Determining the correct burial depth for High-Density Polyethylene (HDPE) pipes is a critical factor in ensuring long-term performance, structural integrity, and safety in both commercial and residential applications. Whether you’re designing a drainage system, utility network, or irrigation infrastructure, understanding the maximum and minimum cover heights is essential for meeting engineering standards and preventing failures. This article provides a comprehensive guide to the principles, technical considerations, and industry best practices for HDPE pipe burial depths, equipping you with the insights needed to make informed decisions for your project.
What Are the Recommended HDPE Pipe Burial Depths?
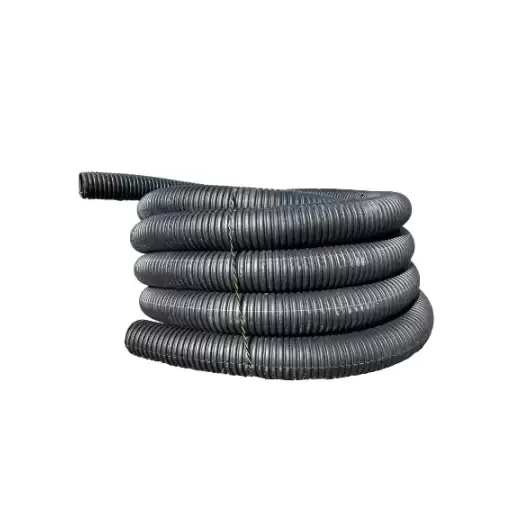
How Is the Minimum Burial Depth Determined?
The minimum burial depth of HDPE (High-Density Polyethylene) pipes is excavated utilizing impact damage to the structure as the main overriding factor with external loads that the pipe will be subjected to. Industry standards provide a cover thickness between 18 and 36 inches, depending on the application and circumstances. Requirements can still be altered by soil type, installation site, traffic load, and other unidentified conditions.
Burial depth will be chiefly influenced by the hoe the pipe will be loaded. Soil cover to street level must be sufficiently deep so that surface compressive stress is distributed throughout the cover and damage is avoided. More rigid construction guidance is called for under pavements where highways are subject to strong dynamic forces over extended periods. Softer, weaker, or more unstable soils may call for greater burial depth to ensure enhanced stability.
Environmental factors such as frost heave, UV deterioration although frost heave pose greater concern, protective measures are enforced once the pipe is buried. Manufacturer recommendations need to be accompanied with guidelines posed by industry leaders such as ASTM and AASHTO alongside local legislations to establish appropriate minimum burial depth for the desired application of the pipe.
What Factors Influence the Maximum Burial Depth of HDPE Pipes?
The HDPE (high-density polyethylene) pipe’s maximum burial depth is determined by a few factors, such as the pipe’s mechanical properties and soil conditions. The pipes’ mechanical properties, which include wall thickness, diameter, and stiffness class, will affect the mechanical strength because of the soil and traffic load pressure. A pipe with greater stiffness or a thicker wall structure can withstand higher amounts of pressure and therefore be buried deeper.
Soil surrounding the pipe has a direct impact on the external load applied as well as on the pipe’s inner structural support. Soil type, density, and moisture content have a direct impact on humidity level. Compared to loosely consolidated or highly plastic soils, well-compacted granular or select fill soils offer greater resiliency and added strength. Proper void elimination on and around the pipe is crucial to protecting the pipe from local stress concentration, which causes excessive deformation or failure.
External load factors also modify the maximum permissible burial depth. Some examples are the overburden soil weight, live loads from vehicle movements, and other dynamic forces impacting the pipe. For deeper placements, computations require the consideration of vertical and horizontal loading for sustained performance over time.
How Does Pipe Diameter Affect Burial Depth?
The safe burial depth of underground installations relates to the diameter of the pipe. A larger diameter incurs a shallower burial depth because its greater cross-sectional area makes it more prone to deflection and stress under imposed loads. On the contrary, smaller diameter pipes can withstand deeper burial due to reduced surface area and lower flexibility which aids in resist deformation under pressure.
Moreover, pipe diameter influences load distribution. When larger diameter pipes are buried at greater depths, they are subjected to additional soil pressure because of the overburden soil. Without proper support measures, like adequate bedding or encasement materials, this will cause structural deformation. When paired with supportive materials, smaller pipes do not experience extensive load redistribution, which makes them more adaptable to deeper installations.
