High-density polyethylene (HDPE) pipes have gained an establishment in modern construction activities and fluid transportation due to their structural qualities, such as strength, flexibility, and anti-corrosion properties. This blog will help you understand the details related to 8-inch HDPE pipes, which include their dimensions, advantages, and uses in water supply, gas distribution, and sewage systems. Certain readers may be particularly interested in more practical issues, including the pressure, temperature, and installation of 8-inch pipes. It is our aim to assist professionals and interested members of the public in making appropriate choices related to the pipes and their specifications used in carrying out various activities. Through research and varied presentations, users will appreciate the course of action taken in regard to HDPE materials instead of traditional materials in piping system applications.
What is an 8-inch HDPE pipe?
The term 8-inch HDPE pipe pertains to a pipe made of high-density polyethylene and has an outside diameter of about 8 inches. It is engineered for high-performance and durability, featuring high impact strength, low thermal conductivity, as well as high chemical and abrasion resistance. Despite their strength, HDPE pipes are lightweight which enables them to be used in a wide range of applications such as potable water supply, drainage and sewerage systems, and gas pipes. Because of their flexibility, they can be quickly installed over a wide range of contours and reduce the joints and fittings required to shorten the installation period and potentially leak points.
Understanding pipe materials
My exposure to the industry market shows that of many polymers used for pipeline construction, high-density polyethylene is the one consisting of most properties required in the contemporary infrastructural reality. HDPE pipes are not prone to rust and corrosion as opposed to metallic pipes hence increasing their durability. Thermal wastage is also less as its thermal conductivity is very low. This characteristic is important in any fluid transport system. In addition, high-density polyethylene is highly flexible, which is critical when installation is required in challenging terrains. Such flexibility also helps to reduce the risk of fracture due to framework movement and helps in easy installation. When compared to other polymer materials, high-density polyethylene has many advantages in terms of strength and adaptability in piping systems.
Key features of polyethylene in pipes
I would like here to get into the particulars that make polyethylene, more specifically HDPE pipes, such a unique material for numerous end uses.
1. Durability: Polyethylene pipes are extremely durable. They are able to withstand high impact as well as pressure without cracking, which is important in places where strength is a requirement.
- Corrosion Resistance: Polyethylene pipes are extremely durable. They are able to withstand high impact as well as pressure without cracking, which is important in places where strength is a requirement.
- Flexibility: Polyethylene pipes are extremely durable. They are able to withstand high impact as well as pressure without cracking, which is important in places where strength is a requirement.
- Lightweight Nature: Polyethylene pipes are extremely durable. They are able to withstand high impact as well as pressure without cracking, which is important in places where strength is a requirement.
- Chemical Resistance: Polyethylene pipes are extremely durable. They are able to withstand high impact as well as pressure without cracking, which is important in places where strength is a requirement.
- Thermal Properties: Polyethylene pipes are extremely durable. They are able to withstand high impact as well as pressure without cracking, which is important in places where strength is a requirement.
From the consideration of the aforementioned features, it is understandable why HDPE pipes are becoming popular choices for modern construction projects. They are strong, durable, and flexible – all essential characteristics of a good piping solution.
Applications of HDPE Pipe
I would like to present the different uses of HDPE pipes in different fields, showing the rationale behind this preference for the material.
- Water Supply Systems: HDPE pipes are among the most used polymers in municipal and rural water supply systems. Because of their corrosion-free properties, potable water will be transported without jeopardizing its quality. Also, because of their lightweight and flexible nature, their use makes installation easier and inexpensive.
- Gas Distribution: For gas distribution networks, there cannot be a more suitable pipes than HDPE pipes because of their robustness and leak proof attributes. They are able to handle great fluctuations in pressure and are insensitive to environmental stress cracking, therefore a dependable supply of natural or synthetic gases is assured.
- Sewage and Wastewater Management: HDPE pipes stand out in sewage systems because of their chemical resistance and rough flow handling. These pipes provide a long-term strategy with regards to waste transportation as they are free from deterioration breakage, thus serving an efficient waste in urban and industrial industries.
