High-density polyethylene (HDPE) pipes are becoming popular in different industries because they offer durability and flexibility and are cost-effective. Knowledge of HDPE pipe specifications and dimensions is equally necessary for engineers, builders, and hobbyists as it will dictate the design and implementation of any given project. This article seeks to give the intended audience a clearer insight into the different sizes of HDPE pipes, together with their relevant size charts and a guide for conversion. Furthermore, since these features will be examined, the guide will ensure that HDPE piping is used properly for all projects, including irrigation systems and various industrial undertakings. If you are new to HDPE, or looking for a reliable guide, this guide is one of the best resources that will help you understand the different dimensions of HDPE pipes.
What Are the Standard HDPE Pipe Sizes Available?
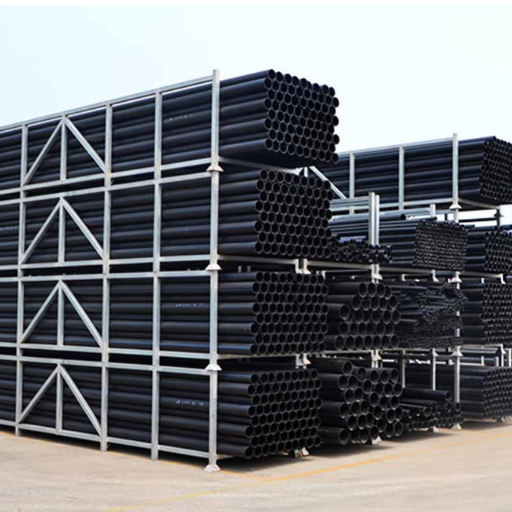
To cater to the needs of various industries, HDPE pipes come in some of the standard sizes, such as 0.5 inches to 63 inches in diameter. There are certain standards, for example, ASTM D3035 and ISO 4427, that they have to conform to. Primarily, the pipes are classified on the basis of the outside diameter, which is otherwise known as OD. HDPE pipes, however, can be made with different wall thicknesses since there are many pressure ratings available. Due to this variability in the design sizes, HDPE pipes are versatile in application and range from residential water lines to huge industrial pipelines.
Understanding the Diameter of HDPE Pipes
Awareness of the diameter of HDPE pipes aids in the competent utilization of this multifaceted material. In different projects that I have participated in, understanding the diameter of an HDPE pipe correctly is one of the most important aspects to focus on while choosing the right pipe for the job. You can measure the HDPE pipes in terms of Diameter outside (OD) or Nominal Pipe Size (NPS), or there are other reasonably-sized parameters depending on what the application of the pipe is intended to be. For example, there is a possible sense that only a small pipe diameter will be needed in a waterline serving a home in order to ensure that water will be moving without wasting too much material. Other Applications in highly developed industrial environments can, however, call for bigger diameters so as to increase the flow rate and/or handle heavier loads. I guarantee myself that by understanding the diameter crucial requirements and standards, all projects involving HDPE piping will be undertaken in the most cost-effective and efficient manner.
What is the Standard HDPE Pipe Size Chart?
The HDPE pipe size chart is quite common as it usually provides structural details of the pipes, with particular emphasis on the pipes’ outside diameter (OD) and nominal pipe size (NPS). The most common dimensions and features included in this information may be summarized as follows:
- Outside Diameter (OD): In essence, understanding the HDPE pipe size chart is about knowing your application’s needs and matching them to the OD, NPS, SDR, and pressure ratings for efficiency and reliability in your projects. This clarity ensures you select the right pipe for the job, optimizing both performance and cost.
- Nominal Pipe Size (NPS): Used more on a standing basis, NPS is often interchanged with OD but instead provides a rough idea of size in more standard length ranges. But it is not always the full measure, so it is always advisable to first see the OD as well.
- SDR (Standard Dimension Ratio): This is the ratio between the outer diameter and the wall thickness of the pipe. A low SDR means a thicker wall, and a high-pressure rating means A high SDR means a thinner wall. Example, SDR11 will have thicker SDR than SDR17.
- Pressure Rating: This measurement also uses pounds per square inch, psi and indicates the highest enumerated pressure that the pipe can safely sustain. It is of particular significance for cases where the pipe is going to transport pressurized liquids.
