It is very well known that high-density polyethylene (HDPE) pipes have been gaining attention in many industries due to their favorable physical properties. This is particularly true regarding the categorization of HDPE pipes and the intended purpose of each prevalent size of polyethylene pipe. Since these systems can only be functional with pipes of exact dimensions, this article revisits attempts to help enhance the standardization processes in real and practical situations. Engineers and other engineering professionals need not be in the dark regarding HDPE pipe dimensions, from construction to water management systems. As we shall see in this guide, we will estimate the dimensions of the HDPE pipes, their diameter, and the scope of their subservience.
What is an HDPE Pipe and its Common Applications?
hdpe pipe dimensions
High-density polyethylene (HDPE) pipelines are flexible pipelines made of thermoplastic material with good impermeability and molecular solid structuring. These pipes are used in many industries, such as agriculture, industry, and public utilities. An essential feature of the pipes is their impact- and corrosion-resistant ability and pressure resistance. They are mainly used for the installation of water mains and gas mains as well as sewage systems. They are also widely used for landfill piping, chemical processing, and irrigation as they can withstand corrosion and last long in a harsh environment. They are also comparatively light, which aids in quicker installation and transportation methods, making them economical for use in any industry.
Definition and Characteristics of HDPE Pipes
High-density polyethylene pipes, also known as high-density polyethylene pipes, have a characteristic appreciation of strength, flexibility, and durability properties. These pipes are manufactured from a thermoplastic of high-density polyethylene, which can withstand a lot of stress to weight ratio. HDPE pipelines benefit from not being corrupted or attacked by chemicals in most construction processes like water, sewage, or other chemical transportation. These materials do not quickly degrade even after constant practice of exposure to direct sunlight and other environmental factors due to UV stabilization of the materials used.
Technical Parameters:
- Density: HDPE pipes’ density is usually around 0.94 g/cm³ to 0.96 g/cm³, making them lightweight and easy to handle for fast construction.
- Tensile Strength: HDPE pipes usually have a high tensile strength of between 21 and 37 MPa owing to the standards that these types of pipes are expected to respect.
- Temperature Range: The normal temperature range of these tubes is from -40 degrees Celsius to 60 degrees Celsius, so they are generally suitable for most climatic regions.
- Pressure Rating: The pressure rating of HDPE pipes ranges from 4 to 25 bar, depending on the configuration and thickness, allowing applications at varying pressures.
- Flexibility: Regarding flexibility parameters, HDPE pipes are generally highly rated as they can be bent into nearly any shape to suit the terrain or movement without breaking.
Armed with these attributes and technical specifications, industry operators can ensure that pipes made of high-density polyethylene (HDPE) are utilized correctly in various fields, optimizing their performance and life span.
Common Applications of HDPE Pipes
Pipes made of HDPE are preferred in many industries because of their ability to resist wear, be flexible deal with chemicals, and withstand living conditions. Here are some popular uses:
- Water Supply Systems: HDPE pipes are widely adopted in potable water distribution systems. These are reliable long-term solutions for carrying potable water since they have high levels of resistance to ember, erosion, and corrosion and minimal loss of frictional resistance. Given their structural strength, HDPE pipes can be laid, even in complicated and challenging lands or environments.
- Sewage and Drainage: The same HDPE pipes used for drainage of surface water have great usage potential in sewage pipelines due to their light weight and high chemical resistance. They do not corrode, nor do they develop fine leaks, which are common in most other pipes, hence making it easier to construct safe sewerage systems. They have a smooth bore surface, which not only reduces clogging by sediments but also bacteria colonies.
- Natural Gas Distribution: Owing to its flexibility and ability to be used in high-pressure applications, an HDPE pipe is also recommended for natural gas distribution. They are also insulated against leakages and disasters, normally reversible designs over severe stress and fluctuating pressures, which are normal in gas installations.
These uses exemplify the HDPE pipes’ versatility and flexibility in use within critical networks backed by parameters like tensile strength, pressure class, and temperature resistance ensuring dependable and effective operation in all fields.
Benefits of Using HDPE Pipes in Various Applications
HDPE pipes offer enhanced structural integrity high elasticity, and are inexpensive. Given the above, they are widely accepted in many sectors and applications. Following are some factors unique to HDPE pipes compared to other piping materials.