- Agricultural Irrigation: In agricultural irrigation systems, the use of HDPE pipes are appropriate because of their resistance to chemicals and fertilizers. They are able to provide efficient water conveyance system under different climates thus, promoting better sustainable agricultural systems.
- Industrial Applications: The use of HDPE pipes in different industries can also be attributed to the transportation of syntactic slurries, chemicals and compressed air. Their high strength and ability to resist wide variety of chemicals makes them a perfect fit for these applications.
- Mining: In the mining sector, HDPE pipes are used for slurry lines and other high-pressure applications. Their resistance to abrasion, as well as their flexibility, makes them effective in harsh mining conditions.
Corrosion resistance, flexibility, lightweight, and chemical resistance are attributes that allow the applications of HDPE pipe to remain reliable and useful in various applications and, thus, increase their efficiency.
How to Choose the Right HDPE Pipe Size?
When sizing a particular type of pipe, in this case, HDPE, there are a number of important factors that need to be assessed for success. To begin, the flow rate requirements of the system should be determined, as that would determine the pipe diameter capable of carrying liquids without pressure losses or restrictions. For the second step, pressure ratings should be examined in order to see whether it is possible to sustain the operating pressure pertinent to the relevant application without issues of failure or leakage. This also impacts the material and the size of the pipe, account the nature of the fluid with regard to viscosity, temperature, and other features. The last consideration would be the installation environment, where such features as conditions of the ground, distance of the pipe from the source, and other physical pressures should inform the final decision on size. Having a clear appreciation of such factors, one should be in a position to select the most appropriate size of an HDPE pipe that addresses the concerns of a specific use.
Determining the right diameter
It may look like a challenging task to size an HDPE pipe diameter properly, but it is essentially a function of a few specific things. To begin with, let’s talk about the flow rate. It tells us the volume of liquid which you will be passing through the pipe and, therefore, the size which will be required. As the flow rate increases, the pipe diameter also has to be increased in order to accommodate the flow rate without creating any blockages. Now, the next factor considers pressure requirements. You would want the pipe to withstand the pressure of the system so it will not develop bursts or leaks. This is the point where it is useful to know what the working pressure of your system is when deciding on the diameter.
The other important factor is the fluid, its viscosity, temperature, and even chemical properties will all affect considerations of pipe sizing. For tighten and more viscous fluids, it is generally the case that the pipe diameter has to be larger than normal in order that smooth flow can be achieved. Also, don’t forget the installation environment: The length of the pipeline, terrain irregularities, and exposure to environmental conditions such as UV or chemicals are also elements that should not be neglected.
Considerando estos parámetros: caudal, presión requerida, tipo de fluido y factores ambientales, se puede tomar una buena decisión en lo que se refiere al diámetro de la tubería de HDPE, logrando un sistema eficiente y confiable.
Importance of Pipe Specifications
It is of pivotal importance to comprehend and comply with certain requirements concerning the pipes when installing HDPE pipes for any application. These requirements guarantee that the pipe will be suitable for its intended purpose while also providing performance and safety assurances. The following are some important specifications which should be taken into account:
- Pressure Rating (PN Rating): This indicates what level of pressure the pipe can bear without breaking. All pressure ratings are absolute in nature, relative to the thickness and diameter of the pipe, and are assigned as Pressure Nominal, or PN values. PN rating is vital in high pressure systems in order to prevent failure of the systems.
- Diameter and Wall Thickness: These parameters determine the flow rates and pressure tolerances of the pipe. The spherical ratio or SDR links the outer diameter and thickness, which governs the pressure rating and general mechanical characteristics of the pipe.
- Material Grade and Density: The material for HDPE pipes may include various grades, each having specific properties relating to mechanical strength, as well as an ability to withstand certain chemicals. Higher-density grades are generally considered to be stiffer and able to withstand greater pressure, which is exactly what is needed in a harsh
- Temperature Rating: Knowledge of the temperature range of operation of the pipe is essential for use of the pipe at extremely hot or extremely cold temperatures. This ensures that the material will not yield, and that there will not be any material failure that results from thermal stress.