Essentially, interpreting the HDPE pipe size chart is understanding the requirements of your or project and, the OD, NPS, SDR, and pressure ratings which will meet the requirements efficiently and reliably at your projects. This clarity makes sure that you install the correct pipe for the appropriate project making sure performance and cost are optimal.
Common HDPE Pipe Sizes and Dimensions
From the tutorial about HDPE pipes, their standard dimensions, and characteristics, I understand that there exists some order when it comes to the division of these pipes. The different sizes are systematically organized and presented, which includes many dimensions that are important for various uses, as indicated in charts or tables. For example, a single, or rather, an NPS, can be located in a table next to its appropriate OD value, which is actually in inches and even in millimeters. The same measurement is very important so as to allow usage in different countries. There is more information provided about the SDR of the pipe which explains how the outer diameter and wall thickness of the pipe influence its pressure rating.
As for practical physical characteristics, it is evident that NPS is four while OD is often approximately 114.3mm, about 4.5 inches. Depending on the SDR, its pressure rating can vary significantly. For instance, with an NPS of approximately 3 inches, an SDR11 pipe would bear approximately 200 psi, while an SDR17 pipe would have a pressure rating of about 125 psi. At the same time, this information enables me to select the exact pipe that is appropriate for my task and does not exceed the pressure limit for that particular workload, completing it with satisfaction and reliability.
How do you select the right HDPE pipe size for your application?
Choosing the right size for your HDPE pipe requires that a few fundamental bases be covered. To begin with, make sure to analyze the specific requirements of the installation such as desired pressure, flow rates, and the site conditions. Be sure to check the NPS and OD so that they will not conflict with other systems. Determine the SDR in order to be able to check the An error occurred during generation. Please try again or contact support if it continues.
Factors to Consider When Selecting the Right Pipe Size
not all design engineers comprehend the importance of this, let alone engage in the selection of a suitable pipe size for each specific project. First, I try to understand the requirements, such as the pressure ranges and flow requirements for a particular pipe; this indicates the broad parameters for the initial sizings. I then consider the environment in which the pipe will be located; temperature and potentially chemicals will affect the viability of the material’s longevity. Genetic compatibility is also of special importance. In this context, if the Pipe’s or Nominal Pipe Size (NPS) and Outside Diameter (OD) are properly positioned relative to one another, then there will be no complications in the installations of these systems. Moreover, in order to determine the pressure rating of a pipe, it is also necessary to know its Standard Dimension Ratio (SDR), a clear indication of the wall thickness of the pipe in question. In this case, the applicability of the material to certain conditions is greatly reduced. From the research of these factors, I have the confidence to state that I knew which HDPE pipe would work for this task the best ensuring durability and efficiency in that specific application.
Applications of Polyethylene Pipes in Different Industries
The pex-plumbing. Connections with diverged sectors internal/external are quite captivating and very important, as such expertise is very crucial, especially in the sheet metal industry. I’d be happy to explain the specifics of some of these areas.
- Water Supply Systems: It is typical to choose polyethylene pipes with respect to their ductile characteristics and resistance to corrosion. They are manufactured to withstand a variety of pressure requirements and flow rates while ensuring longevity and low leakage.
- Gas Distribution: Polyethylene pipes are widely used for manufacturing gas pipelines because of their strength and thermal stability as well as their chemical resistance which is fundamental to transporting gas safely.
- Sewage and Industrial Waste: Polyethylene pipes are suited to offer these applications as they can tolerate extreme conditions. They are resistant to a variety of chemicals and leaks or ruptures are minimised.
- Irrigation Systems: The agriculture sector is heavily dependent on effective water supply systems, and polyethylene pipes are appropriate for this application. They are quick and easy to install, are highly adaptable to various terrain features, and are weather resistant which ensures the crops receive adequate supply of water.
- Mining and Oil Pipelines: These industries require piping systems that can withstand high operating pressure, and coal or metal dust. polyethylene’s strength and toughness are suitable for such extreme working conditions typically found in the mining and oil extracting industries.
Knowing this information about the applications and their requirements, I make sure that polyethylene pipes are used correctly in a number of sectors and thus they are able to provide dependable and efficient services.
Understanding Pressure Ratings for HDPE Pipes
Understanding pressure rating is one of the most important points when selecting HDPE (High-density polyethylene) pipes for various applications. Here are the cardinal parameters and their meanings:
- Nominal Pressure Rating (PN): This refers to the level of pressure that the pipe can withstand before rupturing. It is measured in pressure bars or pounds per square inch and assists in finding whether a pipe is fit for high or low-pressure fittings.