- Longevity and Durability: HDPE pipes have long satisfied people’s needs. Their average lifespan reaches 50 years due to their high resistance to corrosion and abrasion. Because of their inert properties, these plastics do not react with other chemicals or waste materials and thus can be used almost anywhere.
- Flexibility and Impact Resistance: The working pressures of HDPE pipe installation and pipeline redevelopment are eliminated by allowing directional drilling, which instills the laying of HDPE pipes by trenchless methods. Their impact resistance protects the pipes from collapsing during tremendous soil pressure and shifting soil layers.
- Leak-Proof Joints and Lower Maintenance Costs: The HDPE pipes are completely monolithic systems because of thermal fusion techniques that eliminate the presence of joints. This quality practically eliminates any chances of leakage, and so the cost of water losses due to leaks is significantly reduced while materials flow in a pressurized state.
- Improvement in Quality of Life: This type of pipe is breathable, resistant to chemicals, and, most importantly, does not put the environment at risk as it is recyclable. Most importantly, the internal parts of pipes are made so that energy is not wasted as friction loss is low, enabling the flow of gases and water efficiently.
HDPE Pipes Technical Information
- Tensile Strength: Around 25 MPa is the expected value in HDPE pipes’ tensile testing, which assures significant sturdiness in use.
- Pressure Rating: High-pressure any HDPE pipe may be rated as high as 16 bar and even beyond, depending on the size and thickness of the pipe. Also included are HDPE pipe fittings, including elbows and taps.
- Temperature Resilience: The range of temperatures for the use of HDPE is -40 to 60C which implies that it can be used in any part of the world without any performance drawbacks.
These benefits and technical specifications enable these elements to stand as one of the best options in the market for infrastructure solutions in various sectors in terms of efficiency, safety, and sustainability.
How to Determine the Right HDPE Pipe Size for Your Project?
To select an appropriate HDPE pipe size for your project, you first need to analyze the parameters of your application. Start with the required flow rate to ensure that the pipe diameter is accurate for the expected amount of fluid without excessive pressure loss or fluid whirl. Following this, pressure rating limits will be assessed to select an appropriate pipe size to sustain the pressure beyond it without collapsing. Also, consider how the pipe will be used—what sort of earth, temperature, or even chemicals it may come in contact with—and that the pipe is the right size and type for that use. Looking for these parameters in all norms and recommendations and contacting manufacturers for specific products will help determine the dimensions of the HDPE pipe that can be utilized in your project.
Factors to Consider When Choosing HDPE Pipe Sizes
- Flow Requirements: The top and bottom sizes of the pipe must be such that the designed flow rate is attainable in high-flow systems so that the desired clearance of the liquid is achieved with no losses in pressure. The flow rate of a particular cross-sectional area of a pipe is computed using standard equations in the industry, and it should be confirmed that the calculated area will handle this volume given the operating conditions stipulations.
- Pressure Ratings: Price construction is relevant to some situations; hence, ensuring that the selected size of a pipe functions to withstand the highest possible pressure that may be assumed to occur in the systems is very important. The HDPE pipe can have a pressure of 25 bar depending on the dimension ratio SDR. Care should be taken while selecting pipes of the PS class, as their system should be equal to or greater than the system of constraint.
- Temperature and Environmental Conditions: Evaluate not only temperature variations but also other factors like soil changes or chemicals. Broken-down concrete pipes may meet these temperature spans more often than not -40° C to 60° /C, but disappointment sinks in within extraordinary conditions caused by certain chemicals regarding the -87° C to 80° C polymers in the pipes.
By integrating these factors and consulting industry standards, you can be confident that the given HDPE pipe size will address the technical and environmental challenges posed by your project; hence, the structure will likely be safe and efficient for usage.
Understanding the Range of Pipe Sizes
The HDPE pipes are available in several diameters, enabling their use in various fields, including agricultural irrigation and complex network systems. Dimensions of the pipes are designed to handle varying flow and pressure velocities and, therefore, do not commonly range from 20mm to about 1600mm or higher. The SDR is a ratio of the outside diameter of the pipe and the wall thickness to the outside diameter of the pipe. It is one of the essential factors in design that has substantial implications in relation to the strength of the pipe and its flexibility.