- Chemical Resistance: It is necessary to choose pipes which have that chemical resistance which they may be exposed to, particularly in the industry or sewage, so that the service life and performance of the pipe is not compromised.
- Jointing and Fitting Compatibility:Issues of joint and fitting compatibility have to be addressed to ensure the integrity of the system being used. It is possible to specify the joint fittings adequately which minimizes the likelihood of leakages and increases the longevity of the system.
Complying with these specifications improves the performance of HDPE piping systems, increases their service life and reliability as well as improves the safety and efficiency of the entire infrastructure project.
Factors Affecting Pipe Selection
When I am selecting an HDPE pipe for my projects, I emphasize a number of factors so as to assure appropriateness as well as efficiency. The most critically important would be the flow rate requirements, as any error in this would create excess strain on the system, which translates into waste or breakdown of the system. I undertake the task of precisely forecasting the amount of fluid that is likely to be transmitted so that the suitable smooth bore is able to permit its movement.
Another aspect that I pay attention to are the pressure ratings of the pipes. In matters of pressure assessments, I make sure that the pipe is well suited to withstand operational stress and strains without becoming structurally stressed. I use these norm values when matching the PN rating with the requisites of the system.
Considering the fluid type is also of paramount importance, its viscosity, temperature, and chemical properties may act as a detriment to the pipe material. In order for the pipes to withstand aggressive fluids, I select the pipe material appropriately, thus ensuring chemical compatibility and pipe durability throughout its predicted life span.
Evaluating the installation environment is also on my checklist. From geographical surveys to weather patterns, I collect as much information as possible to establish how the surrounding environment would affect the pipe. For instance, if the pipeline cuts across rough terrain, then adequate levels of flexibility and pressure resistance would be incorporated to cater to internal and external stresses that would otherwise cause failure.
Through a detailed examination of these factors, I optimize the reliability and system efficiency during the selection of the HDPE pipes in my engineering design, thereby establishing a focus on the structural support systems.
What Are the Specifications of 8-Inch HDPE Pipe?
Specifications of 8 Inch HDPE Pipe
I can state that the specifications of the 8-inch HDPE pipe encompass a few essential features that allow it to function and last. The outer diameter of this pipe, for instance, is 8.625 inches (or 219 mm), allowing different flow rates and pressure requirements to be met. The wall thickness is dependent on the Standard Dimension Ratio (SDR) whereby an SDR 11 pipe will have what can be considered a thicker wall as compared to an SDR 17 which will allow for greater pressure to be held.
The pressure rating is important and for instance an 8 inch pipe, this ranges generally depending on the SDR the lower the SDR the higher the of capacity……The pressure rating is generally pressure rating is generally pressure rating is the number that designates the maximum working pressure the pipe can withstand without failure which for an 8 inch HDPE PEX shrub can see up to 20 atm.
You can say the material grade for this PE4710 high density polyethylene pipe grade; this has high density and better chemical resistance, this grade is important for extended durability in a range of applications. Pe plastic pipes suitable for the temperature range of -40f to 140f, are maintained, but engineers might have a need to accommodate a few extreme circumstances.
Lastly, the compatibility of fittings and jointing is standardized with a range of options such as butt fusion, electrofusion, and mechanical joints, all of which have good resistance to anticipated leakage. On the whole, the specifications suitable for applications of the 8-inch diameter HDPE pipe are water supply and gas distribution, as well as the disposal of industrial waste.
Technical specification overview
You are a professional in the field, so what important parameters, or characteristics, define the operational features and the range of applications for an 8 inch HDPE pipe? Permit me to elucidate.
- Outer Diameter: This external diameter measurement is usually nearly 8.625 inches or 219 mm . This is very important as it determines the entire capacity of the pipe towards the flow of fluids as well as how it is connected to the rest of the system.