- Wall Thickness:The Pressure Rating of a pipe is dictated by wall thickness. More pressure is applicable to thicker walls, and less pressure is suited to applications with thinner walls.
- Pipe Diameter: As the diameter of the pipes goes larger, the pressure rating also tends to reduce, because the pressure applied on the pipe walls is being spread along a larger area. On the other hand, smaller diameters undergo higher pressure without yielding as easily.
- Temperature Rating: The pressure ratings of the pipes tend to vary due to temperature variations, in this case, an increase in temperature would bring about decreased tolerances with regards to pressure of the pipe; therefore, temperatures should be taken into account when looking at pressure ratings as well.
- Standard Dimension Ratio (SDR): It is the ratio obtained from the distance of the outer edge of a pipe to the thickness of a wall of the pipe. For instance in the case of pipes with low SDR, they have thick walls, and have high pressure rating, making it an important component when determining the type of pipe suitable for you.
Considering these pressure-related parameters makes you choosing the most suitable HDPE pipes safer and more efficient for your application.
What is the Chart Conversion for HDPE Pipe Sizes?
The Chart Conversion for HDPE pipe sizes establishes a logical procedure for determining the outside diameter of the pipes of given nominal sizes. More simply, it defines the outdoor diameter, wall thickness, or even SDR or the cross-section area of a pipe that has been assigned a size that is expressed in inches or millimeters. This chart is of utmost significance to the practitioners in the industry to select the right HDPE pipes against some given requirements and validate compatibility with the neighboring pipelines. Knowing these conversions tends to simplify the installation procedure and assures the functioning of the selected pipes as desired in the prevailing conditions.
How to Read and Use the Size Chart Effectively?
As I practice, I begin by determining which nominal dimension of the HDPE pipe that I am using which is normally indicated in either inches or millimeters. The next step involves using the dimensional cross reference” which enables me to ascertain the actual outside diameter as well as the wall thickness of the pipe in question. SDR value is also important to mention since it gives an indication of the wall thickness to diameter ratio. This will help me to be sure that the pipe chosen for the purpose will meet the pressure as well as the environmental aspects of the project. Also, it is helpful to know the conversion chart in order to check whether the new pipes match with already present systems so that expensive errors do not occur during the positioning of the new pipes. In this way, this systematic practice helps to make sure that the selected pipes will withstand the operating parameters as per defined conditions.
Conversion from MM to Inches: A Simple Guide
Add in the fact that converting metric measurements (MM) to imperial (Inches) is an effortless but vital skill to have, and this problem becomes a piece of cake. Allow me to elaborate on this with an easy take and a more functional one.
- Understanding the Conversion Factor: When changing from millimeters to inches, the conversion factor must be used, where 1 inch is equal to 25.4 millimeters. In this case, the conversion factor is fundamental since it allows for correct computations.
- Performing the Conversion: The millimeter value is divided by 25.4 to express it in inches. In practical terms, if a pipe has a diameter of 100 millimeters, then 100 millimeters divided by 25.4 millimeters per inch equals approximately 3.937 inches. This accuracy ensures that HDPE pipes are installed with respect to the previously existing structures which were measured in inches.
- Tools and Verification: There are also conversion tools that can be used as a calculator, which is also useful, especially in getting correct measurements. These tools can economize time and effort especially with respect to errors during the conversions within the range of a single project.
- Check for Consistency: You will then proceed to recheck your work in an effort to makes sure that your conversions are accurate and consistent. This step is important because a simple mistake may result in a problem where elements and or installations are non compatible.
Consequently, by accomplishing the processes outlined above, you can be sure that you will change MM to inches and that your selection and installation of the HDPE pipes will be precise as well as effective. This method is helpful in ensuring that the pipes work effectively under the predicted service conditions.
Understanding the SDR and Its Importance
I often get asked about the importance of Standard Dimension Ratio (SDR) when dealing with HDPE pipes. Knowing about SDR is important because it informs you of the anticipated pressure rating, endurance, and effectiveness of the pipe. So here is what I mean:
- What is SDR?: The term Standard Dimension Ratio is denoted as SDR, and this is also a measure of the strength of HDPE pipes, being the metal a ratio value that determines the width of the pipe wall as the fixed ratio of the diameter. It’s a pillar on which the outer diameter of a pipe rests plus the width of the wall- the ratio of the two. A lower SDR specifies a pipe which has a thicker wall, on the other hand, a pipe which has a higher SDR has thinner walls.