Regulatory standards like ASTM and AASHTO provide guidelines to ensure optimal burial depth for pipe diameter. Well-defined charts and formulas in these organizations consider specific conditions such as soil type, load characteristics, and material properties. Following these standards greatly reduces the risk of structural failure while maintaining the pipe’s longevity.
How Does Material Choice Affect HDPE Pipe Installation?
What Are the Key Material Properties of HDPE Pipes?
To me, one of the main characteristics of HDPE (High-Density Polyethylene) pipes is their flexibility and light weight. These aspects greatly facilitate transportation and installation in regions that are remote or rough-shod with uneven land. In contrast to other, more rigid materials, HDPE’s ability to bend without cracking under tension allows it to adapt to changing movements or ground shifts. This benefit helps to make HDPE pipes useful where there is likely to be seismic activity or soil erosion.
Another critical property is HDPE’s resistance to chemical corrosion and abrasion. The pipe material is able to resist exposure to a variety of chemicals like: acids, bases, and salts which make it useful for certain industries like agriculture, mining, and even wastewater management. Moreover, this resistance is also applicable to internal and external conditions making the pipe usable even after long periods of time in severely corrosive environments.
Finally, HDPE pipes have outstanding durability, often lasting over 50 years with proper care. Its wide acceptance is further attributed to its resistance to UV degradation when treated, its ability to endure extreme temperatures with little impact on performance, and its low efficiency in thermal conduction which aids in applications needing temperature control. All of these factors deem HDPE pipes as dependable and useful for many construction and utility works.
How Do Material Differences Impact Installation?
Material differences are crucial in deciding installation methodologies, equipment needed, and project costs. As an example, high-density polyethylene (HDPE) pipes are light and highly flexible, making them easy to handle and install, especially in trenchless applications, which decreases labor costs. Conversely, rigid polyvinyl chloride (PVC) and steel constructions have lower flexibility and higher weight, which increases the need for support structures and specialized equipment.
Thermal expansion is another important factor. Pipes constructed of non-metallic materials, like HDPE, will require design modifications to cope with non-uniform stresses that arise due to temperature changes because they expand more than their metal counterparts. In addition, different materials have different techniques of joining together. For instance, HDPE uses advanced fusion welding, which guarantees strong and leak-proof connections, while solvent welding or mechanical joints are used in PVC. Metals use threaded, welded, or flanged connections, all of which increases time and complexity for installation.
In the end, understanding the materials’ physical characteristics along with the specific operational and environmental conditions helps ensure installations are straightforward, efficient, and with minimal risks and long-term maintenance needs.
What Role Does Pipe Material Play in Performance?
For instance, a pipe material’s type determines the performance of a system, its pipe flow efficiency, longevity, and upkeep needs, alongside maintenance costs. This is why a material such as stainless steel, while useful in industrial applications owing to its resistance to high temperatures and pressures, becomes corroded, over time, in acidic or saline environments. Thermoplastics such as PVC and HDPE, on the other hand, are best at cost-effectiveness. However, while lighter, they are also mildly corrosion resistant at higher temperatures or under constant high-pressure loads.
Pipe material has a direct impact on its flow characteristics. The type of material used determines the friction caused by flow due to surface roughness on the inside of the pipe. Smooth surfaces such as PVC or HDPE allow for a more effortless flow of materials compared to metals, which have a high internal surface roughness. However, the use of aggressive media requires consideration of factors such as chemical compatibility. For example, Polypropylene pipes are more suited for environments with strong acids and alkalis, while metals require protective linings or coatings to function efficiently.
Developments like the invention of cross-linked polyethylene (PEX) and fiberglass reinforced polymer composites have diversified options for technologies. System designers are now able to optimize life expectancy, operational efficiency, and minimize costs and environmental impacts by choosing materials tailored to specific operating conditions and design tuning options. This decision needs to be made by evaluating operational dynamics, performance metrics, legal policies, and business compliance policies for the desired time frame.
What Are the Application Requirements for HDPE Pipes?
What Are Common Applications for HDPE Pipes?
- Municipal or Industrial Water Supply Systems: Given the high resistance to corrosion and pressure, HDPE pipes are used extensively in industrial and municipal water supply systems. Best performance is delivered under optimal use conditions and is associated with very minimal leakage. Lifespan is more than 50 years.
