High-density polyethylene (HDPE) pipes are widely regarded for their durability, flexibility, and resistance to corrosion, making them an ideal solution for various piping applications. However, the performance and longevity of HDPE pipes are heavily influenced by proper installation techniques, particularly in trench preparation and backfilling processes. This guide serves to provide a comprehensive overview of HDPE pipe bedding installation, focusing on the critical steps involved in trench preparation and the methods used for backfilling. Whether you are embarking on a new HDPE pipe installation or looking to refine existing practices, this article outlines key procedures and best practices to achieve successful results.
What is the recommended HDPE pipe bedding material?
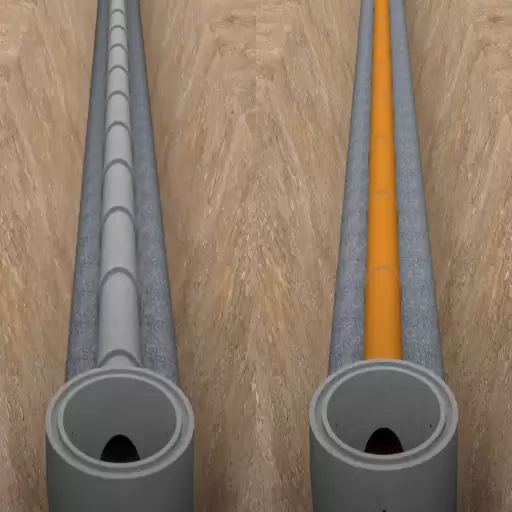
Sand for pipe bedding: when and how to use it
Sand is often selected as bedding material for HDPE pipes due to its property of providing even support and reducing point loading on the pipe. This is especially the case when the native soil consists of coarse and rocky material, poorly graded soil, or both, which are detrimental to pipe support and can cause damage to the pipe.
For best results, the sand in question must be clean, free of organics, and have the correct gradation as per ASTM C33. Proper compaction of the sand is required to provide sufficient structural support and stability for the pipe. Compaction should achieve at least 90% Standard Proctor (ASTM D698) relative density or as per project specifications. In most cases, sand layers are placed in lifts not exceeding 6 inches (150 mm) for uniform density and to minimize voids.
Alongside that, the degree to which the sand layer is bedded is also a determining factor. Usually, at least four (100 mm) inches of sand bedding under the pipe is suggested together with a sidefill and initial backfill of up to twelve (300 mm) inches over the crown of the pipe to accommodate proper load bearing and shield the pipe from external threats. Sound design and management of sand bedding guarantee effective operation with increased longevity of service of installed HDPE pipes.
Suitable gravel and stone options for HDPE pipe support
When choosing gravel and stone for HDPE pipe installation, one must pay particular attention to achieve the desired support, durability, and stability of the structure. Compared to rounded stones, crushed, angular, and uniformly graded aggregates are preferred as they provide better compaction and can bear greater loads.
- Crushed stone: Crushed stone is best for compaction and minimizing voids around the pipe therefore its ideal range is between 9.5 mm (3/8 inch) and 37.5 mm (1.5 inches).
- Gravel mix: This well graded gravel type II or type III does provide adequate support. This type of gravel can be classified whatever belongs to Clean Type and does not have excess fines (particles passing the No. 200 sieve should not exceed 5%-12%).
- Pea gravel: Although pea gravel can be used, its effectiveness for compaction and structural support prevents its use in most situations unless no other angular aggregate material is available.
Using the right material ensures it is strcuturally sound, minimizes displacement of the pipe, and is suitable for the surrounding soil which enables the HDPE pipe to function properly for a long period of time.
Materials to avoid: organic material and angular cobbles
It is primordial that no organic matter or angular cobbles be used as embedding materials or backfill materials when installing HDPE pipes.
Organic Material: Organic topsoil, peat, or vegetation is unsuitable at any level because erosion allows them to break down into voids which leads to a lack of support ultimately making the piping weightless. This undermines the bedding of the pipes and structurally cripples them over time. Additionally, Organic material captures moisture which causes additional sinking of the pipes and puts pipes on brittle failure margins.
Angular Cobbles: Cobble stones larger than 1.5 inches and having sharp irregular shapes are also angular cobbles that must not be allowed. These shapes tend to dig in the soft earth putting a point load on the surface area of the pipes leading to changes in shape, strength, and other harmful effects like stresses and damaging the HDPE pipes. In addition, sharp-edged cobbles cannot be compacted under and around the pipe which will leave voids in the soil above which negates the strength stone needed for support.
