When it comes to selecting the right piping solution, high-density polyethylene (HDPE) pipes often emerge as the material of choice, thanks to their durability, flexibility, and cost-effectiveness. However, navigating the complex range of sizes, dimensions, and specifications can be a daunting task without the right resources. Whether you’re a contractor, engineer, or industry professional, having accurate and concise information on HDPE pipe sizes is critical for ensuring efficiency and precision in your project. This guide provides a detailed overview, equipping you with the essential knowledge you need to make informed decisions. Explore the intricacies of HDPE pipe dimensions and discover why understanding these specifics is crucial for successful applications.
What is an HDPE Pipe and Why is its Size Important?
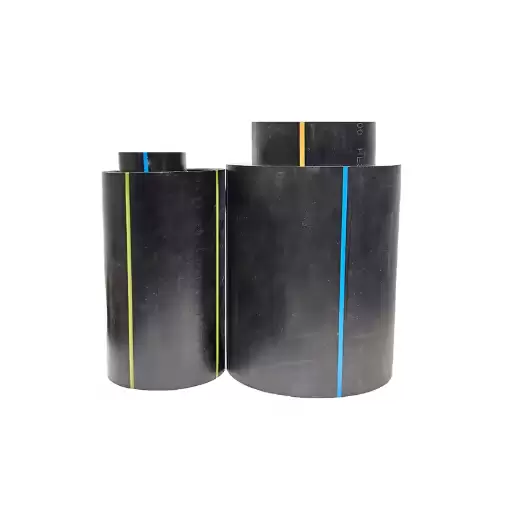
Understanding HDPE Pipe Characteristics
The versatility of HDPE (High-Density Polyethylene) pipes can be attributed to its superior strength-to-density ratio, flexibility, and corrosion-resistance. The material provides endurance for most applications, including industrial pipelines, water supply, gas distribution, and sewage systems. The high-density polyethylene material offers durability and chemically resistant properties which are essential during operation.
The size of an HDPE pipe influences its application and functionality. Its diameter and wall thickness determine the flow capacity and its pressure rating, while SDR (standard dimension ratios) ensures compatibility and uniformity in manufacturing. Properly sized piping assists in achieving maximum system performance by avoiding pressure drops or capacity concerns in high- and low-pressure systems.
Employing proper dimensions not only improves operational efficiency but also reduces resource expenditure and the chances of system failure. Having dimensional accuracy provides professionals the advantage to systematically and methodically achieve their technical goals and project objectives.
Why Pipe Size Matters in Projects
To determine appropriate pipe sizes for a certain project, it is significant to analyze many factors that affect the performance and the operational risks that may result. The flow rate requirement is one of the most critical to consider, and its value must always be high. The pipe needs to allow for proper flow to prevent loss of pressure and other inefficiencies, such as restrictions. Plumbing System velocity also needs to be carefully calculated to avoid all forms of turbulence and erosion, which leads to the breakdown of the pipes.
Another key factor to consider is the piping material and its composition. This type of fluid also needs to be accurate because different materials can endure temperature, pressure, and chemical substances to different degrees. Compatibility ensures the structural integrity of the pipeline over an extended period, therefore reducing maintenance works and unnecessary costs.
Modern engineering offers endless possibilities as far as computational tools and simulation modeling is concerned, allowing for ideal pipe dimensions across various disciplines. These level tools works with multifaceted issue such as temperature gradients, peak load condition, energy efficiency, etc.
Common Applications of Different Pipe Sizes
Choosing the correct pipe size is pivotal in determining system effectiveness in different industries. The following are some examples under their respective uses of pipe measurements.
- Small-Diameter Pipes (Usually pipes less than 2 inches): Used in residential buildings for plumbing, water supply, and distribution, given their capacity to deal with moderate flow rates. Further, other industries that need accurate fluid control, like chemical injection systems and instrumentation tubing, also utilize these pipes.
- Medium-Diameter Pipes (2 to 12 inches): Particularly common in industrial and commercial use such as HVAC, fire suppression systems, and waters of moderate scale distribution. Their size allows to strike the balance between space and the need to accommodate higher flow volumes.