- Drainage Systems and Sewage Systems: These pipes are very adaptable for drainage systems and wastewater due to aggressive flow and high levels of chemicals. Their very smooth internal surface reduces friction to a minimum, and this increases the efficiency of the fluid flow in the installations.
- Gas Distribution: These pipes are also very lightweight and resist impacts while being punctured. That is why they are considered the preferred option when it comes to transporting natural gas. There is guaranteed, safe, and long-term operational use when it comes to dealing with resistant chemicals.
- Agricultural Applications and Irrigation: HDPE pipes are used in drip irrigation systems, but they also serve other functions in agriculture. Not only does resistance to UV light allow these systems to function very well in variable field conditions, but it also works with severe direct sunlight. Minimum water exposure is ensured, and HDPE pipes can perform well under these conditions.
- Chemical and Industrial Uses: The characteristic HDPE pipes possess for chemically resisting most industrial chemicals makes them ideal candidates for the distribution of chemicals, acids, and toxic fluids. Their strength in an unforgiving atmosphere coupled with minimal upkeep makes them economical for industrial activities.
Every one of these applications utilizes the relied upon HDPE’s attributes, traits, and properties spanning numerous industries.
How Is Burial Depth Influenced by Application?
The burial depth of HDPE pipes is primarily determined by application-specific factors such as type of load, soil conditions, pipe diameter, and external environmental stress. For example, pipes used in roadways or regions with heavy vehicle movement must be buried deeper to resist both static and dynamic loads. Industry guidelines suggest these pipes may need, at a minimum, 24 to 36 inches of cover under LED pavement, and this depends on local rules and load classes.
For non-traffic activities like irrigation and chemical transport in farmland, the depth of burial may be shallower because of the absence of heavy loads on the surface. However, the frost line, the type of soil (like compacted clay or loose sand), and even some external factors like agricultural equipment do impact the region. Studies state areas that undergo cycles of freezing and thawing require adequate depth for burial (often below the frost line, which can be 20 inches and soar over 70 inches depending on climate and geography) to protect the structure from damage by thermal expansion or contraction.
The combination of the trench design, backfill material, and the structural integrity of the HTPE pipes also affects the burial depth. To ensure pipe performance, durability, longevity, and efficiency, engineers use finite element modeling to simulate varying loads and depths to optimize pipe performance.
How to Verify HDPE Pipe Installation Depth?
What Are the Steps to Verify Correct Burial Depth?
A systematic verification process should be maintained to make sure that the Installation of HDPE pipes is done at the given burial depth:
- Go Over Project Specifications: Check the engineering designs and associated project documents to validate whether the specified burial depth warrants attention. Also cross check if these specifications refer to atleast industry benchmarks like ASTM F714 or ISO 4427 regarding HDPE piping systems.
- Go For A Pre-Installation Survey: Surveying devices like laser levels and total stations should be used to check and mark the intended trench depth vis-à-vis the various levels that have been excavated with a predefined goal to ensure that achievement is realized.
- Post Trench Check: The depth of the trench should be checked at particular intervals along its length with appropriate measuring devices. Ensure that the set minimum and maximum limits of burial depth vis-à-vis the pipe diameter and the soil conditions are met.
- Check the Bedding Material: Verify the bedding material’s layer for compliance in depth and uniform ground level below the construction of the wall specifications. There should be a pipe, bedding which should serve as a base elastically, such that it supports without drilling to the outer enclosure mark without any indentation leading to stress concentration.
- Check While Installing the Pipe: Check the installation of the pipe in sections to make sure the HDPE pipe on the trench floor is sitting at the proper depth. All necessary checks should ensure the pipe sits at the correct level. Additionally, confirm that grade slopes for gravity flow systems are also accounted for.
- Measure Cover Depth After Backfilling: Cover depth measurements of the surrounding material on the pulled pipe should only be calculated after initial backfilling has been added. The step guarantees that the pipeline does not lie too near the surface and offers scrutiny of cover depth specifications. Measurements should be done further to protect the surface against external loads and other environmental influences.
- Document All Measurement and Observations: All depth measurement documents, alongside inspection notes, must be kept on file and organized. Digital methods with GPS capabilities or mobile devices are recommended if the accuracy and reliability of the files being documented are important.