Meeting these material requirements and selecting crushed stone or clean sand which is characterized as well-graded, strong, and of the correct size and shape and which can be compacted to between 85 and 95 percent of Proctor density will guarantee the optimal performance and durability of HDPE pipes over time.
How deep should HDPE pipe trenches be excavated?
Calculating minimum trench depth for different pipe diameters
Trench depth must allow the pipe diameter, bedding, plus rough cover height, with the following key factors:
- Pipe Diameter (D): trench dimensions scale proportionally to the HDPE pipe external diameter. A certain amount of space must also be safeguarded around the pipe to facilitate installation and effective compaction of bedding material.
- Bedding Thickness (T): it is necessary to place a layer of granular bedding material, either clean sand or crushed stone, under the pipe with a thickness of between four to six inches (100-150 mm) depending on pipe diameter and type of soil.
- Pipe Cover (H): depth of cover placed over the pipe, planned to absorb traffic and soil load, is also important. HDPE pipes installed in zones without excessive traffic loads require a minimum cover depth of 12 inches (300 mm).
This guarantee that the pipeline is correctly supported and will remain in position for an extended period of time. Ensure these depend on project particular requirements and the predefined condition of the land for precise outcomes.
Required depth based on soil conditions and external loads
In assessing the anticipated depth of a pipe relative to soil conditions and lateral loads, I apply the following measures:
- Minimum Cover Depth: The industry standard minimum cover depth for HDPE pipes within non-heavy load zones is 12 inches (300 mm). This coverage protects against minor surface disturbances around the pipe.
- Traffic Loads: In areas prone to vehicular traffic such as highways or heavy equipment operations, I ensure that the cover depth is in accordance with AASHTO or relevant structural specifications which is often in excess of 24 inches (600 mm) dependently on the axle load.
- Soil Type and Compaction: The type of encasing soil and its consolidated form (clay, sand, or crushed stone) is significant. The higher the level of compaction employed (95% Standard Proctor Density or higher), the less the cover depth due to load distribution.
- Live and Dead Loads: The combined effect of live loads (temporary, dynamic loads like traffic) and dead loads (static, permanent forces from overlying soil weight) should be calculated using site-specific conditions and verified against pipe strength.
- Frost Depth: Certain climatic conditions require that the frost heave should not damage the pipe, which calls for installation at below the frost line as well as regional variation of 30 to 60 inches (750 to 1500 mm).
Considering these indicators and the relevant engineering standards, I can state the installation depth with a high degree of accuracy. Always conduct a site-specific assessment to guarantee safety and durability compliance.
Minimum cover requirements for PE pipe applications
Following common practices in engineering and covering industry standards, the minimum cover for Polyethylene (PE) pipes is usually determined by the application type and the external loads. In cases where traffic loads are absent, the minimum cover is generally 450 mm (18 inches). However, for areas where vehicular traffic or heavy loads are present, this depth increases considerably. Typically, such areas require a minimum cover depth of 600 mm (24 inches) to 900 mm (36 inches), depending on the load and soil strength.
- Live Loads: For vehicular traffic, the cover needs to be sufficient enough to ensure that there is no overstressing of the pipe and can distribute the load effectively.
- Pipe Stiffness: This is defined as the rigidity of a pipe about its material properties and diameter as its external pressures.
- Trench Backfill Quality: Poorly compacted backfill does not uniformly distribute the applied load, increasing the risk of localized stresses.
- Frost Protection: If installed in frost areas, the cover must take into account the frost depth from a damage provision for freeze-thaw cycles perspective.
- Site-Specific Analysis: Inadequate subgrade stability or adverse geological conditions may require departures from normal procedures and several guidelines.
Considering all these aspects, along with local engineering regulations, I can unconditionally define the cover depth that will provide long-term durability and proper functionality of the PE pipe under known conditions.
What are the standard trench width specifications for PE pipe installation?
Recommended trench widths based on pipe diameter
The trench width for the installation of the PE pipe needs to be chosen with care to achieve proper backfill and pack the surrounding soil effectively.
- For Pipe diameter lesser than or equal to 6 inches (150 mm): Minimum trench width Pipe OD + 12 inches (300 mm). This ensures enough room for the placement of backfill material and its subsequent compaction.