- Importance of SDR:
- Pressure Capacity: As to the matter of fact, the SDR serves as the determining factor on the pressure capacity of the pipe. Pipes made with lower SDR on the other hand can withstand a considerable amount of internal pressure enabling them as good choices in high pressure endeavors.
- Durability and Longevity: Impact resistance and gradual impact wear are less likely in pipes that have been manufactured with lower SDR due to the fact that they have thicker walled pipes, thus making them more reliable.
- Cost Considerations:Investment wise, other than the thin walls, yes, the pipes with higher stds are cheaper but there durability and longevity are certainly not at the same level as those with lower stds.
- Choosing the Right SDR:
- Application Needs: Ask yourself, what are the operational needs and pressures I anticipate and what stresses will the environment push? Only then can I find a suitable SDR that meets my conditions.
- Regulatory Standards: Look into if there are specific rules for the industry which might attach certain SDRs with certain applications.
In selecting appropriate SDR, it is never enough to just satisfy the minimum level requirements but rather it guarantees that the pipe will be able to function well under service conditions as anticipated. Taking into account, the SDR along with other aspects like material specification and exposure, you can undertake thorough planning which maximizes both effectiveness and safety margins of your designs.
How Does Wall Thickness Affect HDPE Pipe Size?
It is important to note that the wall thickness of HDPE pipes dictates both their dimensions and their functional parameters. An increase in the wall thickness, resulting from a lower SDR, strengthens the pipe’s performance pressure-wise and renders it suitable for more stringent applications. Of course, an increase in the wall thickness causes a decrease in the internal diameter of the pipe, affecting its overall size and changing its flow characteristics. Therefore, in order to meet the different operating requirements, it is important to choose the wall thickness of the pipe correctly to balance the pressure capacity, mechanical strength, and efficiency of the hydraulic system.
Minimum Wall Thickness Requirements for Different Applications
Minimum wall thickness for different use cases is an interesting area for discussion and one that I would argue deserves focused attention. One would argue for high operating pressures, in order to address, to some extent, the environmental considerations and the governing standards on this matter. The implication here is that with high wall thickness, an external wall is inherently and reasonably guaranteed. Low pressure applications on the other hand, possibly allow for wall thickness to be kept at around level! And, so, it is understandable that industry standards and the strength of the wall would recommend a maximum and minimum level of wall thickness across multiple applications. Hence, in consideration of all these aspects, I would be able to make my recommendations in regard to specifications that would meet the technical requirements and also would be economically viable.
Impact of Wall Thickness on Pipe Size and Performance
While I do recognize that a number of organizations conducted many studies on the effect of wall thickness on pipe size and performance, I would like to discuss these issues in simple terms by using an analogy. Consider a pipe as a tunnel – the stronger it is , the thicker its walls will be, and the larger its internal diameter.
- Pressure Capacity: The wall thickness also determines the pressure Bearable of the pipe. This is important when the pipe has to support high internal or external pressure to avoid damage or breakage.
- Flow Rate: To a certain extent, a thicker wall means reducing the diameter of the pipe, which could act as a bottleneck for the flow. This is worth addressing on how it would be integrated within the system where there are possibilities to have high flow rates.
- Mechanical Strength: It is expected that as the wall thickness increases, so does the mechanical strength, allowing the pipe to withstand physical forces such as impacts or bending moments during installation or use.
- Material Cost: The more walls are thickened, the more material is needed for construction which means expenses also go up. Achieving the designed system that is strong and cost effective remains a challenge.
- Thermal Expansion: Different materials have different reactions to temperature changes. It is critical to be aware of the wall thickness and how it impacts the thermal expansion of the pipe and contraction, which allows the system to work over a prolonged period.
The contribution of these parameters is useful in making decisions concerning wall thickness in relation to the effectiveness and efficiency of pipes for any given purpose.
What Are the Benefits of Using HDPE Pipes in Water Applications?
