High-density polyethylene (HDPE) pipes find broad acceptability across industries owing to their strength, flexibility, and affordability. This detailed guide is meant to enhance the understanding of the polyethylene pipe dimensions and how they can benefit the readers. From the most miniature household plumbing systems to the most significant commercial engineering applications, HDPE pipes offer an excellent solution for transporting fluids and gases. The author will outline standard pipe size determining HDPE factors and its dimensions understanding and standards relevant to pipe uses. After reading this guide, the reader will have sufficient information to choose the most appropriate HDPE pipe size they intend to use for maximum efficiency for those applications.
What is HDPE Pipe, and Why is its Size Important?
hdpe pipe sizes
In practice, High-Density Polyethylene (HDPE) pipe is a high performance and durable plastic pipe that is highly resistant to chemicals, corrosion and environmental pressures. Its flexibility and tensile strength help it find utilities ranging from water and gas transportation to sewage and industrial effluent treatment. An HDPE pipe size is crucial because it affects the flow rate and pressure, the two primarily designed fluid and gas transport system elements. Besides, sizing dispensing is essential to prevent mismatching with systems already in place and standards that exist in the industry, all of which end up dictating the performance and life of the pipe. This is important to facilitate the proper functioning of the piping system to turn out the outcome of resiliency with maximum utilization on both the scale of domestic and industrial.
Definition and Benefits of HDPE Pipes
Definition: HDPE is defined as high-density polyethylene pipes or sentiments, which are hard but bendable plastic composites made from petroleum. These conveyance systems are interesting as they are also made of thermoplastic polymers and, therefore, perform well and are durable under many adverse circumstances.
Benefits: The HDPE pipes do have many advantages:
- Corrosion Resistance: Unlike metal pipes, HDPE pipes do not develop rust and corrosion, which allows for their prolonged use.
- Flexibility and Toughness: The rising popularity of HDPE pipes can be attributed to the fact that these materials can also be bent, which will ease the installation of the pipes in instances where it is important for the pipe to twist to run along narrow paths or over rough terrain.
- Chemical Resistance: In most chemical applications, HDPE pipes are very useful, as they work excellently in places that are in contact with various chemicals.
- Leak-Free Joints: The fused joints unite the pipe itself and create a joint-less structure that significantly prevents leakage, making maintenance activities easy.
- Eco-Friendly: HDPE pipes help in the construction of ideas because of their durability and the possibility of recycling.
Technical Parameters
- Pressure Ratings: HDPE pipes are offered with pressure ratings of about 4 to 25 bar or even higher, making them appropriate for various uses.
- Diameter Sizes: The standard diameter sizes range from 20mm to 1600mm, catering to both downscaling and upscaling of infrastructure.
- Temperature Tolerance: Most HDPE pipes are tested to withstand temperatures between -40 degrees Celsius and 60 degrees Celsius.
These pipes have been proven to be multifunctional and dependable, making them suitable for a number of industries, including water supply, gas distribution, and industrial operations.
Significance of Pipe Size in Various Applications
Pipe dimensions are one of the most critical factors that guarantee the improvement of the various applications in regard to their efficiency and effectiveness and influence the system’s performance and overall design. The following is a summary according to the best information sources:
- Water and Wastewater Systems: In these systems, the pipe diameter must increase to comfort the design flow rates and restrict the loss in head. Jumbo sizes are, therefore, mostly used on the main distribution pipes to achieve good water distribution over large areas.
- Gas Distribution: The parameters of gas pipelines must be measured correctly to hold the pressure during flows. Small pipes give rise to sudden pressure decreases, while large-diameter pipes are costly in materials and installation labor. So, their size is always selected so that both aspects are addressed satisfactorily in an economic sense.
- Industrial Processes: For industrial applications, the pipe size is dictated by the process variables in which different liquids or gaseous substances may be transported at an elevated ratio of pressure and temperature. Technical aspects such as wall thickness, pressure levels, and temperature values are important in evaluating safety and functionality.
Technical Parameters Justified:
- Pressure Ratings: Ensure the pipe can withstand the relevant pressure ranges needed for specific uses, such as 4 to 25 bars for HDPE pipes.
- Diameter Sizes: Choosing appropriate diameter sizes (20 mm to 1600 mm) related to the infrastructure and the medium that is being transported in consideration.
