significantly.
- Pressure Rating (PN): These pipes cater to a wide range of pressure ratings, exceeding 16 bars which supports their usage in highly complex interconnecting networks.
- Thermal Stability: They perform exceptionally well and can withstand sustained temperatures of – 40°F to 140F which makes them useful in various regions.
- Chemical Resistance: Due to their construction material being inert, they are impermeable to most aggressive chemicals which guarantees safety in drinking water and harsh industrial situations.
- Lifetime Expectancy: Depending on the application, HPDE pipes can be as useful as 50 to 100 years which gives an unparalleled long-term value.
Therefore, advanced technical specifications and the strength these pipes have while facing critical infrastructure lead to higher costs, which is a positive aspect as it ensures operational efficiency and less life cycle costs. To conclude, purchasing HDPE pipes leads to the guarantee of superior functionality and reliability which far surpass the initial investments made.
What Should I Budget for a Complete HDPE Pipe Project?
Calculating Material Costs for Various Project Applications
While calculating the material costs for an HDPE Pipe Project, I ensure that I analyze the following major factors for the estimate to be adequately justified and accurate:
- Pipe Dimensions and Specifications: The diameter, wall thickness, and pressure rating such as SDR and PN value profoundly affect the price. Bigger diameters and higher-rated pressure bring about higher costs due to more material being needed during manufacturing.
- Application Type: The type of use, whether for distribution of water, sewage systems, industrial processes, or gas transfer will determine the specific grade of HDPE material that is needed. For instance, gas and high-pressure applications are better serviced by PE4710 resins due to greater strength and creep resistance.
- Project Scope and Length: The longer the pipeline, the more materials are needed, so the total linear footage of the pipeline affects the capacity to a large extent. Also, one must take into account any additional reserves that might be required for future repairs or replacement of more expensive materials.
- Accessories and Fittings: Materials costs are increased by necessary accessories such as bends and caps, tees, end coupling, and even wedges. This is a must for any fitting if the integrity of the system is to be maintained for the pipe itself, material grade and specifications must be matched.
- Transport and Logistics: For large bore projects, the movement to the site tends to take up a large proportion of the f budget so reducing transportation costs is a goal. Compared to traditional materials, the lightweight nature of HDPE is advantageous as it helps with reducing transportation costs.
By assessing these features, I can develop a comprehensive and accurate cost estimate for a particular project’s scope.
Additional Expenses: Fittings, Services, and Installation
- Fittings and Components: The fittings on the pipes such as elbows, reducers, tees, flanges, and coupling systems seams to my fittings budget are eligible due to the scope of the project. They are all required for proper system function and compatibility. For example, two material combinations (i.e., HDPE with electrofusion or butt fusion fittings) as well as pressure ratings (SDR 11 for high-pressure systems) need to be compatible with the requirements of operational usage of the pipeline.
- Specialized Services: Critical services such as fusion welding or joint testing also need to be considered. As an example, electrofusion welding is vectors an integration of different processes and requires a lot of temperature and angular control in addition there is a lot of labor to create and apply the required control.
- Installation Considerations: Different locations have different problems which has a direct impact on the cost of installation. This could be the case with trenching where the methodology with variations depends on the type of soil, depth, and safety requirements. Some standards need to be adhered to, such as ASTM D2321 for the installation of HDPE pipes. These preassumptions lead to accurate cost calculation in the end ensuring the structure is stable and compliant.
These factors allow me to explain in a thorough yet precise manner the additional expenses and justify them within the limits of the project scope and standards.
Cost-Saving Tips for HDPE Pipe Projects
- Optimize Material Usage: The right material choice and proper estimation of material quantities needed, especially for pipe lengths, can mitigate waste considerably. Use sophisticated measurement software to cut as little as possible to maximize benefits and eliminate scraps. In addition, select pipe grades that can achieve the project specifications without going overboard to optimize cost versus performance.
- Efficient Jointing Techniques: Select jointing techniques that blend both economical and strong options. For example, in large projects, butt fusion welding is frequently cheaper than electrofusion due to the lack of required couplings. Make sure to stick to constraints such as temperature, which is usually between 400 and 450 degrees Fahrenheit for HDPE fusion, as well as alignment accuracy, or else face the risk of joint failures and rework costs.