- Large-Diameter Pipes (more than 12 inches): Common Use in water mains, sewer systems, and storm drain networks, both in municipal and industrial infrastructure. Most importantly, they can be used as conduits for transporting vast volumes of industrial fluids, which are critical for oil and gas pipelines.
The newest developments in pipe design include new materials and HDPE, RTP, and composite pipes, which have broadened the scope of applications. CFD modeling makes certain that pipe dimensions correspond with pressure and flow parameters for different operating conditions, optimally improving project safety and efficiency.
How to Read a Polyethylene Pipe Size Chart?
Key Metrics: Diameter, ID, and OD
Pipe Size (Nominal Diameter) |
Inside Diameter (ID) |
Outside Diameter (OD) |
---|---|---|
1 inch |
Approximately 0.86 inches |
Exactly 1.315 inches |
2 inches |
Approximately 1.74 inches |
Exactly 2.375 inches |
4 inches |
Approximately 3.83 inches |
Exactly 4.5 inches |
6 inches |
Approximately 5.74 inches |
Exactly 6.625 inches |
8 inches |
Approximately 7.92 inches |
Exactly 8.625 inches |
10 inches |
Approximately 9.95 inches |
Exactly 10.75 inches |
12 inches |
Approximately 11.94 inches |
Exactly 12.75 inches |
The table above contains the important measurements concerning HDPE pipes, which are central to understanding their usefulness for particular industrial and operational needs.
Interpreting Pressure Ratings and SDR
The interrelationship between Pressure ratings and SDR (Standard Dimension Ratio) sets the boundaries within which HDPE pipes are reliable and functional under certain operating conditions. SDR is a function of the pipe’s diameter and wall thickness; it is determined by the outer diameter of a pipe divided by its wall thickness. A lower SDR suggests a thicker wall, which in turn suggests a higher pressure rating the pipe can withstand internally.
As an example, an HDPE pipe with SDR 11 can typically handle a working pressure of around 160 psi, while an SDR 17 pipe can only sustain a working pressure of around 100 psi under the same conditions. These pressure ratings take into consideration the material’s long-term hydrostatic strength, making allowances for factors like temperature and time period for which pressure is being applied.
It is important to think about the application, the working environment, and the transported medium when choosing SDR and pressure rating for an HDPE pipe. Failing to do so could result in underperformance or inefficient operations. Standards like ASTM D3035 and ISO 4427 give instructions on designing and testing HDPE pipes to maintain reliability and functionality in different use environments.
What are the Standard HDPE Pipe Sizes Available?
Range of Pipe Sizes in the Market
Industries differ in size and so does the equipment that serves them. Infrastructure requires dimensions big while commercial enterprises like shops or even single stores can get away with low infrastructure demands. Commercial activities have peripheral HDPE pipes catering to businesses peers or even multiunit residential buildings. These businesses can use as simple as 0.5 inches to complex systems of over 2 miles of pipes.
Comparable to most pipe systems, HDPE pipes are divided into different categories based on denomination, serial, and other common attributes. In every denomination, they feature unique internal diameters. Based on the region, people use different-sized pipes, construction projects, or cold waters demanding 20 mm, while hot systems using iron may require 315 mm. Furthermore, standard pipe lengths are available featuring two inclined options. For diameters under 110 mm, pipes are coiled, while rigid supine fully extendable pipes promising utmost usability, come in increments of 6 or 12 meters with suggested customization for added incentive.
To guarantee that HDPE pipes satisfy various requirements, they are manufactured in accordance. Additionally, companies may offer custom-sized components and fittings, further illustrating that HDPE piping systems are not only useful in many ways, but are also useful in meeting a myriad of operational requirements.
Commonly Used Sizes and Their Applications
HDPE pipes help industry sectors like water, gas, sewage, and even industrial sectors to do their work hassle-free. Different sizes of HDPE pipes help ease up these different industries and sectors. Some of the ranges that are most commonly used include:
- Diameter Range of 16mm to 75mm: Household drip irrigation systems, commutable water lines for households, and minor scale agricultural activities all have one thing in common, they use these smaller range-sized pipes. These pipes are easy to install as they are light in weight and flexible, allowing for decreased interference in tight areas.