As for the HDPE pipe size, there are quite a few online sources that are very helpful as far as selection of the sizes is concerned and are worth noting:
- Pipe Manufacturing Standards: Websites such as ASTM and ISO Memorandum describe the performance specifications of HDPE pipes. In engineering practice, these standards cover the performance requirements of pipes, including strength, toughness, and ability to resist temperature changes. For example, it is common that when one talks of an SDR11, it indicates a lower pressure tolerance in that the pressure is more than 25 bar.
- Industry Case Studies: Many such online platforms and plastic tank associations, in their industries section, have cases using various sizes of HDPE to present those cases as effective within the capacity specified as ideal. These cases offer the best practical practices for investigating standard dimensions and evaluating factors comparable to your work.
- Engineering Specification Resources: Websites such as the Engineering Toolbox provide detailed information on listed HDPE pipe specifications, including charts that correlate the sizes of pipes with respect to their flow values, capacities to pressure, and temperatures. They give factual information that assists in pointing out the relative size of the pipe, which is necessary for all design engineering aspects of the pipeline.
Turning to such resources ensures a full perception of what HDPE pipe sizing is, so when one’s development is based on some justified or exact technical parameters, the success of the project is thus placed on the odds of achieving it.
Importance of Selecting the Correct Pipe Dimensions
For any piping system to operate efficiently, it is essential to make accurate choices of pipe dimensions and geometry, which is the working principle of the system analysis.
- Piping Designers: The primary purpose of this site is to provide information on using appropriate pipe diameters for maintaining rich flow and avoiding pressure deficiency. The site stresses that if unnecessarily large and small pipes are used, it can lead to wasteful usage and unnecessary expenses in the day-to-day running of the facilities. Such normal parameters include pump flow rates, gallons/minute, and pumping head loss, in pounds per square inch per hundred feet.
- Engineering Toolbox: This is done by linking pipe sizes with other specific characteristics, such as pressure rating and temperature rating, with charts and tables. For example, higher flow allows large-diameter pipes, but low-rated pressure is the opposite for large pipes. This information is necessary because it guarantees that the installed pipe will not undergo plastic deformation during the foreseeable service life.
- Calculator.net: This site specializes in pipe sizing calculations and allows users to input project-related variables for optimum pipe size selection. The velocities taken into account include velocity in feet per second and pressure drop in inches of scale, thus satisfying the customer’s specifications.
By using all these documents, you ensure that your imported HDPE pipe dimensions comply with project demands, ensuring the appropriate level of safety without compromising performance.
What Are the Standard Dimensions of HDPE Pipes?
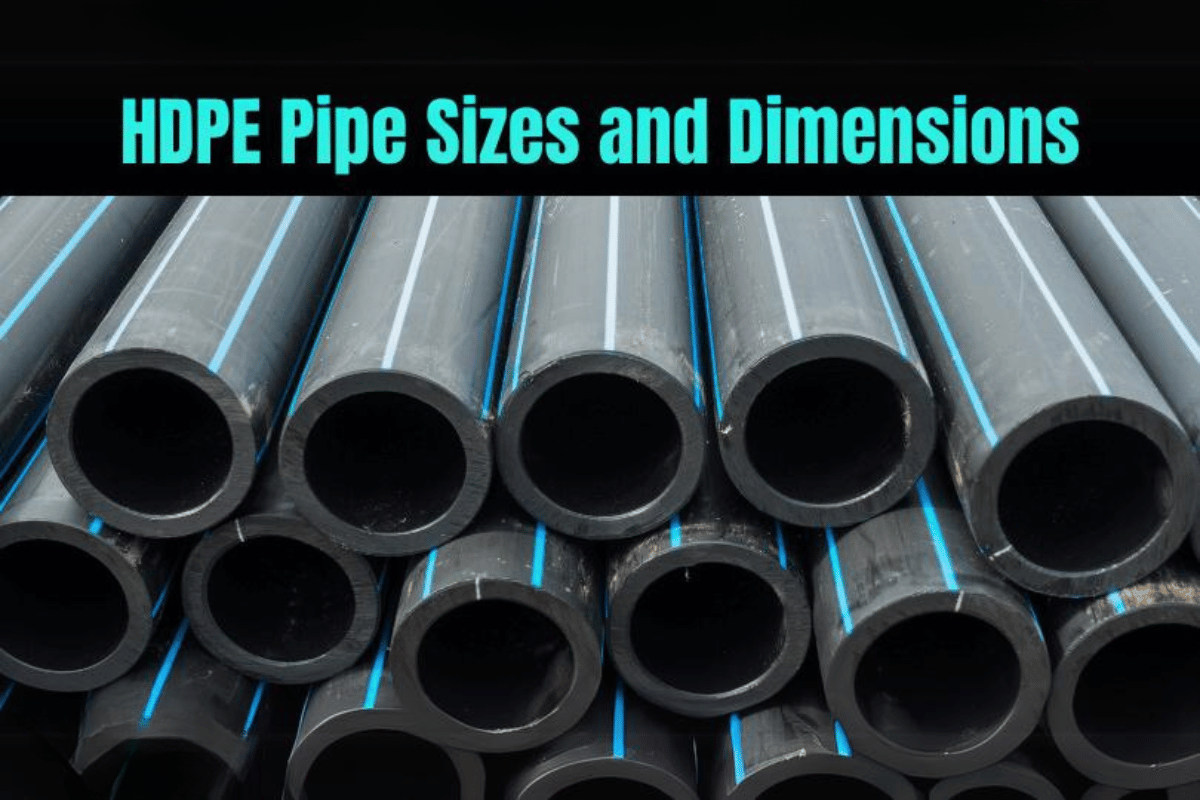