- Temperature Tolerance: Appreciating a pipe’s temperature tolerance (-40 degrees Celsius to 60 degrees Celsius for HDPE) is critical for long-term operational viability.
Rational pipe dimensions are essential for the general system design, helping to reduce costs, improve performance, and meet the requirements of relevant codes.
Common Applications of HDPE Pipes
The characteristics of HDPE pipes are so dynamic that they can be found in different working environments owing to their practicality. The top three applications commonly noted from leading sources include:
1. Underwater Piping Systems: HDPE pipes have been reported to be optimal in the transportation of potable water due to their high resistance to corrosion, flexible design, and durability. Their ability to handle a high amount of stress assures a fairly consistent supply of water without allowing much spillage.
Technical Specifications:
- Pressure Rating: These pipes are ordinary in the range of PN 6 to PN 16 and can be used for varying water demands.
- Size of Diameter: They often range between 20 mm and 1200 mm, but the size is determined by the particular system’s volume and flow rate.
2. Sewers and Waste Water: The great flexibility and strength of HDPE pipes help manage the sewage system and wastewater. These pipes are not limited to mechanical forces but have enhanced durability to chemical forces, which are essential in permanent structures buried underground.
Technical Specifications:
- Pressure Rating: Certainly, this would be parameter PN 4 to PN 10, subject to the courses and nature of the flows.
- Temperature Level: The watertight materials can endure at least 60 ° C to withstand wastewater with different heat effects.
3. Land Development & Drip Irrigation: Owing to their light weight and affordable construction cost, HDPE pipes have found great application in water conveyance systems for irrigation. They also assist in the proper application of water on expansive agricultural lands.
Technical Parameters:
- Pressure ratings: Normally, PN 6 to PN 10 are meant to suit the operational pressure of the irrigation systems.
- Diameter Sizes. With diameters ranging from 20 mm to 500 mm, we cater to various scales of agricultural activities.
Maintaining these technical parameters ensures the efficient, economical, and dependable performance of HDPE pipes in these critical applications.
How to Determine the Right HDPE Pipe Size?
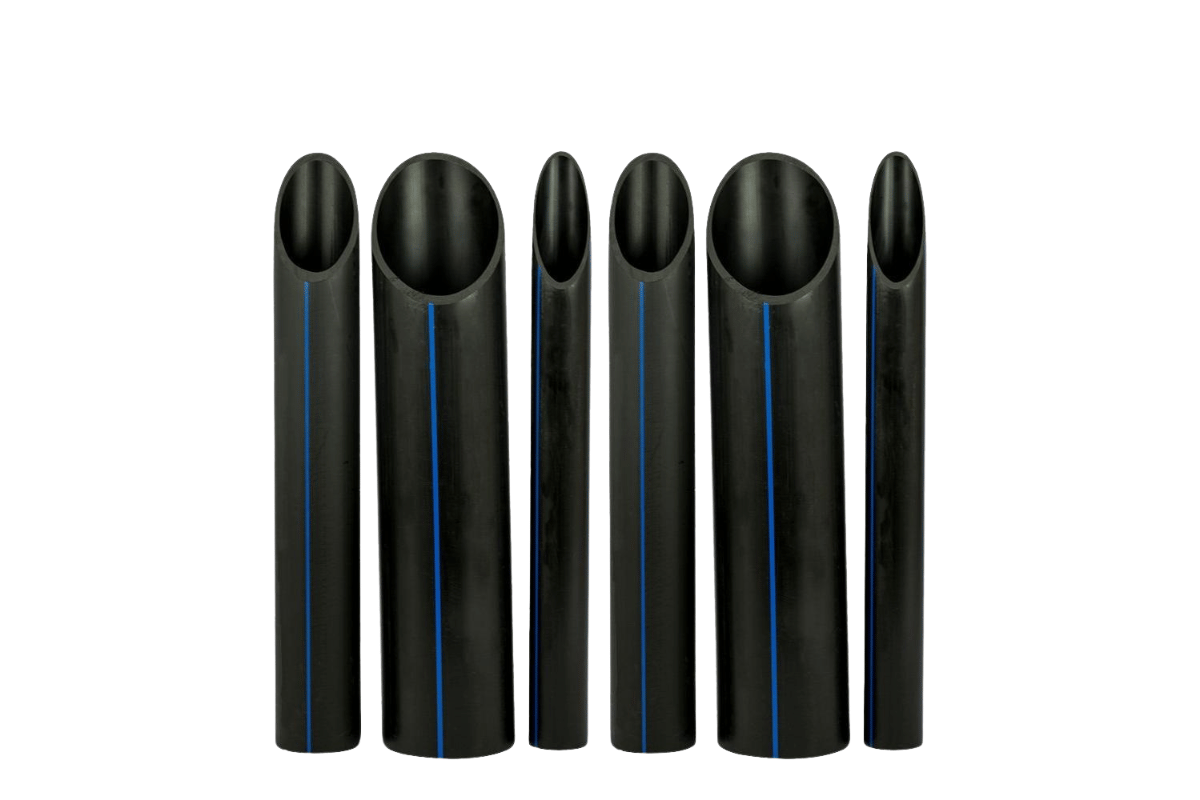
Selecting the appropriate size of a High-Density Polyethylene (HDPE) pipe is guided by some steps and factors to consider. First, identify the flow characteristics based on the possible use – water, gas or any other fluid. Secondly, utilize the charts for standard pipe flow, which relates the pipe size, volume flow rate, and pressure, and ensure it fulfills the criteria required on your system. In addition to that, think about the civil engineering pressure rating (PSI) that is changed by the thickness and diameter of the pipe to confirm that the pipe can bear the working conditions. Based on the standards developed by ASTM International or ISO, understand your case’s or geographical area’s compliance rules. Finally, seek the opinion of the manufacturers or experts in the field to ensure that the recommended size is appropriate for your purpose, especially when aspects such as altitude or pressure are complex variables in the system.