- For Pipe diameter between 7 inches (175 mm) to 12 inches (300 mm): Minimum trench width= Pipe OD + 16 inches (400 mm). These widths cover larger sized pipes, thus, ensuring ease of working around the pipes during the compaction process.
- For Pipe diameter greater than 12 inches (300 mm): Minimum trench width= Pipe OD + 24 inches (600 mm). It is easier to compact the backfill material and more accessible this way, therefore, wider trenches are necessary.
Inadequate working space leads to over-compaction of sidefill soil which is bad for the piping system. Moreover, the specified distances lessen the chances of pipe movement and help the installed system retain its strength as per the stipulated engineering requirements. Wrapping up, specific soil stability analysis together with geotechnical guidance should be incorporated to validate determined trench sizes.
How to prepare the trench bottom for proper pipe support
To facilitate standard pipe support, the trench bottom should be prepared systematically. As an example, the trench bottom should be graded and completed without ledges, which include rocks and debris that can damage the pipe. The trench should be graded to have a final slope that matches the pipe configuration; in most cases, a gradient of one to two percent is used for drainage systems to assist in gravitational flow operations.
In addition, for augmentation of support, bedding materials such as sand, crushed rock, or other granular materials should be introduced and compacted at the base of the trench. For most cases, the bedding layer should be at least 100 millimeters and up to 150 millimeters thick, depending on the diameter of the pipe and load constraints. To prevent material from settling under load, compaction should meet a relative density of at least 95 percent Standard Proctor. During compaction, attention should also be given to the moisture content as it is directly proportional to the density of the material and pipe stability.
For pipes needing additional alignment or load restriction dragging, trench bottom preparation may also include over-excavation and provision of engineered fill to increase support.
Techniques to prevent the collapse of the trench walls
To minimize the risk of a trench wall collapse, various engineering methods and precautions should be taken depending on the type of soil, the depth of the trench, and any environmental factors. The following methods are recommended:
- Shoring: Use plywood, hydraulic shores, or steel plates by OSHA regulations to support the walls of the trench. Trenches exceeding 5 feet deeper must be shored unless stable soil conditions permit otherwise.
- Sloping: Cut the trench wall vertically at an angle that is further away from the excavation’s center.
- Bench cutting: Carve a series of horizontal ridges on the trench wall to reduce movement’s shear strength. Similar to sloping, bench cutting depends on soil type and limits have to be met.
- Shielding: Utilize trench boxes or shields to protect workers by serving as a barrier against collapses. These are especially critical for unstable soil conditions.
- Water Management System: Remove water from the trench using fans or ditches to maintain soil integrity. Overly saturated soil coupled with a lack of support greatly increases the chances of a collapse.
- Inspection and Monitoring System: Check site safety regulations with attention to detail and change the protective measures accordingly. Carry out inspections with, and after, heavy rain.
Using these strategies and sound engineering judgment guarantees the stability of the trench as well as the protection of the workers from dangerous collapses.
How should backfill be applied around installed HDPE pipes?
Proper layering and compaction of embedment material
The steps of properly layering and compacting embedment material are core to the stability and functionality of HDPE pipes. In this regard, the embedment process starts with pouring granular materials like sand, pea gravel, or crushed stone that conform to the standards ASTM D2321 norms. Suitable materials should be placed uniformly in layers that are 6-8 inches thick, and subsequently placed around the pipe.
To improve soil-pipe interaction and mitigate the chances of settlement, each layer needs to be compacted to a minimum density of 90% standard Proctor density. The recommended methods of compaction for trenches include the use of hand tools and vibratory plates. Careful compaction drum dimension should be utilized for areas that are closer to the pipe’s haunches to avoid any voids that could put the pipe at risk of unfavorable support.
The moisture content factor, which ideally needs to be 2% within the optimum moisture content, is also prominent during embedment Effective inspection during the placement and embedment processes guarantees operational safety by containing deflection and pipe overloading risks.
Final backfill procedures to protect the pipeline
The last stage in the backfill sequence is essential for guaranteeing the lasting operational effectiveness and physical robustness of the pipeline. For this stage, it is necessary to have a backfill material, usually devoid of big rocks, boulders, or vegetation, which could potentially harm the pipe. In addition, the material has to comply with some project’s mechanical and geotechnical conditions like gradation, density, and cohesion.