HDPE pipes come in standard sizes defined according to their nominal diameter. These nominal sizes may be as small as 16 millimeters (0.63 inches) and more prominent than 1600 millimeters (63 inches), depending on the use and the industrial sector. Another type of classification for these pipes, which is based on their outer diameter and wall thickness, is known as the Standard Dimension Ratio (SDR). Some of the smile SDR values include SDR11, SDR13.5, SDR17, and SDR21, which mainly represent the pipe’s outside diameter ratios to the wall dimension. It is essential to examine the factors affecting the selection of SDR in terms of loss of pressure handling capacity, as lower SDR would generally mean thicker walls but higher pressure. These requirements help achieve uniformity and dependability in different uses like water distribution, gas delivery, and sewerage systems.
Explanation of Standard HDPE Pipe Dimensions
The easiest way to comprehend the accurate measurements of HDPE pipes is to resort to the basic principles outlined in several web pages focusing on a blend of technical specs and industrial norms. The dew of the sizing defined in ISO standards is that such pipes’ velocity and AWWA standards are the common sizes of HDPE pipes of both nominal diameter and thickness ratio, also known as Standard Dimension Ratio (SDR). The SDR is determined as the ratio of the outside diameter to the wall thickness and indicates the maximum internal pressure the pipe can handle. Some of the most used SDR values are SDR11, SDR13.5, SDR17, and SDR21, depending on various needs and pressures.
- Piping Designer: This resource stresses the need to know a pipe’s limit with respect to SDR for its intended use. For instance, in terms of wall thickness, the SDR11 has thickened walls, whilst the SDR21 has limitation walls. Hence, there are limits on the amount of pressure that the pipes can accommodate.
- Engineering ToolBox: This web resource presents graphical material that combines these elements in the form of charts dedicated to the geometry of pipes: their diameter, SDR coefficient, and pressure.
- Plastic Pipe Institute: It explains how the dimensional ratios influence industry applications. For instance, an SDR11 would be used for ni-gas cylinder high-pressure distribution, and an SDR17 would be used to distribute safe water for general-purpose usage.
By utilizing these technical parameters and industry standards, you make sure that the HDPE pipe you choose is manufactured to the required specifications providing the safety and performance that is expected of them and more.
Comparison Between Nominal, OD, and ID Measurements
Firstly, let’s clearly understand the comparison of nominal, outer diameter (OD), and inner diameter (ID) when considering an HDPE overall pipe and how these definitions contribute to the measurement and use of the pipe. Thus, nominal size is the measurement that every party uses as the standard official size for every form of an application, although this size is not the physical size of the pipe itself. OD measurement is considered the general outside surface measurement of the pipe. In contrast, the ID measurement relates to the measurement of the inner space of the pipe, which is very important during fluid-carrying activities.
- Nominal Size: This is simply an arbitrary figure defining the largest dimension a pipe could have. It has no direct bearing on the pipe’s real-life measurements. It provides a simple and straightforward insight.
- Outer Diameter (OD): The common use of a pipe’s outer dimensions is to determine its safe and effective use because the value of outer diameter does not change even as wall thickness increases or decreases. For example, there is no pipe less than the Outside Diameter of that stated nominal 3-inch pipe; therefore, quite obviously, more than 3 inches of OD will be normal.