Factors to Consider When Choosing Pipe Dimensions
Selecting the optimal pipe sizes is not a straightforward process, and certain parameters must be considered to produce an efficient and effective pipe for use. Here are the factors that one should consider, as stated by some of the leading websites:
1. Flow Rate Requirements:
- Justification: The flow rate helps to determine the pipe diameter that should be offered to support that demand. Increases in flow rates require a given diameter to avoid pressure deficits.
- Technical Parameters: Include so GPM or L/s units are not so excessive that the selected pipe fails structurally.
2. Pressure Ratings:
- Justification: Pressure ratings are some of the factors that determine the tendency of the pipe to fail due to internal pressure containing CP slowly over time. Make sure you get a pipe with the correct long-term pressure ratings so that it does not burst or leak.
- Technical Parameters: The values should, however, not be lower than standard PN or PSI ratings, most of which are symmetrically designed for the systems. For example, dynamic inhalation pressure 10 is for moderately dynamic inhalation pressure systems.
3. Material Compatibility:
- Justification: Different materials tend to have different levels of strength, elasticity, and resistance to corrosive agents. The pipe material must be appropriate to the surroundings and the materials it would be transporting.
- Technical Parameters: Ensure that the material used will be compatible with certain chemicals or atmospheric conditions, meeting the standards outlined by ASTM or ISO.
Apart from the above factors, site-specific features such as environmental and regulatory aspects would significantly affect the selection of the appropriate pipe size for any specific project. Also, referenced materials and specialist recommendations contribute to compliance with industry norms and the efficiency of the work performed.
Understanding SDR and Its Impact on Pipe Size
The Standard Dimension Ratio, or SDR, is one of the most important parameters when sizing a pipe in most applications, including plastic piping. SDR determination is usually made by providing the ratio of active tube diameter over the wall thickness, which indicates the pipe’s strength that is diametrically pressurized. SDR makes it possible for any engineer to ascertain the reliability characteristics of a specific pipe at different parameters. This is because there are thicker pipe walls for a thicker pipe (low SDR number) and thinner pipe walls (high SDR number) for a given diameter strong enough to take high pressures. For instance, it can be said that SDR 11 is thicker than SDR 17; thus, it will withhold more pressure than the latter.
Such technical parameters as SDR involve the following points:
- Pressure Capacity Selector: This joint’s stress response consists of the SDR based on the system’s internal pressure. A high SDR ratio entails a low-pressure tolerance.
- Wall Thickness: This is very important since it basically determines the pipe’s resilience and bendiness to its surroundings. Having thicker or lower SDR walls confers Avast superiority.
- Applicable Areas: Different cases apply the same measures of SDR but different ranges of application pressure. For instance, standard SDR 26 is for use in less demanding sewer systems and SDR 9CT in high-pressure industrial applications.