- Diameter Range of 90mm to 250mm: Broadly utilized HDPE pipes can be found in drainage systems, industrial processes and even sewage networks, all of which use medium sized pipes. These sizes combine strength and versatility enabling them to be used in a moderately high flow systems, where sytem durability is highly stressed.
- Diameter Range of 315mm to 630mm: Most commonly used for municipal water distribution systems for dealing with household water supply and even large-scale agricultural irrigation, pipes of this diameter range stormwater drainage networks can handle high and wide flow volumes along with long distances.
- Diameter Range of Above 710mm: Useful for ongoing high intensity work sites like bulk water transmission, industrial waste management and gravity based sewer systems all utilize this size of Horizontal Directional Drilling. Being large in diameter, these pipes cope up with extreme internal and external pressures ensuring safe and durable under extreme functioning conditions.
Choosing the appropriate pipe diameters is connected to the flow rate, pressure settings, and the environment. Design and planning needs accuracy for targeting the best performance versus costs, since all of these factors need to be accounted for. HDPE pipe systems, as an example, are easily adaptable to many industries because of their precise configurations, proving how adjustable and functional these systems are.
Understanding Nominal and Actual Sizes
Nominal pipe size (NPS) is a term used to describe the diameter of a pipe and is mostly used for easy identification or classification, but it does not reflect the actual size of the pipe. Unlike the actual pipe sizes, which considers the internal diameter (ID) and external diameter (OD) as a function of wall thickness, material grade and thickness of the pipe, NPS is a reference size and does not reflect an actual measurement.
For example, when looking at the actual measurements of High-Density Polyethylene (HDPE) pipes, one can notice that their nominal sizes deviate significantly due to wall thicknesses related to Standard Dimension Ratio (SDR) classifications. For example, a nominal pipe size of 2 inches has an internal diameter and external diameter translating to an SDR value, hence accurate measurements and calculations need to be done during the design and installations of the system.
Using accurate descriptions avoids issues of pipeline problems in places like water supply systems, to industrial fluid transport applications, which correlate to business level operational failures. Understanding these discrepancies is central to effective planning and engineering of pipelines that aid in mitigating risks of system flow capacity and pressure failure.
How Does HDPE Pipe Size Compare to Other Materials?
Differences Between HDPE and Ductile Iron Pipe Sizes
Aspect |
HDPE Pipe |
Ductile Iron Pipe |
---|---|---|
Material Flexibility |
Highly flexible |
Rigid |
Size Range |
Wider diameter options |
Limited standard sizes |
Weight |
Lightweight |
Heavier |
Pressure Rating |
Lower pressure rating |
Higher pressure rating |
Joint Configuration |
Fusion or mechanical joints |
Mechanical, flanged, or push-on |
Inner Diameter Consistency |
Slightly reduced due to thicker walls |
More consistent |
Corrosion Resistance |
Excellent, non-corrosive |
Prone to corrosion without lining |
Installation Ease |
Easier to handle and install |
Requires heavy machinery |
Longevity |
Long lifespan with less maintenance |
Durable but requires maintenance |
Comparing HDPE with PVC Pipe Dimensions
While assessing piping systems, two common options are HDPE (High-Density Polyethylene) and PVC (Polyvinyl Chloride). Each offers different dimensions and performance attributes suited to different applications. For example, the thicker walled HDPE pipes are built to sustain greater internal pressure ratings, making them preferable for high-pressure water mains and gas distribution systems. Conversely, thinner walled PVC pipes for the same nominal diameter allow for greater inner diameter and enhanced flow capacity in low-pressure systems.
The flexibility of HDPE pipes proves useful in seismic or uneven terrains as they can shift with the ground without rupture. PVC pipes, though stiffer, are better suited for projects requiring strong alignment. Meanwhile, HDPE pipes use SDR (Standard Dimension Ratio) classifications, which state wall thickness proportional to outer diameter, with lower SDR values indicating higher pressure capacity.