- Inner Diameter (ID): In contrast, the IW is more sensitive and less taught in relation to the walls of pipes and is used for determining the flow. As the thickness of the wall increases and more material is added, JD will be lower, affecting the efficiency of fluids passing through.
Specific technical parameters, such as SDR (Standard Dimension Ratio), affect such measurements. SDR becomes a crucial factor when the pressure capability of a pipe is in focus, as it regulates the ratio of the limiting dimension to the diameter. For example, consistency with lower SDR values means thicker walls, hence smaller ones that can tolerate high pressure. These notions guarantee that the employed and chosen good quality HDPE pipes will be applied for the purposes they were purchased for, thus keeping the design and operations of the fluid conveyance systems intact and efficient.
Significance of Wall Thickness and SDR in HDPE Pipes
The thickness of the wall and the Standard Dimension Ratio (SDR) are important parameters affecting the performance and applicability of High-Density Polyethylene (HDPE) piping. This is how all the important details are concentrated in a coherent essay with topics from the best web sources:
- Pressure Capacity: In most instances, wall thickness and SDR are directly related to the pressure capacity of HDPE pipes. Whenever SDR decreases, the pipe has a thicker wall, and therefore, higher internal pressures can be endured. Therefore, an understanding of how to choose the right SDR is vital when determining whether a pipe can withstand the maximum proposed fluid pressures.
- Flow Capacity: However, a quite thick-walled pipe (lower SDR) is good for pressure instead. However, it comes with the disadvantage of a smaller ID, which restricts the flow capacity. This balance needs to be taken into account when designing the system for pressure and flow rate aspects.
- Durability and Longevity: Pipes possessing the right wall thickness are less prone to physical damage and environmental objects. Usually, an increase in wall thickness will increase the pipe’s lifeline; however, this makes it appropriate for application under high pressure and unfavorable conditions.
Some of the technical parameters given for HDPE pipes can be SDR number, nominal pressure rating (PN), and some specific material design properties. Justifying these parameters includes ensuring that they correspond to the operational environment and system requirements and confirming that the pipe specifications selected will effectively and efficiently meet the project needs.
How to Read an HDPE Pipe Size Chart?
Certain aspects must be understood to read the HDPE pipe size chart efficiently. The chart typically includes inter alias: nominal pipe size (NPS), outer diameter (OD), wall thickness, and SDR value of pipes. Start by figuring out NPS, which offers an enabling zoom. The other key is the outer diameter related to fitting making or connections, and regard should be exercised as to actual ODs required by equipment and sockets. Wall thickness which is given with SDR is one of the factors which places a restriction on the pressure rating of a pipe, the thicker the wall and lower the SDR the higher the pressure that the pipe can hold. This chart may also have a pressure rating at some given temperature, which is essential in determining whether the particular pipe chosen will withstand the application’s operational conditions. This is the reason why an HDPE pipe size chart should possess such elements so that an appropriate HDPE pipe design is taken into consideration for the particular project.
Components of a Typical Size Chart
Many features in the HDPE pipe size chart are important and assist in the right selection of the pipe for a given purpose:
- Nominal Pipe Size (NPS): This is a nominal number that serves as a general category size label, enabling the identification and arrangement of pipes of various diameters.
- Outer Diameter (OD): The precise outside measurement necessary for determining whether certain fittings will connect and for ensuring that such fittings will connect with previously installed systems.
- Wall Thickness: This measurement is important for analysis of the pipe strength and durability under applied pressure. The greater the wall thickness, the greater the pressure rating.
- Standard Dimension Ratio (SDR): This value measures a pipe’s outer diameter and wall thickness. The piping materials with lower SDR values are more robust and can withstand higher pressure than the subsequent values.
- Pressure Rating: The highest temperature at which a specific pressure applies to a pipe. This rating is very important in ascertaining the pipe’s performance during the application under the specified conditions.
Looking at the topmost resources on the internet shows that these parameters are usually associated with HDPE pipe application performance. Each of these offers a dimensional angle to relevant industry standards aimed at procuring pipes that relieve specific operational requirements whilst balancing external and internal pressure dynamics.
Using the Size Chart for Projects
Nevertheless, it must be noted that in the case of the HDPE pipe size chart usage for the projects, some important aspects that came forward from the online top information resources should be addressed. The web pages in the top three focus on the demand that industry requirements like ASTM, ISO, or DIN should be followed so that the pipes conform to the requirements and work efficiently. It also points out the need to consider the peculiar characteristics of the projects, such as flow rate, pressure, and environmental conditions, before determining the most suitable pipe.