When choosing the most suitable SDR, it is necessary to conduct a thorough evaluation of the pressure rating, the conditions of application, and the adherence to certain normative documents, including but not limited to ASTM and ISO standards. It is important to make sure that the right SDR is selected to ensure the quality, performance, and safety of the products.
The Role of OD and ID in HDPE Pipes
In the case of high-density polyethylene pipes (HDPEP), one of the outer diameter (OD) and inner diameter (ID) dimensions serves the most functional and applicable role of the pipe, in consideration of its performance and purpose, respectively. The OD, which is the outer view of the pipe dimension, is especially invariant even in a particular standard ratio of dimensions, ensuring smooth interfacing with a range of fittings and joints. Such a relationship assists in the factoring, which is critical when applying the pipe to how the construction materials or the pipe structure withstands external conditions.
The internal diameter, however, changes the thickness of the wall and SDR, as this is determined by calculating ID as OD minus two times the wall thickness. Closed loop circulation networks rely on such metrics on the ID as internal clearance is vital for flow calculations. Critical knowledge of the ID is essential in flow computation, in cases flow rates have to be observed to ensure the system operates under certain conditions.
Technical Parameters of OD and ID:
- Flow Capacity: The internal diameter of a pipe’s moisture movement capacity is at significant constraint/or is ambitiously present due to its liner capacity. The reason is The flow is crucial when speed and volume matter more in some applications.
- Pressure Rating: The pressure rating of an HDPE pipe is a function of the relationship between OD and wall thickness. Thin walls are detrimental to the service condition, which calls for systems that are thick-walled, hence allowing the application of high pressure.
- Fitting Compatibility: The OD facilitates the pipe’s conformity with standardized fittings, which is imperative for attaching to existing systems and structures.
Consequently, systematic examination of these parameters enables engineers and designers to choose appropriate HDPE pipes based on functional performance and operational safety for individual projects, thereby preserving efficacy and reliability in the system.
What are the Standard HDPE Pipe Sizes?
Different external diameters and wall thicknesses of standard HDPE pipes classify relevant size standard dimensional piping. Nominal pipe sizes (NPS) or diameter nominal values represent the most common standard dimensions. As per the familiar current top sources, the sizes also foster small diameter pipes more than ½ inch or more than 20 mm suitable for residential systems to large diameter pipes which can reach up to 63 inches or 1600 valuable mm for industrial and municipal purposes. The wall thickness, including the pressure rating, is decided by the Standing Dimension Ratio or SDR, with the ordinary SDR being SDR11 and SDR17, and the rest affecting the pipe’s pressure rating and not the OD. Manufacturers and standards organizations should provide more detailed sizing charts to enable a user to establish that the selected HDPE pipe satisfies your needs and the requirements of the projects.
Overview of Standard HDPE Pipe Sizes
By the consolidated content from the first three sources, here’s an answer concerning the size of standard HDPE pipe:
1. Nominal Pipe Size (NPS) and Diameter Nominal (DN): These are the parameters used to classify various types of HDPE pipes. Sizes are in inches or millimeters, where 20 mm = 1/2 inch and 1600 mm = 63 inches.
2. Wall Thickness and Pressure Ratings: The wall thickness of HDPE pipes is vital because it provides information on the pipe’s pressure rating and is usually described in terms of zero. Popular SDR values include SDR11 and SDR17. Large SDR values denote lower wall thickness, lower pressure ratings, and higher SDR ratios.
3. Justification of Technical Parameters:
- Outside Diameter (OD): This is for having corelative with standard fittings.
- Pressure Rating: Boundary line – SDR classification limits dictated by the application of a case.
- Material Type: Durable and flexible high density polythene is used.
To better satisfy the intended use of the particular pipe, especially in terms of dimensions and the pressure that the pipe can withstand, it is advisable to check the manufacturer’s detailed sizing charts. This ensures the proper use of the HDPE pipes for different project requirements, thus improving system efficiency and reliability.
Comparison of IPS Pipe Sizes
When these structures are measured in terms of pipe diameters called IPS, one has to scour the internet for the most authoritative sources to do this accurately. An IPS standpipe non-returning specifications include the nominal pipe size, outside diameter, and wall thickness. These are all essential features that relate to the given pipe strength and its use in fittings.
