In infrastructure projects, proper installation of HDPE pipes is paramount for long-term performance and structural integrity. One major aspect of a successful installation includes meeting the minimum cover requirements for HDPE pipes. These requirements safeguard the pipes from external stress or damage while also aligning with relevant industry standards and regulations.
Importance of Minimum Cover for HDPE Pipe
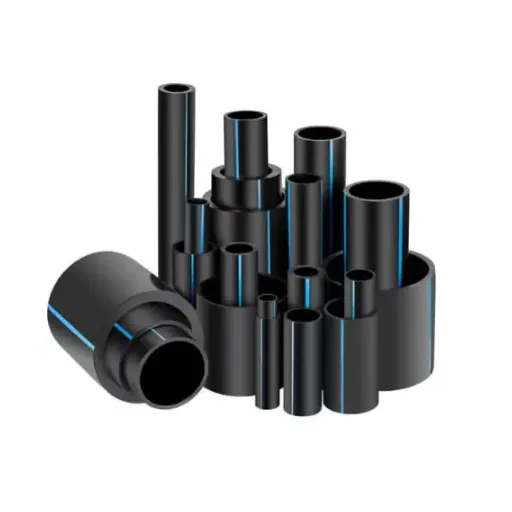
Industry Standards: AASHTO and ASTM Guidelines
These standards ensure that installations retain their structural integrity, durability, and safety against the variations of loading and environmental conditions that may be expected during installation. AASHTO concentrates on the application of HDPE pipes in transport infrastructure, requiring cover depths depending on live loads, vehicular traffic, and soil composition. ASTM works with material specifications and testing methods to guarantee that HDPE pipes meet standards of uniform quality and performance.
Key Standard Recommendations:
- The AASHTO LRFD Bridge Design Specifications recommend a minimum cover of 12 inches for HDPE pipes under traffic loads when pipe installation is performed with appropriate backfill material and proper compaction
- ASTM D2321 emphasizes installation practices regarding trench width, bedding preparation, and backfill compaction
Adhering to AASHTO and ASTM standards ensures regulatory compliance while maintaining higher performance standards and reliability of HDPE pipe systems. Site-specific conditions must be considered by engineers and contractors to consult these guidelines for exact requirements on cover during design and installation.
Impact of Minimum Cover on Pipe Longevity
Minimum cover depth directly influences the lifespan and functional operation of HDPE pipe systems. The following factors describe how minimum cover affects pipe longevity:
Protection Factor | Impact | Consequences of Inadequate Cover |
---|---|---|
Surface Load Protection | Greater cover depths protect heavy surface loads from vehicles or equipment | Pipe deformation or collapse under concentrated loads |
UV Degradation Prevention | Proper cover shields from sun exposure | Material degradation, reduced polymer structure strength |
Thermal Insulation | Adequate cover insulates from extreme temperature variations | Thermal stresses, compromised material integrity |
Erosion Resistance | Adequate cover resists soil erosion or scour formation | Pipe exposure, operational life reduction |
Ground Movement Mitigation | Sufficient cover absorbs and distributes local soil movement effects | High stress concentration on pipe structure |
Consequences of Non-Compliance
Warning: Missing minimum cover requirements can lead to:
- Structural failure and loss of performance
- Costly repairs or complete replacements
- Pipe cracking, deformation, or collapse
- Reduced resistance to external impacts
- Leakage and environmental contamination
- Legal and financial implications, including fines and project delays
Factors Influencing Minimum and Maximum Cover Requirements
Soil Type and Its Effects on Cover Heights
The nature of soil directly determines bearing capacity, drainage, and erosion potential, which sets minimum or maximum cover requirements:
- Cohesive soils (clay): Provide higher stability but pose drainage problems that may create pooling and stress
- Non-cohesive soils (sand/gravel): Facilitate water infiltration and drainage, but may require higher cover depths due to lower load capacity
- Loose or poorly-compacted soils: Usually require increased cover to protect pipes and reduce deformation risks
- Well-compacted, high load-tolerant soils: May allow reduced cover without compromising safety
Load Conditions: Live Load Considerations
Live loads are transient and dynamic loads that change with time or usage circumstances. These include:
- Vehicular traffic
- Pedestrian movement
- Equipment shifting
- Impact factors and vibration effects
- Load surcharges from unforeseen conditions
Numerical analysis methods like finite element analysis (FEA) provide exact simulations of load distributions and foster optimized design.