- Wall Thickness and SDR: The wall thickens, however, is as a result of the Standard Dimension Ratio (SDR) which is the outer diameter of the pipe divided by its thickness. To illustrate, a pipe with an SDR of 11 would have a thicker wall than one with an SDR of 17, and therefore, is able to withstand greater pressure and last longer.
- Pressure Rating: The pressure ratings of the pipe in most cases ranges between PN 6 which is approximately 150psi and PN 20 which is about 300psi depending on the SDR. The pressure rating shows the amount of pressure that can be exerted on the pipe without bursting.
- Material Grade: Most material grades like PE4710 have high density and durability and chemical resistant material. This is important in ensuring that the pipe lasts in a place where it is likely exposed to a number of chemicals and other forms of external abuse.
- Temperature Tolerance: For most of these pipes, shooting the operational temperature even between -40 °F to 140 °F is manageable allowing ease of operation in various environmental settings.
- Jointing and Fitting Compatibility: The 8-inch HDPE pipes can effectively be joined by several means, which include butt fusion, electrofusion as well as mechanical joints. Each of these methods provides strong and tight connections which are necessary for the system to work effectively.
You can definitely stick to a dependable infrastructure setup for any application by putting into consideration these parameters in evaluating the effectiveness of an 8 inch HDPE pipe for the task at hand.
Pressure Ratings and Usage
I will explain the pressure ratings in relation to the application of 8-inch HDPE pipes in easier terms. Let’s take it one step at a time:
- Pressure Rating Explained: To start with let’s explain what Pressure rating is. It is the maximum pressure a pipe is allowed to sustain safely. With 8-inch HDPE pipes, pressure rating may differ and is lactated in different classes, for instance, PN (for pressure nominal), which is followed by a distinguished number indicating a level of pressure sustained in standard measuring units, which are most likely psi, American Measure of Pressure meaning Pounds per Square Inch.
- Relationship to SDR: It has been noted that pressure rating is directly proportional to the Standard Dimension Ratio (SDR) of the pipe. This is expressed as the ratio of the outer diameter of the pipe relative to the wall(height) of the pipe. The lower the SDR, the thicker the walls, which, in most cases, gives the pipe the ability to withstand high pressure. An example of a pipe SDR 11 and 17 shows that SDR 11 can withstand more pressure than SDR 17.
- Typical Pressure Ranges: As a standard setting where American HDPE Piping Sytem is used, an 8-inch PN 20 HDPE pipe possesses pressure ratings more than PN 6, which is approximately 150 psi, and PN 20, which is around 300 psi. The versatility in registration also enables the pipe to be employed in different areas, including water and gas provision and more industrial procedures that place higher demand on the pressure ratings of the pipe.Rather, the application of plastic pipes is governed by pressure and demand. For high-pressure applications such as industrial systems or long-distance urban water supply systems, pipes with a higher pressure rating are recommended. On the other hand, more typical applications, such as the distribution of water in ordinary houses, will use lower pressure-rated pipes.
Grasping these parameters helps you choose the most appropriate pipe specifications for your project regarding efficiency and safety.
Compliance with Industry Standards
It is essential that certain industrial standards are met when choosing an 8-inch HDPE pipe. The standards listed below give specific requirements and recommendations that ensure quality, serve safety and performance functions:
- ASTM F714 – Standard Specification for Polyethylene (PE) Plastic Pipe (SDR-PR):
- Details: This standard is critical for the size and tolerance defense of HDPE pipes. It encompasses the specifications for materials, marking and tests needed to ensure that the pipe is stress bearing.
- Compliance Data: All pipes conforming to ASTM F714 are guaranteed to undergo hydrostatic testing to ensure disruption-free structure under stated conditions.
- AWWA C906 – Polyethylene (PE) Pressure Pipe and Fittings:
- Details: Specifies the pipe stiffness and the structural and mechanical integrity of PE pipes that are placed in use for the construction of water and wastewater systems. This standard guarantees the capacity of the pipes to deal with different environmental conditions.
- Compliance Data: Compliance with AWWA C906 indicates the capacity of the pipe to convey drinkable water and recover from ultra-violet and chemical assault.