- Nominal Pipe Size (NPS): Partially straight-walled and full-encasement pipes NPS to HDPE HDPE pipes are provided with a series of sizes that conform to other existing ones. For instance, they vary from ¾ inches, which can be used for all purposes, to 24 inches, which is meant for industries.
- Outside Diameter (OD): NPS is different from general practice because it is based on the actual resistance to internal volume, which is achieved by another value, the OD of the pipe. For instance, a nominal 2-inch NPS pipe will, on average, have an OD of 2.375. The OD of a pipe is an important aspect for determining the fittings and joints it is subjected to.
- Wall Thickness and SDR: A pipe’s pressure rating usually depends on the wall dimension, which has its counterpart called the Standard Dimension Ratio (SDR). There are standard discs and values, for example, SDR11 and SDR17, that enable actual pipes to exceed a given maximum pressure. For example, tubular pipes can have a very thick wall at an 11SDR pipe than when they have a 17SDR pipe of equal outside diameter.
Taking these parameters into account, engineers can choose an IPS HDPE pipe size that is adequate for the project’s specific needs and appropriate in terms of structural reliability and performance. It would be ideal to cross-reference such detailed sizing guides with those available on manufacturer’s sites or any other applicable industry guideline.
Explanation of Nominal and Actual Diameter
I see that nominal diameter refers to a dimension that is also referred to as the approximate internal diameter of a given pipe but does not exactly measure the dimensions of a given pipe. This sizing system provides less complexity in the systemic classification of pipes to enhance the inter-compatibility of fittings and systems of different manufacturers.
On the other hand, an actual diameter refers to a more refined measurement that includes the pipe’s outside diameter (OD). However, such a dimension (nominal diameter) remains the same, while the wall thickness and so on may influence the actual internal diameter. Some key design features are: Short but relevant editing information is always available.
- Nominal Diameter (NPS): For example, it can be part of the diameter over which the pipe’s internal surface extends, transporting the non-abrasive medium.
- Outside Diameter (OD): This is the outside diameter of the pipe, which is measured and poses a great risk when the right fitting is fitted onto the pipe.
- Wall Thickness: This value will depend on the particular Standard Dimension Ratio (SDR) employed for the pipe and will dictate the amount of pressure that the pipe can withstand.
These parameters help maintain the uniformity of specifications and the quality of pipes used in engineering works. However, it should be emphasized that these parameters must be checked against particular requirements to satisfy the application in question.
How to Use an HDPE Pipe Size Chart?
To benefit from the HDPE pipe size chart, it’s advisable to begin by determining the external dimension (OD) and the standard dimension ratio (SDR) suitable for the project’s needs. The chart’s measurements typically list the nominal pipe size plus the external and internal diameters to help evaluate the pipe’s pressure and usability. Compare the chart of the relevant pipes with the system you are using and the plumbing pressure information and temperature/ fluid used in the system. It’s also essential that the selected sizes fit into the established codes of good practice among different regions or countries if there are any. Customer service departments usually provide detailed directions on how to improve the pipe application to meet a customer’s needs. Always periodically check the most recent information from reputable industry players to avoid outdated information.
Reading and Interpreting Size Charts
In reviewing and deciphering HDPE pipe size charts, there are critical technical parameters that have to be paid attention to to make the right choice:
- Nominal Pipe Size (NPS): This dimension represents the approximate pipe diameter in all the pipe schedules, a dimension critical to understanding the pipe’s flow.
- Outside Diameter (OD): As mentioned above, the outside diameter assists in determining the design of the pipe’s connection with the other piping components or system.
- Wall Thickness: This essential dimension is the Standard Dimension Ratio (SDR). It is utilized to predict the pressure rating of the pipe in question. An increase in wall thickness is likely to increase the pressure capacity.
To facilitate the appropriate use of these specific charts, it is prudent to seek the latest materials, including:
- Manufacturer Websites: In most cases, these contain explicit size charts indicating specific O.D. and wall thickness for fabrication.
- Industry Standards Sites: For example, ASTM International or ISO websites are full of valuable information regarding standardization since compliance is essential.
- Construction and Engineering Forums: These may also provide practical information and user feedback on selecting the correct and suitable HDPE pipes.