- Verification through Testing and Reporting: Conduct necessary tests like load resistance tests or continual monitoring for any shifts over time to visually confirm if all burial depth criteria have been met. This is more so relevant if there is an observed need for them. Such tests are useful in confirming that standards surrounding performance checks and construction are all met with the required level of HDPE piping installed.
These combined with advanced technology like GPS positioning, satellite and aerial imagery enable pre-trench 3D modeling surveys which allows test planners and trench planners to optimize technical geotechnical HDPE piping networks. Geospatial and engineering surveying can allow them to meet legal standards while optimizing the service life of the systems.
What Are the Technical Considerations for Accurate Installation?
Planning, execution, and conformity to the relevant technical instructions are some of the basic requisites necessary for the accurate installation of HDPE piping systems. Pipe load, soil type, trench width and depth, as well as the minimum required gap for inflow, clearance, and deformation, are all considerations that must be taken into account while designing a trench. Groundwater depth is also critical. Engineers must observe appropriate piping trench width and depth, with a bare minimum space required to allow for vertical deformation under load.
Granular material should also meet the appropriate compaction strength to create adequate pipe inertia base and side supports. Strong inflationary deflationary forces must be withstood, including falling debris or fluids, to prevent deflection or deformation. Aside from engineering principles, standards which outline underground thermoplastic pipe system guidelines also enforce compliance through stipulating appropriate material gradation, compaction density, and freestanding force specifications.
Various jointing methods are also essential to installation. Seeing to surface preparation and their alignment is necessary in the case of butt fusion welding or electrofusion. The use of calibrated fusion equipment permits dependable long-term joint success by eliminating joint failure conditions. Also important is ensuring that pipes are not angled at joints that cause sharp directional changes. This ensures that stress concentrations capable of causing premature failure are avoided.
At last, environmental influences in the form of thermal expansion (or contraction) must be incorporated into the design of the installation. To mitigate these stresses due to temperature changes, flexible joints or expansion loops can be installed in long pipelines. Installation procedures often require periodic checks to confirm accuracy and operational sustainment over time, which can include non-destructive evaluations like ultrasonic testing of fusion welds.
With the aforementioned components of advanced design and precision control aimed at quality incorporation, advanced tools inadvertently contribute to achieving HDPE piping systems functionality and extending their service life.
What Is the Impact of Soil and Pipe Systems on Burial Depth?
How Does Soil Type Affect HDPE Pipe Burial?
The soil type that encircles the HDPE (High-Density Polyethylene) pipe is of utmost importance because it encompasses the soil’s infrastructure, performance, and sustenance. The amalgamation of soil attributes like bulk density, moisture ratios, soil matrix quantifiable proportions, and cone penetration resistance directly affects the dominating external forces, such as the traffic load and superstructure material-overburden material, which have on the pipe and will directly influence the support to the pipe.
Encapsulated soils, such as sand and gravel, are defined by their granular nature. When compacted, they prove useful in minimizing the obstruction posed by the HDPE pipes towards water flow while maximizing load-bearing capabilities. This distinct feature has enabled the use of such materials for backfilling, still achieving geometry change while lowering deformation hydraulic pressure around the pipe. The same cannot be said about fine-grained soils like clay and silt, as they are more sensitive to fluctuating water levels, which drastically alter the terrain’s support yields.
Lastly, the surrounding soil level controlled with the compaction skirt is equally important. On one side, a lack of defined parameters can result in altering the pipe arrangement while causing uniform flow to ensue around the pipe, leading to unequal pipe pressure. On the other side, the beyond set limitations can yield to overpowering stress being applied while extruding the pipe walls at the time of setting the pipe tools. Layered cylindrical placement and compacting, which is mostly done through mechanized means, guarantees enhanced overall aggregate performance of the HDPE pipe system.
Specific requirements and guidelines are provided for the classification and placement of soil to enhance the dependability and operability of buried HDPE pipe systems. Considering the type and composition of soil enables engineers to design and install effective piping systems that provide enduring structural reliability and operational strength.
How Do Pipe Systems Vary in Different Environments?