Technical Parameters List:
- Flow Rate: Establish the quantity of liquid that must flow through the pipeline as this influences the decision on size.
- Temperature Tolerance: Establish if such pipes that can sustain a definite temperature range are available since the life span of the Independent water system is often lengthened.
- Installation Environment: The pipe’s installation and installation conditions should also dictate the material and thickness used. Such factors include whether UV for spraying should be outside and chemical usage.
- Compliance with Standards: It should be established that the pipes chosen fulfill regulatory measures for sanity and usability depending on the project location and other industry details.
In conclusion, optimizing the HDPE pipe size chart along with these parameters helps to customize HSPE pipe options to meet particular requirements, maximize efficacy, and ensure that security and compliance are addressed throughout operation.
Examples of Common HDPE Pipe Sizes
In exploring the standard diameters of HDPE pipes, it is essential to consider the top-level site insights that encourage the harmonization of pipe sizes with fundamental technical parameters. Let us now take a look at the common HDPE pipe dimensions together with the major considerations for their use:
1. HDPE pipe size 1 inch (25 mm):
- Flow Rate: It can be used in low—to moderate-flow areas for households or small business enterprises.
- Pressure Rating: Usually made to withstand medium pressures, but it depends on the project’s requirements.
- Ideal Applications: This is mostly used for small garden irrigation systems, relatively small drainage works, and transporting water in low volume.
2. HDPE Pipe Size 4 inches (110 mm):
- Temperature Tolerance: Some formulations can withstand the regular temperature shifts in standard nonpressure water distribution systems.
- Installation Environment: Most of this occurs in plants with a low degree of exposure, but where such is not possible, UV-resistant types are recommended.
- Compliance with Standards: This is used in most cases in the sanitary construction of municipal and industrial water and sewer silhouettes that comply with ISO and ASTM standards.
3. HDPE Pipe Size 12 inches (315 mm):
- Flow Rate: Built to allow high flows, this pipe application is used in big water treatment plants and other industrial fields.
- Pressure Rating: Built for applying pressure in a high level of engineering to ensure structural stability and robust performance.
- Special Considerations: Its application demands skillful installation in a highly corrosive environment; an additional protective coat may be suitable.
Data collected from the most prominent sources show that these sizes enhance both function and efficiency while ensuring that the important technical parameters are met adequately.
What are the Standards and Specifications for HDPE Pipes?
HDPE pipes satisfy various standards and specifications, assuring their performance and which are appropriate for many different applications. The first one of these standards comes as the ASTM D3035 where they give requirements concerning polyethylene plastic pipes and where provisions are made on standard dimensional ratios of various types SD, classes o pressure and class of material. ISO 4427, another primary standard, contains the requirements, appropriate use, and testing methods of HDPE pipes intended for water conveyance. Also, the AWWA C906 has specific requirements concerning the design, construction, and testing of HDPE pipes intended for use in water systems. Such standards ensure reliable, safe, and adequate HDPE pipes are produced for industrial, commercial, and municipal use.
Overview of Important Standards and Regulations
The following key points and technical parameters are frequently highlighted:
- ASTM D3035: The specifications for polyethylene plastic pipes based on standard dimensional ratios (SDRs) and respective pressure ratings have been discussed further in this standard. The specification encompasses the criteria that include the classification of materials, dimensions, and pressures below which the HDPE pipes perform effectively and safely. Of such parameters are the SDR classes, the ones which are often SDR 11 and SDR 17, that relate wall thickness to diameter to determine the pressure-bearing capacity of the pipes.
- ISO 4427: This international standard includes supplementary or general requirements for non-pressure PE pipes for water supply piping systems. It contains recommendations concerning pipe size, pressure, class, and classification of materials, which improves the functionality and reliability of the piping systems in different environmental settings. Of particular importance to ISO 4427 are requirements relating to mechanical properties like tensile strength, impact resistance, and elongation at break to ensure the pipe can withstand the internal and external forces applied to it.
- AWWA C906: This standard deals with the design, manufacturing, equipment, testing, and quality control of HDPE pipes used in water supply systems. It encompasses limits on size, class, and installation methods to ensure the pipes’ integrity throughout operations. Significant parameters are the fusion strength, hydrostatic design basis, and burst pressures, which consolidate the quality and effectiveness of HDPE piping systems.