- ISO 4427 – Polyethylene Pipes for Water Supply:
- Details: This international standard contains the specifications that must be fulfilled when using PE pipes which are meant for water supply. TheService is about durability, safety, and installation.
- Compliance Data: This compliance with ISO 4427 means that, the pipe has undergone all stringent tests regarding environmental as well as operational efficiency and has passed.
- NSF/ANSI 14 – Plastics Piping System Components and Related Materials:
- Details: Sets out the physical and performance specifications of the piping system and its materials. It guarantees safe piping for drinking water use in plumbing installations.
- Compliance Data: Pipes compliant with NSF/ANSI 14 specifications have been evaluated for functions, the safety of material used, and inscriptions in accordance with health effects’ regulation of the supply of potable water – the requirements pertaining to the supply of safe drinking water.
If your 8 inch HDPE pipes meet the aforementioned industry standards, chances are that they are structurally sound and useful for their intended purposes thereby enhancing the integrity of safe and functional infrastructural systems.
Where Can 8-Inch HDPE Pipe Be Used?
I can say with confidence that 8-inch HDPE pipes have a variety of applications because of their toughness, resistance to chemicals, and elastic properties. These types of pipes are commonly used in municipal water and sewage systems due to their ability to withstand high dynamic pressures and aggressive media. They are also used in industry for the transportation of chemicals and gases where resistance to a large number of substances is a necessity. Apart from these, HDPE pipes are also used in agricultural irrigation, ensuring the seamless water supply necessary for crop irrigation. Their characteristics enable them to be used in geothermal piping and telecom structures where factors like longevity and resistance to external forces are essential. Therefore, the strong and flexible properties of 8-inch HDPE pipes enable their use in various industries, contributing to the operations’ efficiency and sustainability.
Applications in water supply systems
I wish to outline the features of an 8-inch HDPE pipe and its utilization in a water supply, as well as its appropriateness for this purpose, considering her experience in the industry.
These pipes are chosen on the base of their strength. In water supply, this means less repairs and maintenance cost because less number of failures will be experienced. Most materials will suffer from some form of deterioration HDPE pipes on the other hand can last without losing their functional capabilities to serve water systems for many years into the future.
Next, an important parameter is their relative chemical resistance . They do not support many of the chemicals used in water supply systems like chlorine and many alkaline substances. This resistance can make corrosion less likely and hence water delivered can be safe and clean.
Next big contributing factor is their flexibility. The reason as to why the HDPE pipes can be broken is due to the fact that it is able to endure a range of stress levels as well as movement of the ground including earthquakes or settlement of soil. This ensures that in areas with seismic activity, those pipes can provide a reliable option.
Other than the above factors, cost effectiveness is also another factor of the importance. For installation purposes, because they are lightweight and longer, there are fewer joints which save time on installation. This directly cuts on labor costs that would have otherwise been incurred in the endeavors of the projects and also limits potential leak points in the pipes.
Ultimately, their smooth internal surface helps keep the friction loss to a minimum while also allowing them to maintain steady flow capacity, which is very good. This allows for efficient water delivery even when high flow rates are employed, which is vital to improving the operational efficiency of the water supply system.
It can be inferred from the observations of these parameters that it is very optimal to use 8 inch HDPE pipes in water supply systems as they combine practical use, reliability and efficiency.
Role in Drainage Pipe Solutions
I would like to briefly analyze the reasons why 8-inch HDPE pipes are successfully used in drainage systems. Let’s examine the basic parameters that make these pipes suitable for such applications:
- Durability and Longevity: The HDPE pipes are made for the long term as they do not require frequent maintenance or replacement. This comes in handy for drainage applications that involve dealing with water and the elements on a constant basis.
- Chemical Resistance: Drainage systems often drain used and dirty water that may have chemical pollutants. Such chemicals are repelled by HDPE pipes, thus averting any corrosion or degradation. This makes it possible for the drainage system to be sound and operational over an extended period.