The depth of each layer is restricted to a maximum of 200 to 300 mm (8 to 12 inches) before compaction, where the layers have to be distributed in equal parts. Every layer needs to be compacted to a minimum of 95 percent of the maximum dry density that is measured by the Standard Proctor Test (ASTM D698). Such standards of compaction enable minimizing settlement risks or adequately supporting the pipe.
To avoid inflicting mechanical damage on the pipeline, only light equipment should be allowed to pass directly over the trench during the backfilling phase. During this stage, heavy compaction equipment should stay at a specific height above the crown of the pipe, for example, 600 mm (24 inches) above the top of the electric pipe, depending on the size and material of the pipe.
For the last inspection during the backfill process, all parts of the backfill and soil must ensure that there are no vertical or horizontal changes in the soil surface booth and that all compaction requirements have been met. Supervising the settlement that will occur and the final grading could accurately measure how much soil is put within the trench to best serve the contour of the surrounding land.
If these methodologies are closely adhered to, it ensures that settlement which is often due to external structural activities, as well as operational loads and even environmental elements do not severely impact the pipeline.
What are special bedding considerations for PE pipes having a protective outer layer?
Bedding requirements for polyethylene pipe with protective coatings
Caring for the bedding of PE pipes with external protective layers has been proven to be an issue for their longevity and efficiency. Sharp edges such as stones and plaster must not be included as their presence may damage the protective cover. Optimal support features perforated sheets or granular materials with particle sizes from 4 to 20 mm.
To provide uniform support stresses the required thickness of the bedding layer must be 100-150mm for the pipe. The pipe is under deformation risks due to various loads being transferred unevenly so sidefills and initial backfills should be made of coarse material. Compacted coarse mediums will prevent deformation. Care has to be taken to avoid compacting too much as overfilling can put too much force on the protective layer.
The long term goals of stabbed grade bottoms should seek to remove material in certain areas to control localized tensions along the trenches and allow them to support stresses. The water amount in the bedding material will aid in controlling movement and help make the system stable. Following these restrictions will aid with the harsh changes to polyethylene pipes.
How to prevent damage to outer layers during installation
To minimize harm to the outer surfaces during the installation phase, damage control strategies must be implemented. The first step is to make sure that the trench width is appropriate for the placement of the pipe so that no undue pressure is exerted on the pipe during the backfilling operation. For pipes with diameters that are magnitudes greater than some value (depending on the size of the pipe and its load requirements), the width of the trench ought to be at least 0.2 to 0.4 meters greater than the diameter of the pipe.
The bedding material must consist of granular material with a portion of 4-10 mm so that it can support uniformly as well as ensure that there is proper load bearing to decrease the point loads on the surface of the pipe. Ensure that the compacted bedding thickness under the pipe does not go below 100 mm, and also make sure that water in the bedding material concurs with ideal moisture content values, which normally range from 8-12% so that adequate compaction can be achieved without over-saturation.
Both backfilling and compaction should ensure that no layer is thicker than 150 mm, and each layer must be compacted to at least 85-90% of the maximum dry density, especially in the haunch zone so that the stability is maintained and pipe deformation does not occur. Avoid using sharp or oversized materials as they will abrade or puncture the surface of the pipe.
In addition, forces exerted by installation equipment near the pipe should not exceed a certain level. Heavy construction loads should be avoided over partially filled trenches, limiting vibratory compaction should be reserved for at least 0.3m away from the pipe, and assuming these measures will maintain the integrity of the outer layers.
With the addition of these methods, the performance and effeciency of the system’s structure, supporting pipes, and other components will be dramatically improved in the long run.
Reference sources
Frequently Asked Questions (FAQs)
Q: What are the key considerations for excavation when installing HDPE pipes?
A: When excavating for HDPE pipe installation, the trench should be excavated to provide sufficient space for proper pipe placement and compaction of backfill materials. The trench width should typically be at least 1.5 times the pipe diameter. Remove any large rocks, angular gravel, or cobbles that may damage the pipe. The excavated material should be inspected to determine if it can be reused as a backfill or if imported bedding material is necessary. In rural areas, native soil may be suitable if free from sharp objects, while urban installations often require imported bedding. Always ensure proper safety measures for open trench work, including shoring and barricades.
Q: What type of pipe bedding should be used for HDPE pipes?