- Evaluate Site Conditions Early: Perform soil and site inspections in order to forecast challenges and take care of them accordingly.
- Plan for Logistics and Storage: Transport and handling costs are minimized by synchronizing pipe deliveries with the construction schedule to cut down on onsite storage time. Fresh-cut pipes should be covered or stored away from UV light, as prolonged use can lead to excess UV exposure which may damage the pipes.
- Standards and Best Practices: Following guidelines like ASTM D2321 for installation and ASTM F2620 for heat fusion procedure guarantees performance, which in turn, minimizes rework and maintenance costs. This compliance also lowers project risks and guarantees stability and cost savings during the lifecycle of the installation.
Using these methods along with the recommended procedures enhances economical efficiency without compromising the standards and even rules of the HDPE pipe projects.
Reference sources
Frequently Asked Questions (FAQs)
Q: What factors influence HDPE pipe price lists from different suppliers?
A: Several factors affect HDPE pipe price lists from various suppliers. The primary factors include pipe diameter (with 8″, 18″, 20″, and 24″ being common sizes), wall thickness, length requirements, pressure rating, and the grade of high-density polyethylene used. Additionally, supply chain conditions, raw material costs, bulk purchase discounts, and shipping distances all contribute to price variations. When comparing suppliers, request a complete price list that includes these specifications to ensure you’re making accurate comparisons.
Q: How much does HDPE pipe typically cost per foot or length?
A: HDPE pipe costs vary significantly by diameter and pressure rating. As a general guide, smaller diameter pipes (around 8″) typically range from $5-15 per foot, while larger diameter pipes (20″ and above) can cost $50-200 per foot. Standard length options are typically 20, 40, or 50 feet, with some suppliers offering custom lengths. For the most accurate pricing, request a current HDPE pipe price list from your local supplier, as prices fluctuate based on material costs and market conditions.
Q: What should I consider when selecting an HDPE pipe for my project?
A: When selecting HDPE pipe, consider several critical factors: application requirements (pressure, temperature, chemical exposure), proper sizing (common diameters include 8″, 18″, 20″, and 24″), pressure rating (SDR or DR rating), wall thickness (solid wall or profile wall), connection methods, and local code compliance. High-density polyethylene pipes come in various grades (PE4710, PE3608, etc.) suited for different applications. Also factor in installation conditions, UV exposure, and long-term maintenance needs. Consulting with an experienced engineer or contractor can help ensure you select the appropriate product for your specific application.
Q: How can I create an account with HDPE pipe suppliers to access wholesale pricing?
A: To create an account with HDPE pipe suppliers for wholesale pricing, first research reputable suppliers with solid industry reputations and sufficient stock levels. Contact their sales department via phone or through their website to inquire about establishing a business account. Be prepared to provide business credentials including tax ID, business license, and possibly trade references. Many suppliers require minimum purchase amounts to qualify for wholesale pricing. Once your account is approved, you’ll typically gain access to complete price lists, special promotions, and potentially dedicated account representatives for your high-density polyethylene pipe needs.
Q: What installation factors affect the total cost of an HDPE pipe project?
A: Installation factors significantly impact the total cost of an HDPE pipe project beyond the basic product price. These include trenching and excavation requirements, soil conditions, depth specifications, backfill materials, fusion equipment rental or purchase, skilled labor costs for proper fusion/joining, and landscape restoration. Additional cost factors include permits, inspections, traffic control in public areas, dewatering if necessary, and accessibility challenges. Projects requiring 20″ or larger diameter pipes typically have higher installation costs due to heavier equipment needs.
Q: Are there different grades of HDPE pipe and how do they affect price?
A: Yes, different grades of high-density polyethylene pipe significantly impact pricing. Common PE grades include PE4710, PE3608, and PE2708, with PE4710 being the premium grade offering excellent pressure ratings and longevity. Higher grades cost more but provide better long-term performance. Additionally, specialized formulations with enhanced properties like chemical resistance, UV protection, or antimicrobial additives command premium prices. The diameter (8″, 18″, 20″, 24″, etc.) and wall thickness (solid wall vs. corrugated) also affect pricing. When comparing HDPE pipe price lists, ensure you’re evaluating equivalent grades to make informed purchasing decisions.