- Flexibility and Toughness: These pipes can withstand bending without breaking, an important characteristic when meeting the requirements of ground movement or shifting loads. The structural feature of flexibility makes it possible to use the pipes in cases of shifting soil or settling.
- Ease of Installation: Due to their lower weight and larger length, they are much faster and simpler to install in comparison with heavy pipes which have short lengths. As a result, this improves construction work, and decreases the labor hours and expenses.
- Smooth Inner Surface: The HDPE pipes have a thin wall which reduces the overall friction and thus enhances the movement of water. In drainage systems, this feature is crucial to prevent clogging of systems and promote rapid drainage of water.
It can be concluded that the mounting features of the 8 inch HDPE pipes make them reliable and efficient for drainage systems as they can cope with the harsh conditions in the environment and function optimally.
Usage in Mining Operations
so let me tell you why 8-inch HDPE pipes are widely employed in mining operations. Let us now consider the pertinent parameters that warrant their applicability in such extreme conditions:
- Durability and High Strength: The pipes used in mining have face wear and tear from rough elements combined with high compressive forces. Such issues are overruled owing to the high strength and toughness of the HDPE pipes, which enable the application of these pipes without the fear of them shattering or wearing out, even when subjected to high pressure.
- Chemical Resistance:Chemicals are handled during mining activity which can rust or corrode other lower grade materials. This ability of the HDPE pipes to resist a multitude of chemicals provides impermeability avoiding failure of the pipe as well as protecting the materials being transported.
- Flexibility: The mining site may be active, with many changes being seen on the ground over short spans of time. The relative flexibility of the HDPE is vital to remain intact as the pipes are bent during installation and subsequent movements of the surface or underground.
- Resilience to Wear and Tear: The continuous flow of slurry, water, and other fluids in mining can cause damage to pipes. Such wear and tear is markedly reduced for the HDPE pipes; thus, the frequency of replacement and subsequent repairs are reduced.
- Ease of Transportation and Installation: The installation of pipes, and the transportation of pipes can be a tough task in remote mining locations. HDPE pipes help in minimizing logistics challenges and installation duration owing to their comparatively light weight combined with availability in different lengths.
- Smooth Interior Surface: Another favorable modification is the presence of a smooth inner surface which decreases friction and thus avoids energy losses during the functioning and pumping of liquids. Such efficiency is relevant for mass-scale operations in mining, where the output is seriously affected by frictionsal losses.
By dealing with these factors, it is clear that 8” HDPE pipes are, in fact, capable of withstanding the harshness of mining activities while improving the efficacy and cost-effectiveness of the processes.
How to Install and Maintain Polyethylene Pipe?
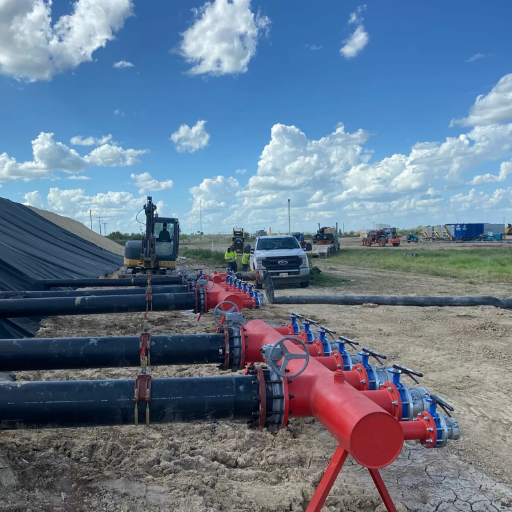
Effective installation and maintenance of polyethylene pipes begin with the conduct of a site survey so as to evaluate whether the characteristics of the site, such as the type of soil or climatic condition, are suited for the installation of polyethylene pipes. The range of work involved in the installation procedure includes trenching, bedding, laying, and backfilling. Trench width and depth should be sufficient to provide space for the thermal movement of the pipe and to avoid any external overburden damage to the pipe. Use suitable methods of securing joints, such as butt or electrofusion, to make all connections leak-free. In relation to maintenance, simple blockages, leaks, or any form of mechanical damage from the environment should be conducted on a periodic basis. When applicable, use such systems to remotely evaluate the condition of the pipes. Disposable repairs should be carried out swiftly and appropriately to ensure that the expected efficiency of the system is not compromised. Orienting oneself with recent developments in the field is advised in order to ensure more longevity and efficiency in the performance of polyethylene pipe systems.