A: The appropriate pipe bedding for HDPE pipes depends on soil conditions and application. Generally, a well-graded, compatible granular material like sand or fine gravel (less than 19mm) is ideal. For water mains and pressure pipes, AWWA standards recommend a minimum bedding depth of 100-150mm. Cobbles should not be used for bedding as they can damage the pipe. In areas with poor soil conditions, imported bedding with consistent gradation is necessary to provide uniform support. For sewer applications or where groundwater is present, the bedding should also promote proper drainage while providing consistent support for the flexible HDPE pipe.
Q: How should HDPE pipes with protective outer sheath be handled during installation?
A: HDPE pipes with protective outer sheath require special attention during installation. The bedding material should be free of sharp objects that could penetrate or damage the sheath. When the HDPE pipe has a multi-layer or protective outer sheath, the excavation must be clean and smooth. Manual placement of bedding material directly around the pipe may be necessary to prevent damage. The backfill process should avoid impact or abrasion against the protective layer. If the excavated material contains sharp or angular particles, it should not be used for direct contact with the pipe, and imported bedding should be used instead to maintain the integrity of the protective sheath.
Q: What are the proper techniques for fitting HDPE pipes in the prepared trench?
A: When fitting HDPE pipes in a prepared trench, ensure the pipe is lowered carefully to avoid damage. The pipe may be installed directly on the prepared bed if the soil is suitable. Provide proper support at fitting locations, as these are often more rigid than the pipe itself. Allow sufficient space for thermal expansion and contraction, particularly for longer runs. For electrofusion or butt fusion fitting connections, ensure the joint area remains clean and dry – excavated material should not contaminate the fusion surfaces. When installing fittings, provide additional bedding support beneath them to prevent sagging. Finally, before completing the installation, check that the pipe and fittings have the recommended minimum cover depth for the application.
Q: How does soil type affect the excavation and bedding requirements for HDPE pipe installation?
A: Soil type significantly impacts HDPE pipe installation requirements. In stable soils like well-graded sands or gravels, excavation is typically straightforward, and the excavated material may be suitable for reuse as bedding and backfill. In contrast, clay or soil containing organic material often requires complete replacement with imported bedding to ensure proper support and drainage. Rocky soils necessitate careful excavation to prevent pipe damage, with all large rocks removed from the bedding area. Unstable soils may require wider trenches with special bedding designs. For wet conditions or high water tables, additional drainage provisions and more extensive imported granular bedding are needed to establish a stable foundation for the flexible HDPE pipe system.
Q: What backfill methods are recommended for HDPE pipes in gravity sewer applications?
A: For HDPE pipes in gravity sewer applications, the backfill should be placed in layers not exceeding 150-300mm in thickness, with each layer properly compacted to at least 85-90% Standard Proctor density. The initial backfill directly above the pipe should be carefully placed to avoid displacing the pipe. Material similar to the bedding is recommended for this zone, free of large stones or debris. The flexible nature of HDPE allows it to resist some deformation, but proper compaction is still essential to prevent excessive deflection. In sewer installations, particular attention should be paid to achieving consistent support along the pipe invert to maintain proper gravity flow. Imported angular material may be necessary around the pipe to achieve the required structural support while allowing for minor ground movement.
Q: What special considerations exist for HDPE pipe installation in rural areas?
A: HDPE pipe installation in rural areas presents unique challenges and opportunities. In rural settings, native soil may be used for bedding and backfill if it meets quality requirements and is free from sharp objects or large rocks. The wider spatial availability in rural areas often allows for more spreadable excavated material storage and easier machinery access. However, rural installations may encounter more varied soil conditions, including unidentified rock formations or agricultural drainage systems. Access to imported bedding materials may be limited or costly due to transportation distances, making proper assessment of existing soil reusability crucial. Additionally, rural installations often cross natural waterways or environmental features, requiring special bedding designs to prevent erosion and ensure long-term stability in these sensitive areas.
Q: How can you verify proper trench preparation before installing HDPE pipes?
A: To verify proper trench preparation before HDPE pipe installation, first check that the trench dimensions (width and depth) meet specifications for the pipe size and application. Ensure the trench bottom has a consistent grade without high or low spots that could cause uneven support. The bedding material should be placed and graded to provide uniform support with the correct thickness (typically a minimum of 100mm). Verify that the bedding material meets the specified gradation requirements and has consistent compaction. Check for any protruding objects, large rocks, or foreign materials that could damage the pipe. If groundwater is present, confirm that dewatering measures are effective. Finally, document the trench condition with photographs or inspection records to demonstrate compliance with project specifications before pipe placement begins.