Pipe systems are affected by environmental parameters such as temperature, soil, and even vegetation which pose challenges during the installation. In the case of HDPE pipes for arid and hot areas, the pipes undergo ‘material fatigue and deformation’ due to overheating and soil drying. To counter this, UV radiation resistant coatings are used, in addition to using thermal expansion properties enhanced HDPE pipes.
For cold areas and regions with permafrost, pipes undergo constant contraction and expansion due to freeze-thaw cycles. To counter this, flexible piping such as cross-linked polyethylene or PEX is used. And to minimize damage as well as ensure a constant flow, additional insulation layers and protective materials are used to reduce exposure to thermal extremes.
Subterranean piping systems require special join techniques, ductile iron, and even PVC to minimize leakage due to subsidence as well as vibrations. And in order to guard against construction activities, enhanced load bearing materials along with reinforced bedding are embedded.
Marine and coastal installations face unique difficulties due to the presence of saltwater, increased pressure, and biofouling. In such settings, FRP, alloyed metals, or HDPE pipes with protective coatings require corrosion resistant materials. To avoid collapsing due to extreme current or tidal forces, anchor systems and trenching techniques are used.
Design and maintainace of a pipe system to withstand diverse conditions requires a specific approach to every environment’s geotechnical, chemical, and physical dynamics.
What Is the Role of Backfill and Level of Compaction?
Along with backfill height, backer height, and compaction, directly impact the strength and durability of buried HDPE pipe systems. Proper backfill materials range from granular or well-graded soil down to sand and silt that will sustain the pipe and fill empty spaces around it. The material properties within the backfill directly impact how the pressure is distributed, controlling collapse due to overburden and surrounding weight.
Equally important is compaction, since it improves the density and contact between soil particles, which further enhances support to the pipe. The failure to ensure compaction or due of the wrong materials can cause differential settlement or pipe movement, which may lead to system collapse. Most need 90-95% compaction and it is recommended to create stability without excess pressure causing pipe collapse.
Mixing appropriate backfill materials and strict control over tampering procedures increases the stability of the soil surrounding the pipe while reducing the amount of water able to sneak I,n and external pressure can greatly improve efficiency and lifespan of the HDPE pipe systems.
References
Frequently Asked Questions (FAQ)
Q: What is the minimum cover required for PE pipes under vehicular traffic?
A: The minimum cover required for PE pipes, such as N-12 WT pipe, under vehicular traffic is highly influenced by the type of backfill and the level of compaction around the pipe. According to the drainage handbook, pipes must have at least 300 mm of cover to protect against vehicular loads.
Q: How do you determine the maximum cover heights for corrugated HDPE pipes?
A: The maximum cover heights for corrugated HDPE pipes are determined by the pipe’s design and installation conditions. The PE pipe manufacturer’s guidelines and the drainage handbook provide general maximum cover limits, which are included in the minimum cover and maximum burial depth calculations. The maximum burial depth is highly influenced by factors such as soil type and vehicular traffic.
Q: What factors highly influence the burial depth of PE pipes?
A: The burial depth of PE pipes is highly influenced by the type of backfill used, the level of compaction around the pipe, and the expected loads, such as vehicular traffic. The installation section of the technical note and the drainage handbook provide detailed guidance on these factors.
Q: Why are PE pipes preferred for certain drainage applications?
A: PE pipes, including PE 100, are preferred for certain drainage applications due to their flexibility, durability, and resistance to chemical and environmental factors. They can withstand a variety of backfill conditions and have been shown in Table 3 to perform well under different installation scenarios.
Q: How is the hydrostatic pressure managed in PE pipe systems?
A: Hydrostatic pressure in PE pipe systems is managed through proper design and installation, including ensuring correct burial depths and selecting appropriate pipe materials. The drainage handbook and manufacturer guidelines provide calculations and specifications for managing hydrostatic loads.
Q: What are the recommended maximum burial depths for PE pipes?
A: The recommended maximum burial depths for PE pipes are provided in the drainage handbook and are shown in Table 3 for a variety of backfill conditions. These depths are highly influenced by installation conditions and the type of traffic loads expected.
Q: How does the type of backfill and level of compaction affect PE pipe performance?
A: The type of backfill and level of compaction are crucial for PE pipe performance. Proper backfill materials and adequate compaction ensure the pipe is supported and protected, minimizing the risk of deformation or failure. Guidelines are typically provided in the manufacturer’s handbook and technical notes.