From an installation point of view, HDPE pipes have the advantage of low weight and can be provided in long rolls or coils to reduce jointing needs, which is especially beneficial for trenchless installations. This significantly lowers potential leak risks. Short, rigid PVC pipes rely on either mechanical or solvent-welded joints that maintain alignment accuracy but take more effort to install. In general, HDPE and PVC offer unique advantages and disadvantages. Factors such as pressure, operating environment, and installation limitations define which materials are most suitable for the project’s demands.
Advantages of Using HDPE Pipes
The applications of High-Density Polyethylene (HDPE) pipes span several industries, including water distribution, gas pipelines, and wastewater systems. This is unleashed through their advanced durability compared to other materials, which is one of the greatest advantages of using the material. Because of the way HDPE pipes are designed, they are strong candidates for use in tough environments, including coastal or industrial areas, due to their ability to endure corrosion and the breakdown of chemicals.
Under aggressive mechanical loads such as soil displacement and seismic forces, HDPE pipes demonstrate a remarkable level of flexibility alongside tensile strength, making them even more durable. They help ensure no damage occurs while adapting to external forces, which make the pipes suitable for installation in earthquake prone areas. Furthermore, due to the lower modulus of elasticity, the pipes can withstand more pressure while enhancing the overall lifespan of the material.
Another critical advantage is the lightweight compared to materials like concrete or ductile iron. The lighter weight makes transportation, handling, and installation easier, saving time and money. Also, HDPE pipes use modern joining methods like butt fusion and electrofusion which create reliable, leak-proof joints. These welds create a monolithic pipeline devoid of weak points, which is crucial for high-pressure applications or critical infrastructure.
The material’s smooth internal surface lowers friction losses which improves flow efficiency thus lowering energy costs when pumping. Coupled with HDPE’s resistance to biofouling and scaling, this HDPE feature ensures maintenance is minimal throughout the lifespan of the pipeline. Finally, HDPE’s recyclability makes it environmentally friendly, aligning with modern sustainability practices while reducing impact.
When choosing pipes for any infrastructure project, the optimal overall performance of HDPE pipes makes them a favorable answer, given that the system design and operational conditions align with their capabilities.
What Factors Affect the HDPE Pipe Size You Choose?
Project Specifications and Requirements
A lot of technical operational elements need to be evaluated when selecting an appropriate HDPE Pipe size for a project. Getting the correct specification requires consideration of what type of fluid is to be transported, the temperatures involved, and what pressure rating is needed for smooth and operational processes. For example, the pipe’s diameter and wall thickness need to be adequate for the applicable pressure classes, considering material density, and also considering the stress loads expected in the system. Assessments made concerning flow rate and velocity need to be accurate since they are key determinants in the proper operation of a system in traversing a pipeline with minimal pressure drop and turbulence.
A lot of factors need to be put in perspective as well, like environmental conditions. For projects that are subject to extreme temperature, chemical exposure, and UV radiation, the pipes resistance against such factors need to be validated.
Using advanced simulation tools alongside technical standards gives the ideal integration of HDPE pipes into various infrastructural project systems after meeting those specifications.
Environmental Considerations and Constraints
It is very important to consider all factors that may affect the performance of HDPE pipes when looking at different environments. In particular, long-term influences such as temperature, chemicals, soil make-up, UV exposure, and others require careful evaluation. Because HDPE pipes are resistant to a wide array of chemicals, including those present in agriculture, chemical transport systems, and wastewater management, they are an industry favorite.
Materials of construction, such as HDPE pipes, are often subjected to extremes in temperature, which threatens to test the upper extremes of what these materials can withstand, straining their weakness. Although HDPE pipes have high flexural rigidity and thermal resistance, constant exposure to low temperatures or extremely hot temperatures can impact them mechanically. This impact comes in the form of tensile strength, elasticity, and stress cracking, especially under thermal cycling set through ASTM-compliant testing.
Above ground installation of pipes subject them to UV radiation, and combined with supremely high temperatures pose a challenge in terms of dirt removal and maintenance. Therefore, above ground HDPE pipes require constant long-term surveillance in order to ascertain their structural integrity and mechanical stability over decades of heavy duty service.