Installation Techniques and Tips
I strive to ensure accuracy and industry best practice compliance when installing polyethylene pipes. To begin with, an adequate site assessment, including soil grade and likely installed pipe location, is paramount. While trenching, there is a requirement that a trench is sufficiently deep and wide so that the pipe does not experience stress during movement. There are also appropriate bedding requirements where granular material should be used to bear the point loads away from the line of pipes.
The placing of the pipe on the trench should be done quite carefully in such a way as to keep the pipes in their position, and any protruding particles that could fracture the pipes should not be experienced. During welding, connecting devices like butt fusion or electrofusion techniques should be used, as these procedures join poles without leakage, which is very much needed for the security of the system. After the cement is fully set, backfilling should follow using the acceptable material, consolidated enough to hold the pipe but not to the extent of applying excessive pressure on it.
At every stage of the entire operation, accuracy, together with safety, is given the utmost regard where appropriate tools are used to align the markers and stamps and make sure there is adherence to requirements. Moreover, adding maintenance checks to the calendar contributes to the early detection of failures in a reliable, efficient piping system. Such professional remarks are meant to improve the installation processes of polyethylene pipes in different cases.
Maintaining HDPE Pipe for Longevity
Owning this profession and being an industry insider, I am apt to share good practical tips regarding the care of HDPE pipes for durability in a layman’s language. This maintenance of these pipes can help increase their life span as well as improve them, so let us get into the steps:
- Regular Inspection: Monitor the entire piping system for deterioration, rupture or obstruction on a regular basis. Timely identification of these cons saves the system from major defects in future.
- Cleaning: To prevent build-up of trash or sediments, flush out the interiors of the pipes regularly. This practice not only prevents build-up of unwanted materials but also enhances efficiency of flow.
- Monitor Joint Integrity:Inspect the joints and connections to assess if there are any slippages or leaks. If some joints are fused and are weak or damaged, fusing is to renew the integrity of the joints for a leak free system.
- Proper Pressure Management: Check and control the pressure used in the piping system carefully to avoid incurring structural stress on the pipes. Excessive pressure can cause damage to the pipes, however the right pressure levels help maintain the pipes for a longer time.
- Protect from UV Exposure: If HDPE pipes are to be used and are expected to be in direct sunlight, then provisions should be made for suitable covering, or ultraviolet protectors should be used. There are some materials which are affected by UV rays with time, hence it is best to limit the exposure.
- Adapting to Temperature Changes: Both heat and extreme cold has effects on the structure of the HDPE pipes. Appropriate measures should be taken when installing these pipes to incorporate self expansion and contraction mechanisms for different weather conditions.
- Utilize Technology: Use automated means to oversee the working of the pipes throughout the process. Such technologies allow for continuous measurement of pressure, flow, and integrity of pipes which facilitates timely maintenance measures.
The application of such simple guidelines can be significant in the management of HDPE piping systems, their reliability and durability in application being guaranteed.
Common Issues and Troubleshooting
In my extensive experience with HDPE pipes, it seems that there are numerous issues related to them, but if dealt with appropriately, these can enhance the system’s performance and reliability. Common problems and their solutions are reviewed in this context:
- Leakage at Joints and Connections:
- Issue: this happens mostly as a result of poor jointing or stress at the connections.
- Solution: Do not forget to inspect the joints during periodic operations. Ensure the joints have been constructed with adequate fusion techniques such as butt or electrofusion to ensure strong joints are achieved. Re-fuse or change joints that are defective in order to keep the system leak-proof.
- Blockages and Flow Restrictions:
- Issue: Attributed to the presence of debris, sediment, or deformation of pipes.