The comparison techniques allow users to defend their choice of pipes against any engineering constraints relative to their projects, thus safeguarding compatibility and efficiency. In any case, relationships should be maintained even at the lowest level, ensuring that the chosen pipe conforms to the geographic norms and peculiarities of the project in relation to its performance and the integrity of the system.
Standard Range of Pipe Sizes and Their Uses
When selecting a pipe for a given project, knowing the standard range of pipe sizes and what they are used for is essential. The following quotes explain how different pipe sizes are manufactured for various uses:
- 1/2 inch to 2 inches: The small pipes are often used in residences to water the family’s kitchens, showers, or toilets. This thin pipe can easily be concealed inside walls and floors.
- 2 inches to 6 inches: These medium pipes are more often found in commercial structures that require high-flow water systems, such as office and industrial buildings. They are also used in drain-waste-vent systems.
- 6 Inches and above: These pipes are preferably used in infrastructural works such as water mains, sewer lines, and heavy industries. They can transport vast quantities of water and hold high pressure.
In line with this, standard measures deriving from technical parameters ought to be considered, such as the Nominal Pipe Size (NPS) and Schedule that specifies the strength and pressure rating of the particular pipe. Lastly, caution should be taken to ensure that all the selected sizes conform to some of the industry standards offered by bodies such as ASTM and ISO to enhance the system’s efficacy.
Examples of PE4710 Pipe Sizes
As a result, PE4710 pipes are popular in many applications due to their high strength and good durability. Standard sizes and corresponding uses include:
- 4 inches to 12 inches: Such sizes are applicable and installed throughout the industrial and municipal water systems and are well within the flow rate and pressure range. Its technical parameters of the most standard dimensions are up to 100 PSI, which could be applied for the lower range up of a certain level.
- 12 inches to 24 inches: These are the great diameter pipes that are used in civil construction, for instance, water distribution systems or sewage systems. They can accommodate larger flow rates with a normal pressure rating of 125 psi and above, depending on application and wall thickness.
- 24 inches and above: These sizes are found in industrial applications or big municipal systems and are used for the highest flows and pressures. The rating of such pipes may reach 160 psi, and they are mostly useful in demanding places that need high levels of operation and reliability.
Such pipes shall also be manufactured in accordance with both ASTM F714 and ISO 4427, meaning that they should be subject to tougher performance and safety requirements. Some of the factors to consider when choosing the pipes include the material grade, applicable pipe pressure rate, installation environment, etc., to prevent selection system failure.
What are the Applications of Different Pipe Dimensions?
Applications of other HDPE pipe dimensions are determined by the size of the pipe and its pressure rating as well. Small-diameter pipes, which are predominantly used in domestic plumbing and irrigation systems, find application in low to medium-pressure applications involving the transportation of water. Medium-sized pipes find applications in municipal water systems, agriculture, and mining, where the demand for strength and flexibility increases as pressure intensifies. Further, bigger pipes are produced to help in industrial projects that include sewer systems, land drainages, and water mains. These types of pipes are built to take in high volumes of flow and high pressures, creating a credible reliance for ample water and waste systems. There is no per pipe dimension type without a specification regarding either type of fluid to be transported, the pressure within the pipe, or the conditions faced by the pipe, and this is in line with the bonding picture of placing liquids within the pipes.
Specific Applications for Various Dimensions
When it comes to the specific applications of the various sizes and dimensions of HDPE pipe, views extracted from some of the leading sources subject the pipes to different usages depending on the technical properties and dimensions of the pipe:
- Residential and Commercial Plumbing– There is frequent usage of small-sized HDPE pipes of between ½ inches to as large as 2 inches in residential and commercial plumbing. These pipes are suitable for drinking water and have working pressures of up to 125 psi, which is useful for applications that do not have high-pressure demand.
- Agriculture and Industrial Irrigation—Medium-size pipes, ranging between 3 inches and 6 inches, are commonly used in agricultural and industrial irrigation. These pipes are free and reliable in terms of pressure flexibilities from 100 psi to 150 psi, enabling them to be used in more than one type of terrain and working conditions.
- Municipal Water systems and Sewage transport—Large diameter pipes, 8 inches and above, are used in municipal water systems and for sewage transportation. Most of them are built to withstand pressures in excess of 160 psi. Hence, they are used for applications that require high volume and high-pressure pumping.