Pipe Diameter and Its Role in Cover Specifications
Diameter Impact Factor | Description | Example |
---|---|---|
Load Distribution | A larger diameter requires increased cover depth to prevent crushing | 48-inch diameter pipe requires ~36 inches minimum cover under heavy vehicular loading |
Hydraulic Efficiency | Diameter governs flow volume capacity | A smaller diameter needs less cover but may increase friction |
Material Strength | Works with the diameter to determine the needed cover | Flexible HDPE depends more on soil support than rigid materials |
External Loading | Environment and anticipated loads interact with the diameter | Bigger diameters may need engineered backfill and compacted soils |
Regulatory Compliance | Standards specify minimum covers based on diameter categories | ASTM standards vary and cover requirements across diameter ranges |
Installation Guidelines for HDPE Pipes
Minimum Cover Requirements for Various Applications
Application Type | Minimum Cover Depth | Special Considerations |
---|---|---|
Road Bases (Traffic Areas) | 12 inches (300mm) | Must resist vehicular loads as per pavement construction specifications |
Non-Traffic Areas | 6 inches (150mm) | Fields, walkways, and similar low-load applications |
Heavy Truck Loads/Railroad Crossings | 24 inches (600mm) or higher | Depends on design calculations and load analysis |
High Groundwater Areas | Variable | Must compensate for buoyant forces to maintain pipeline stability |
Best Practices for Backfill and Burial
ASTM D2321 Requirements:
- Backfill material should reach a compaction of at least 90% Standard Proctor density
- Use well-graded granular materials (crushed stone or gravel with few fines)
- Trench width should be 1.25 to 1.50 times the pipe diameter
- Place backfill in layers not exceeding 6 inches (150mm) in thickness
- Compact each layer thoroughly before placing the next
Additional Considerations:
- High groundwater or changing soils: Consider geotextile fabric to stabilize trench sides
- Heavy traffic areas: Ensure backfill material and compaction can withstand anticipated forces
- Compaction methods: Use mechanical or hand-operated equipment that won’t damage pipe structure
Common Installation Mistakes to Avoid
- Improper Trench PreparationLoose or uneven bottoms lead to uneven stress distribution and potential structural failures. Ensure uniform compaction without coarse materials that could damage the pipe.
- Inadequate Backfill Material CompactionPoor compaction causes uneven load conditions, increased pipe deflections, and diminished performance. Follow compaction specifications and use properly graded granular soils.
- Incorrect Pipe Jointing TechniquesMisaligned joints, surface contamination, or insufficient heating during thermal fusion create weak points. Enforce standardized fusion standards with certified personnel.
- Ignoring Thermal Expansion and ContractionHDPE pipes undergo considerable thermal effects. Incorporate expansion joints, proper anchoring, and movement accommodation to prevent buckling or joint separation.
- Improper Handling and StorageDragging on rough surfaces or prolonged sunlight exposure causes surface damage and material degradation. Store on flat surfaces protected from environmental elements.
Coverage Depth Comparison: Urban vs. Rural
Urban Installation Considerations
- Minimum cover: 1.5 to 2.5 feet, depending on vehicular loads and soil characteristics
- Protection methods: Encasement or thicker-walled pipes under heavy traffic
- Utility conflicts: Use GIS and SUE mapping tools to detect underground utilities
- Traffic management: Implement comprehensive plans for road closures and pedestrian safety
- Accessibility: Plan access points and inspection chambers for maintenance
- Backfill: Granular material preferred for uniform load distribution
Rural Installation Considerations
- Flexibility: More route selection options with less infrastructure interference
- Soil analysis: Detailed stability assessment, especially in agricultural lands
- Erosion control: Critical near slopes or heavy precipitation areas – use geotextiles or vegetation restoration
- Environmental impact: Conduct thorough assessments to minimize biodiversity damage
- Logistics: Special planning for material transport to remote locations
- Advanced techniques: Consider trenchless technologies like horizontal directional drilling
Comparative Analysis of Coverage Depths
Climate/Environment | Minimum Cover Depth | Key Considerations |
---|---|---|
Freeze-Terrain Areas | Above frost line (20-100+ inches) | Varies from 20 inches in warmer climates to over 100 inches in cooler climates |
Arid Areas | Shallow cover designs are possible | Can reduce material expenses while providing adequate structural support |
Enhanced Designs | Optimized with reinforcement | Reinforced bedding materials or geotextile layers enhance load-bearing capacity |
Updates to HDPE Pipe Covering Requirements
2025 Changes in ASTM F2160 Standards
Key 2025 Updates Include:
- Enhanced ESCR Testing: Stricter environmental stress cracking resistance requirements
- Dimensional Tolerance Improvements: Better compatibility with fiber optics and 5G infrastructure
- Extreme Temperature Performance: Expanded criteria for varied climatic conditions
- Accelerated Life Cycle Assessments: Integration with sustainability practices
- Environmental Compliance: Alignment with carbon footprint reduction and material efficiency directives
Green Building Applications and Electric Vehicle Charging Stations
The integration of sustainable infrastructure includes:
- Energy-efficient materials: High insulation, low-emissivity glass, recycled composites
- Smart grid compatibility: Optimized energy consumption and demand adaptation
- Renewable energy integration: Photovoltaic installations on EV charging stations
- Advanced power management: DC fast chargers with optimized energy transfer
- System interconnection: Strong approach to design and protocol compatibility
Future Trends in HDPE Pipe Installation and Compliance
- Trenchless TechnologiesGrowing acceptance of HDD and pipe bursting methods for reduced surface disruption and shorter project timelines.
- Smart Monitoring SystemsIoT sensors provide real-time data on pressure, flow rate, and potential leaks for proactive system management.
- Sustainable MaterialsAdvanced polymer blends offering greater strength-to-weight ratios, better chemical resistance, and improved recyclability.
Frequently Asked Questions (FAQ)
References
- Iowa State University – Depth of Bury Tables: Details cover depth requirements for various pipe diameters
- University of Kentucky – Installation of Pipe: Discusses minimum cover heights and construction loading requirements
- South Carolina Department of Transportation – Pipe Installation Guide: Covers minimum cover, installation, and backfill requirements for roadway applications
- University of Delaware – Proper Pipe Installation Practices: Explains minimum cover requirements due to design loads and exceptions