The performance characteristics of HDPE pipes in water applications are impressive, most especially with regard to their ability to withstand pressure, flex, and endure stress. These pipes are highly resistant to corrosion and chemical leaching, which ensures the purity and safety of water. Their structural and physical characteristics also tend to render them unnecessary for joints and fittings, which are one of the main causes of leakage. Another benefit is that dust and sediment do not stick to the insides of the pipes, thereby enhancing the internal ‘flow’ of the water, which uses less energy and less friction. Due to their lightweight nature, these fittings are also easy to handle, which lessens the cost of labor. These characteristics render HDPE pipes a reliable and inexpensive option for the current methods of water distribution.
Advantages of HDPE Pipes for Potable Water Systems
What lifts HDPE pipes well above the rest for me is their suitability for potable water systems. In my view, the greatest advantage HDPE possesses is its resistance to corrosion and chemical leaching, guaranteeing the intake of safe and clean drinking water. Their flexibility greatly eases the installation process by minimizing the number of joints required, which in effect drastically cuts down on the potential leak points, one of the major concerns towards the upkeep of the system. The low density of high-density polyethylene pipes has proven advantageous over time because of the reduction of labor and time costs during installation. Also, the internal surface of HDPE pipes is smooth, making the internal fluid flow high while energy wastage is low due to a reduced friction force. These sets of advantages thus make HDPE pipes the greatest fit in today’s water distribution systems, advising both quality and price ratios.
Using HDPE Pipes in Irrigation Systems
Allow me to highlight my expertise in the field and discuss how HDPE pipes are very reliable in irrigation systems. The first point to be made here is the matter of their longevity. It is well known that HDPE pipes can withstand significant impacts, stresses, and cracks, which is quite common, especially during high-pressure and heat exposure of the pipes in irrigation systems.
Let us now move to the second point that has to do with flexibility. Because of the fact that HDPE pipes are able to bend freely, they are able to maneuver around certain obstructions without having to add more joints. This flexibility eases the entire process of fitting them into position, not to mention the amount of time and labor cost which is saved.
Let us now turn to the issue of resistance to in HDPE piping, as it relates to. In irrigation, when many other chemicals, not just fertilizers are used, HDPE pipes do not corrode easily which preserves the water quality and the pipes themselves as well.
Of interest as well, is the fact that they have comparable performance levels in hydraulic applications. Because HDPE pipes have a smooth inner surface, the resistance when water flows through them is extremely low. As a result, less power is needed to push water through them.
To conclude, it is also worth mentioning that HDPE pipes are economical. This has been made possible by the reduction of labor and transportation costs. All in all factors above make the case for HDPE pipes in irrigation systems very strong.
Comparing HDPE Pipes with Other Pipe Materials
With industry experience, I appreciate the significance of material selection in irrigation systems. When looking into the uses of HDPE pipes vis a vis other pipes, a number of influential factors ought to be taken into account so as to appreciate the rationale behind the preference accorded to pipes made out of HDPE.
- Durability: HDPE pipes are very strong in nature, do not get damaged easily, and have good resistance against weather conditions and impacts. In contrast, cold weather can cause PVC pipes to become brittle, whereas HDPE pipe can survive a variety of conditions. Less replacements will therefore be required over time and lesser maintenance will be needed.
- Flexibility: HDPE is a material that has more flexibility than other materials, such as concrete or steel. Such flexibility gives it the ability to move or Twist around structures without fracture which is not the case with rigid materials. Fewer components also mean that fewer joints are required for the installation of HDPE, resulting in less weak points and faster installation time.
- Chemical Resistance: HDPE pipes are especially useful in areas where there are chemicals, such as fertilizers, as they are less reactive. HDPE pipes do not develop a rust-like corrosion over time which is what happens to metal pipes, this increases the usable life of the irrigation system. On the other hand, Beispielsweise kann verzinkter Stahl rosten und korrodieren und damit die Wirksamkeit des Systems beeinträchtigen.
- Hydraulic Efficiency: Because of having a smooth internal surface, HDPE pipes can sustain good vacuum flow rate which metals pipes are able to provide at first but deteriorate over time. This characteristic helps to minimize the amount of energy required to pump, in comparison to concrete or metal pipes, which helps save money on energy in the future.
- Cost-effectiveness: Although materials such as copper or steel may cost more for the material itself, HDPE is cheaper and easier to handle owing to its low density. This not only reduces the costs of materials but also the cost of transportation and the labor involved during the installation process.
A compressive assessment of these parameters indicates that HDPE pipes are an all-purpose kind of piping material which has the added advantage of being cost effective in contrast with other conventional pipe materials used in irrigation systems.