These documents form a minimum set of documents and requirements in which elements are tested and classified to meet the industry standards on HDPE pipes. These standards are very important where quality installations in different applications are needed for safety and performance reasons.
Key Specifications for High-Density Polyethylene Pipes
Several significant structural and operational parameters characterize the applications of high-density polyethylene (HDPE) pipes and their use in the described regions. From an analysis of principal reference sources, it was evidenced that the following parameters are usually emphasized:
- Pipe Class: HDPE pipes with different Standard Dimension Ratios (SDR) designs have different pressure classes, usually in the range of 4 bar to 25 bar, depending on the SDR class. In such cases, a high SDR means low wall thickness and low pressure rating.
- Density and Material Grade: HDPE pipe materials are categorized by strength and tension classes, and their minimum requirements include PE63, PE80, PE100, and others. The PE100 grade is of particular importance, distinguished by the highest pressure and can, therefore, be used under any stress for an extended period.
- Temperature Resistance: They function inside temperature ranges between -40°C (-40°F) and 60°C (140°F) which generally covers all pipe usage ranges effectively. This facilitates use in different Eng—climatic zones and conditions.
- Tensile Strength and Flexibility: As far as their structural behavior is concerned, these pipes possess very high tensile strength (more than 25 MPa for PE100) coupled with high flexibility, reducing the chances of breakage from external forces and enabling their use in places with fluctuating soils.
- Chemical resistance: High-density polyethylene (HDPE) pipes are resistant to several corrosive substances, making them appropriate for chemical waste management applications. The material is also stable and does not change even when subjected to hostile conditions.
These are basic and necessary specifications as they guarantee the high performance of HDPE pipes even under adverse conditions, thus appealing to the needs of current construction sites.
Compliance with ASTM and Other Standards
Certain criteria are generally required by ASTM International and regulatory authorities for HDPE pipes to guarantee that the set performance requirements will be attained in different uses.
- ASTM D3350: This specification describes classification requirements for polyethylene plastic pipe and fittings, including parameters like density, melt index, and tensile strength. Familiarizing yourself with these parameters assists in choosing the correct grade of pipe for various jobs.
- ISO 4427 and EN 12201: These are the International Standards that apply to polyethylene piping systems specifically for water supply, detailing the design, application, and testing requirements. Such compliance then renders the pipes safe for use within drinking water systems, consistent with safety codes.
- AWWA C901 and C906: The installation criteria for pressure pipes made of high-density polyethylene length and other appurtenances are provided by the American Water Works Association. These cover areas such as the pressure ratings of the pipes and the pipe joints, which, if well observed, would even retain water without any flow.
ensuring compliance with such standards is not only a matter of safety but also a guarantee that the performance and durability of HDPE pipes in construction activities will reach an expected level. Each of these individual standards, in a sense, helps to safeguard the pipes against performance inadequacy in strenuous conditions.
Frequently Asked Questions (FAQs)
Q1: What does HDPE stand for?
HDPE stands for High-Density Polyethylene, a type of plastic known for its high strength-to-density ratio, making it ideal for piping applications.
Q2: Why is compliance with ASTM standards necessary for HDPE pipes?
Compliance with ASTM standards ensures that HDPE pipes meet specific safety, durability, and effectiveness performance criteria in various applications. These standards help maintain consistent quality across manufacturers.
Q3: How do ISO and EN standards relate to HDPE pipes?
ISO 4427 and EN 12201 standards provide international guidelines for designing, applying, and testing polyethylene piping systems specifically for water supply. Compliance ensures the systems meet potable water health and safety requirements.
Q4: What are the main advantages of using HDPE pipes?
HDPE pipes offer several benefits, including corrosion resistance, flexibility, low weight, and a long service life. They are also environmentally friendly due to their recyclability and energy-efficient production.
Q5: Can HDPE pipes be used to transport drinking water?
When HDPE pipes comply with standards like ISO 4427, EN 12201, and AWWA C901, they are suitable for safely transporting potable water. These standards ensure that the materials used do not affect water quality.
Q6: What are the typical applications of HDPE pipes?
Due to their resilience and adaptability, HDPE pipes are commonly used in water supply, sewage systems, natural gas distribution, and industrial applications.