Due consideration has been given to each application’s environmental conditions and technical parameters to meet the requirements of ASTM F714 and ISO 4427. This alignment permits safe, effective, and sustainable actions in all applications.
Choosing the Appropriate Pipe for Potable Water Distribution
Failure to focus on specific technical aspects in selecting HDPE pipes for drinking water purposes can be a costly negotiation. According to the main sources on the subject, the most significant factors are the pipe’s physical dimensions, working parameters, and target scope.
- Diameter and Flow Capacity: The pipe diameter to be selected should relate to the expected water consumption. Small diameter types ranging from ½ to 2 inches in pipes are sufficient for individual houses. In comparison, more significant diameter types sizing from 3 inches to 6 inches are appropriate for commercial/ multifamily residential systems.
- Pressure Rating determines the limit of the pipe’s pressure-bearing capacity, which is crucial in retaining enough pressure to reach different volumes of water in the system. In most residential and commercial potable water systems, the most widely recommended pressure rating is often between 100 and 150 psi.
- Material and Compliance: The pipe material should align with health and safety standards such as NSF/ ANSI 61 for drinking water systems. Many guidelines have been developed, and HDPE Pipes remain to incorporate due to their corrosion resistance strength rating specifically for clean water use.
These technical parameters are important in ensuring that potable water distribution is done safely, efficiently, and up to the required standards, guaranteeing the safe distribution of water.
Considerations for High-Pressure Applications
In applications characterized by high pressure, selecting appropriate HDPE pipes requires careful consideration of specific parameters. Some of the essential contributions reported by leading experts in the industry are:
- Higher Pressure Ratings: In high-pressure systems, the specifications of HDPE pipes can be expected to be way above normal. That is, an index of 150 to 200 psi or higher, depending on the system’s requirements for such applications.
- Wall Thickness and SDR: Standard Dimension Ratio: to enable the pipelines to withstand higher pressure, more walls’ depth must be introduced. Concerning the pressure requirement, the SDR of the pipe, which is the pipe-to-wall thickness ratio, has to be appropriate. Lower SDR (thicker wall) is higher in case of high pressures than here.
- Stress Crack Resistance: Stress cracking is another serious limitation of any material since intermittent surges in pressure can damage the pipes. Therefore, the material has to have a good resistance to stress cracking. Better stress crack resistance enhancement enhances the reliability of the materials under high pressures.
- Temperature Considerations: As such, HDPE pipes in high-stress systems may also be used in conditions of extreme temperature variations that otherwise affect usable pressure. Heat-resilient materials would be more useful in such cases to prevent failure due to temperature and time degradation.
The technical parameters mentioned above are vital in safety, efficacy, and compliance for implementing HDPE pipes under high-pressure systems, delivering excellent performance in transmitting water or other fluids under stress.
Frequently Asked Questions (FAQs)
Q1: What factors influence the lifespan of HDPE pipes in high-pressure applications?
A1: The lifespan of HDPE pipes in high-pressure applications is influenced by pressure rating, wall thickness, stress crack resistance, and temperature fluctuations. Selecting pipes with appropriate specifications and regular maintenance can significantly extend their service life.
Q2: Can HDPE pipes be used for transporting chemicals or hazardous fluids?
A2: Yes, HDPE pipes can be used for transporting various chemicals or hazardous fluids, but ensuring that the pipe material is compatible with the specific chemicals is crucial. It is advisable to consult with the manufacturer and consider chemical resistance ratings.
Q3: How do I determine the appropriate pressure rating for my HDPE pipe system?
A3: The appropriate pressure rating can be determined based on the system’s operational requirements, including maximum expected pressure, potential pressure surges, and the transported fluid. Consulting engineering guidelines or a professional can provide insights in accurately assessing these parameters.
Q4: Is there a difference between HDPE pipe installations in hot climates compared to cold temperatures?
A4: Yes, installation practices may vary depending on the climate. In hot climates, considerations for possible expansion and the selection of heat-resistant pipes are essential, while in cold climates, it is important to ensure pipes can withstand freezing temperatures without compromising their structural integrity.
Q5: What maintenance practices are recommended for HDPE pipes in high-pressure systems?
A5: Recommended maintenance practices include regular inspections for leaks or damage, pressure monitoring, ensuring connections and joints remain secure, and routine cleaning to prevent blockage or contamination. Following a comprehensive maintenance schedule helps sustain system performance and prevent failures.