How do you calculate the required inside diameter for your project?
First, determine the volumetric flow rate of the fluid (in GPM or L/s) that is going to be pumped through the pipe, and then note the velocity, which should be reasonable to reduce turbulence and wear. For many applications, this is between 1 to 2 meters per second. Some applications have higher maximum velocities (for example, hydraulic transport), while others have lower ones (for example, a gas pipeline). The figure above might be converted to volumetric flow rate using the formula D to S formula D=SQRT (4xQ)/(PI V) where D is diameter, Q is the flow rate and V is the velocity. At this phase, the nominal inside diameter of the piping system to maintain efficient flow in the system has been illustrated. Additional engineering judgment and safety factors for the specific application must always be kept in mind.
Step-by-Step Guide to Calculate ID for HDPE Pipes
Determining the internal diameter of an HDPE pipe is a crucial step in the AI design process. Here is how this can be done easily:
- Determine the Flow Rate: The first task is to establish the amount of liquid supposed to pass through the pipe. This rate of flow is usually given as a volume unit per time, for instance, gallons per minute (GPM) or liter per second (L/s). Having an idea of what flow rate is expected for the pipe will be useful in selecting a pipe diameter that will not be a limitation to the flow.
- Consider the Flow Velocity: Also, velocity or the speed of a moving fluid through the pipe is important. Preferably, you want the velocity to be moderate so that there will be no damage or erosion of the pipe. Such velocities typically range from 3 to 6 feet per second which is equivalent to 1 to 2 meters per second.
- Use the Diameter Formula: Keeping these parameters in mind, one has the formula as (D =\sqrt{(4 \times Q)/(\pi \times V)}),(D) in this case is diameter, (Q) is the flow rate, and (V) is the velocity. This helps find an adequate diameter to cover the conditions of a pipe.
- Adjust for Safety Margins: Please allow yourself and your calculations enough confidence and changes allowance by adding additional safety margins for any possible unanticipated factors that may interfere with your application. This is to allow the system to be able to deal with minor changes in the flow or pressure without causing a problem to the system.
In this way, you can be assured on how to compute the inside diameter that has to be used for HDPE pipes in a project while considering smooth flow transmission and strength parameters.
Considerations for Gas Distribution Systems
There are specific considerations that should be taken into account to ensure both safety and efficiency when designing gas distribution systems using HDPE pipes:
- Pressure Ratings: Opt for pipes with suitable pressure ratings that would be able to withstand the specified gas line pressure. Therefore, it’s one’s responsibility to check a pipe’s pressure rating with the system’s maximum operational pressure to keep any failure at bay.
- Material Compatibility: Confirm availability of appropriate HDPE material that would be suitable with the type of gas transported. Different grades of HDPE may be necessary for different gases to avoid waste or reactions from occurring.
- Environmental Conditions: Take into consideration the environmental conditions such as temperature ranges and exposure to ultraviolet radiation which can influence HDPE pipes throughout the installation of the pipes. It is best to use pipes that are already UV resistant if they are going to be exposed.
- Installation Techniques: Safety measures such as protective measures should be put in place, Training should be provided to everyone that is in charge of the gas distribution system including supervisors, to maintain gas distribution systems. This helps ensure leaks do not occur as a result of incorrect joining processes such as butt fusion or electrofusion.
- Regulations and Codes: Local and international laws should be put into consideration when dealing with gas distribution systems as safety measures, these might include pipelining and installation procedures that are alternative to yours. To do this, one may require practical permits as well as certain requirements.
- Monitoring and Maintenance: Implement a comprehensive monitoring and maintenance schedule to detect any issues early on and perform necessary repairs. This helps to prevent potential leaks and ensures the system operates efficiently over its service life.
Indeed, such criteria enable the designers and the engineers to properly incorporate the benefits of HDPE pipes in the gas distribution systems that will be reliable and safe.
Where to Find Assistance: Contact Us for Expert Guidance
I’m happy to clarify any misunderstandings that may arise with regard to using HDPE pipes in gas distribution systems. So let us consider these step by step :
- Pressure Ratings: It is essential to select the appropriate pressure rating for HDPE pipes. To begin, identify the maximum operating pressure (MOP) of your unit. The pressure class or PN or pressure number of the pipe is then baselined with the MOP. For increased safety, it is fundamental that the pipe has at least the same pressure rating as the MOP.