- Solution: Install periodic flushing at appropriate intervals to eliminate the block. Stubborn build-ups can be internalized by utilizing high pressure.
- Abrasion or Physical Damage:
- Issue:The walls of the pipes can suffer from extensive wear due to external forces or contact with abrasive materials.
- Solution: Employ proper protection to the pipes while bedding and backfilling to avoid contact with rocks and debris. Also, routinely monitor the worn-out surfaces of the exposed areas and provide additional reinforcement where necessary.
- Pressure Management Issues:
- Issue: Non-compliance of pipes with the required pressure levels leads to pipe and joint stress or even ruptures.
- Solution: Install permanent differential gages or automatic detectors to observe pressure all the time. Set operating parameters so that the measurements do not exceed the allowable values specified by the manufacturer.
- Thermal Expansion and Contraction:
- Issue: HDDP pipes are subject to swelling and tile or shrinkage due to temperature variations which may pose a threat to the structural integrity of the pipes.
- Solution:Create piping systems that withstand thermal changes. Where appropriate, use expansion joints or loops to accommodate these movements.
By appreciating such problems and taking preventive measures proactively makes quite easy and simple the maintenance of the durability and performance of HDPE piping systems.
Reference
- HDPE Supply – 8″ DIPS SDR11 PE4710 Black HDPE Pipe: This source provides specifications and pricing for 8-inch HDPE pipes used in water and geothermal applications.
- JM Eagle – HDPE Specification Sheet: This PDF document offers detailed specifications, including lengths and bending radius for HDPE pipes.
- Macomb Group – 8 IPS HDPE SDR 11 PIPE PE4710: Provides technical details about 8-inch HDPE pipes, including size, length, and connection type.
Frequently Asked Questions (FAQs)
Q: What is an 8-inch HDPE Pipe?
A: An 8-inch HDPE Pipe is a type of high-density polyethylene pipe used primarily for water distribution and irrigation. It is known for its durability and flexibility, making it ideal for a variety of applications, including water supply and temporary pumping installations.
Q: How does the 8-inch HDPE Pipe benefit agriculture?
A: The 8-inch HDPE Pipe is widely used in agriculture for irrigation purposes due to its corrosion resistance and ability to handle higher pipe pressure. This makes it suitable for distributing water efficiently across large fields.
Q: Can the 8-inch HDPE Pipe be used for potable water?
A: Yes, the 8-inch HDPE Pipe is safe for potable water supply, ensuring clean and safe water distribution for residential and commercial use.
Q: What are the product details of the 8-inch HDPE Pipe?
A: The 8 Inch HDPE Pipe features a double wall corrugated design, is available in lengths of 5.8 metres, and is designed to withstand higher pressures. It is suitable for both permanent and temporary water transport installations.
Q: Are there related products to the 8-inch HDPE Pipe?
A: Yes, related products include 4-inch HDPE pipes, lever lock couplings for water transport, and other composite materials for varied applications.
Q: How can I request a quote or more info about the 8-inch HDPE Pipe?
A: You can request a quote or additional info by visiting our website under the “Contact Us” section. Our customer service team will contact you within one business day.
Q: What are the shipping options for the 8-inch HDPE Pipe?
A: Shipping options for the 8-inch HDPE Pipe include direct delivery to your site or pickup from our factory. We ensure timely delivery to meet your project deadlines.
Q: Do you offer a warranty on the 8-inch HDPE Pipe?
A: Yes, we offer a comprehensive warranty on our 8-inch HDPE Pipes, covering any manufacturing defects and ensuring your investment is protected.
Q: What payment methods are accepted for purchasing 8-inch HDPE Pipes?
A: We accept various payment methods, including credit cards, bank transfers, and online payment systems, to facilitate a smooth and secure transaction process.
Q: How is the 8-inch HDPE Pipe used in engineering projects?
A: In engineering projects, the 8 Inch HDPE Pipe is used for water distribution and temporary pumping systems, owing to its strength, flexibility, and ease of handling.