Also, the interaction of HDPE materials with different types of soils should be taken into account. Soils that are very acidic or very alkaline may worsen any chemical reaction, which means a thorough geotechnical study must be conducted before installation. Using environmental datasets from specific industries alongside local evaluations enhances the strategic planning for the installation of HDPE pipes, therefore improving the durability and lifecycle of infrastructure systems.
Budget and Cost Implications
It is important to evaluate both the short-term expenditures and long-term benefits of using HDPE piping systems when considering the budget and installation costs associated with HDPE pipes. The costs associated with an HDPE pipe contribute to its material costs, labor, and preparatory work on the site. Moreover, the pipe’s diameter, wall thickness, and length require additional components, which will also affect the overall cost. Furthermore, these specialized methods pose their costs in terms of machinery or procedures needed for installation, such as in environmental or soil-specific conditions.
From a cyclical viewpoint, the weatherproofing, lack of maintenance needed, and rust-resistant features contribute to why HDPE pipes are ultra-durable, further proving their use advantageous in the long run. Expenses associated with operations for systems made out of HDPE are significantly lower due to reduced risks of contamination, leakage, structural failure, or damage over time. These costing methods enhance accuracy, which assists project stakeholders when making decisions regarding resource allocation through advanced modeling and forecast cost algorithms powered by predictive tools.
In sustainability perspectives, using recycled HDPE aids in achieving these movements without purposefully raising the cost of the project, which in turn will lower the overall cost of it according to the latest trends within the industry. Moreover, mechanical and environmental standards must be upheld along with preserving performance so that the structural integrity of the recycled material will be controlled beyond value. Balancing a cost-efficient solution while considering these factors showcases the steps needed to align sufficiency with performance and environmentally friendly responsiveness.
References
Frequently Asked Questions (FAQ)
Q: What is an HDPE pipe size chart?
A: An HDPE pipe size chart is a reference tool that provides detailed information on the dimensions, including diameter and wall thickness, of high-density polyethylene (HDPE) pipes. It typically includes specifications such as IPS, PE4710, and minimum wall thickness.
Q: How do I read an HDPE pipe size chart for line stopping?
A: To read an HDPE pipe size chart for line stopping, locate the relevant diameter that matches your pipeline’s needs, ensuring compatibility with line stopping equipment. The chart will indicate the minimum wall thickness required for safe and effective line-stopping operations.
Q: Why is it important to consider the minimum wall thickness in HDPE pipes?
A: The minimum wall thickness is crucial in HDPE pipes to ensure structural integrity and pressure resistance. It affects the pipe’s ability to withstand external forces and internal pressures, especially in bypass and block applications.
Q: What does PE4710 mean on an HDPE pipe size chart?
A: PE4710 is a designation for a specific type of HDPE material that offers higher performance, including greater pressure resistance and durability. It is often noted on HDPE pipe size charts to indicate the product’s suitability for demanding applications.
Q: How do I choose the right HDPE pipe size for a bypass application?
A: For a bypass application, refer to the HDPE pipe size chart to select a pipe with the appropriate diameter and wall thickness. Ensure it meets the required flow capacity and pressure specifications while considering the average flow rate needed for the bypass.
Q: Can HDPE pipes be used for large-scale projects?
A: Yes, HDPE pipes are suitable for large-scale projects due to their durability, flexibility, and availability in larger diameters. They are often used in municipal, industrial, and agricultural applications.
Q: What role does an IPS specification play in HDPE pipes?
A: The IPS (Iron Pipe Size) specification in HDPE pipes refers to the sizing standard used for pipe dimensions. It ensures compatibility with other piping systems and fittings that adhere to the same standard.
Q: What are the benefits of using high-density polyethylene pipes?
A: High-density polyethylene pipes offer several benefits, including corrosion resistance, flexibility, long lifespan, and low maintenance. These properties make them ideal for a variety of applications, including block and line stopping operations.
Q: How do pipe dimensions vary in HDPE pipe size charts?
A: Pipe dimensions in HDPE pipe size charts vary based on the intended application, material specifications, and manufacturer. Charts typically provide a range of diameters and wall thicknesses to accommodate different installation and usage requirements.