- Material Compatibility:It is necessary to ensure that the HDPE grade selected will be compatible with the gas to be transported. This is important as gases transportable in HDPE may affect its integrity or result to a chemical reaction. This is important because incompatibility will be revealed through manufacturer’s instructions or the chemical resistance chart.
- Environmental Conditions: It is important to take into consideration temperature variations and UV exposure which could determine the use of HDPE. For example, where pipes are installed above ground, consideration ought to be given to whether they are resistant to UV light and for what period. The best way to do so will be by considering temperature de-rating data in relation to the correct pipe size and type.
- Installation Techniques: For leaks to be reduced, proper installation has to be carried out. Make it a point to educate your staff on alternate means of joint construction such butt fusion or electrofusion. By using these techniques, molecules of the pipe components interconnect, which increases the strength between the parts.
- Regulations and Codes: There are no trade-offs when it comes to adherence to compliance rules, standards and regulation. Start off by researching calipers code which includes gas systems, its installation and permitting procedures which ensures that you are compliant and your entire system is safe.
- Monitoring and Maintenance: Set up a schedule regarding monitoring and maintenance of the system. If done regularly, visual inspections and pressure tests can identify places for possible leaks in the gas distribution system. This is critical to the development and security of your gas distribution system as it provides for a preventative maintenance program that includes the said inspections.
For any additional help or for expert advice, please feel free to Get in Touch. We are happy to assist you at every phase.
Reference
- PE4710 HDPE Pipe Sizes – This source provides a comprehensive chart for IPS and large-diameter metric HDPE pipe sizes, including pressure ratings.
- IPS HDPE Pipe Chart – A detailed brochure that includes standard sizes and DRs for HDPE pipes.
- High-Density Polyethylene (HDPE) Pipe Chart PE4710 – Offers a condensed chart displaying common sizes and SDRs for HDPE pipes.
- ADS N-12 HDPE Pipe Dimensions & Sizes Chart – Provides dimensions and sizes for ADS N-12™ HDPE pipes, available in various diameters.
Frequently Asked Questions (FAQs)
Q: What is HDPE, and why is it commonly used in pipe manufacturing?
A: HDPE stands for High-Density Polyethylene, a type of plastic known for its high strength-to-density ratio. It’s commonly used in pipe manufacturing due to its durability, flexibility, and resistance to corrosion and chemicals, making it ideal for a wide range of applications.
Q: How are HDPE pipe sizes measured and classified?
A: HDPE pipe sizes are measured by their outside diameter and are classified by their diameter and wall thickness. These measurements are standardized to ensure compatibility across various systems and applications.
Q: What is the significance of the SDR in HDPE pipe sizing?
A: SDR stands for Standard Dimension Ratio, which is the ratio of the pipe diameter to its wall thickness. It is significant because it indicates the pipe’s pressure rating; a lower SDR means a thicker wall and higher pressure capacity.
Q: How can I convert HDPE pipe sizes to different measurement units?
A: To convert HDPE pipe sizes, you can use conversion charts that provide equivalent measurements in different units such as inches, millimeters, and nominal pipe size (NPS). These charts are essential for international projects where different measurement systems are used.
Q: Are there specific advantages of using HDPE pipes over other materials?
A: Yes, HDPE pipes offer several advantages including flexibility, chemical and corrosion resistance, long lifespan, and a lower environmental impact. Their lightweight nature also makes them easier to install and transport.
Q: What are the common applications of HDPE pipes?
A: HDPE pipes are widely used in water supply, sewage systems, gas distribution, irrigation, and industrial applications due to their robust properties and versatility.
Q: How do customer reviews impact the selection of HDPE pipes?
A: Customer reviews provide insights into the performance and reliability of HDPE pipes in real-world applications. Positive reviews can boost confidence in a product’s quality and suitability for specific needs.
Q: What maintenance is required for HDPE pipes to ensure their longevity?
A: HDPE pipes require minimal maintenance due to their resistance to corrosion and chemicals. Regular inspections and proper installation are generally sufficient to ensure their longevity and performance.
Q: How do environmental factors affect HDPE pipe performance?
A: HDPE pipes are designed to withstand various environmental factors such as temperature fluctuations and UV exposure. However, extreme conditions may require specific grades or additional protective measures to maintain performance.