High-Density Polyethylene (HDPE) pipes have become a critical component in various industries due to their durability, flexibility, and cost-effectiveness. Among the numerous classifications of HDPE pipes, SDR 11 pipes stand out for their balance between strength and wall thickness, making them ideal for high-pressure applications such as water distribution, gas lines, and industrial usage. This article dives into the specifics of SDR 11 HDPE pipe dimensions, examining what SDR represents, the relationship between pipe size and pressure capacity, and how these specifications align with industry requirements. Whether you’re an engineer, contractor, or decision-maker, understanding these dimensions is vital to ensuring efficiency, safety, and compliance in your projects.
Introduction to SDR 11 HDPE Pipes
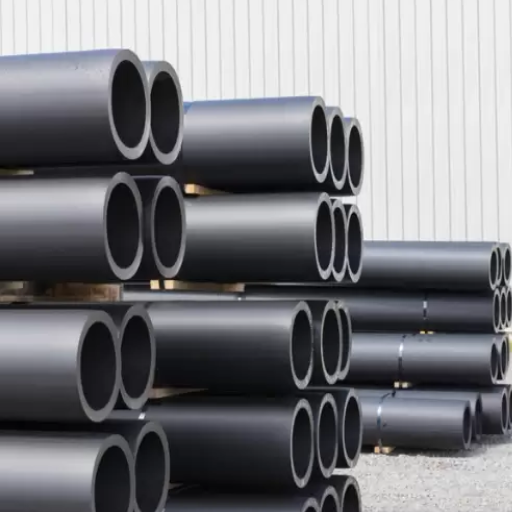
What Does SDR Mean?
SDR or Standard Dimension Ratio is used to specify the pipe wall thickness to outside diameter relationship. In simple terms, SDR equals the ratio of the pipe’s outside diameter to its wall thickness. Since this ratio is inversely related to pressure rating, SDR, when small, indicates thick walls that can resist high internal pressures.
For SDR 11 pipes, the “11” itself represents the Standard Dimension Ratio. This simply translates to the fact that the outer diameter of the pipe is 11 times the thickness of its wall. Pipes with SDR 11 provide an ideal compromise of strength to material and hence can be used in high-pressure applications such as water distribution systems or industrial pipelines.
Understanding SDR is important because it affects the strength, service life, and performance of HDPE piping systems. Those pipes having a lower SDR value, hence thicker walls, are more suitable for cases that require high-pressure tolerances, while those pipes with a higher SDR, thinner walls, might be cheaper to buy but will not resist pressure very well. This prime relationship will enable engineers and designers to select for their needs, optimally designed pipes based upon particular functional and operational requirements.
Importance of SDR 11 in the Piping Industry
SDR 11 is important in the piping trade because of the balance struck between pressure resistance and material usage. The pipes with an SDR 11 rating have thicker walls than those with higher SDR ratings and can resist higher pressures. Hence, these pipes find use in scenarios where high pressure must maintain structural integrity-water distribution systems, natural gas pipelines, or industrial fluid transportation systems.
Selecting SDR 11 pipes guarantees greater durability and serviceability over time. The thick-walled structure lessens the chances of cracks, leaks, or ruptures in a pressurized setting, thereby increasing the extended serviceability probability of a piping system. This kind of reliability is highly consequential in the industrial and municipal setting, where downtime, safety hazards, and tremendous repair costs shall be met with upon any failure.
Besides, SDR 11 design specifics impart engineers with the means to work under diverse conditions. Operating under anything from high temperatures to corrosive conditions, pipes under the SDR 11 classification are made to withstand the highest safety and performance levels, thereby allowing the programs to comply with regulations and provide infrastructure solutions of the highest quality and reliability to critical projects.
Why Choose HDPE Pipes?
HDPE pipes have been widely utilized in various applications because of their strength and versatility. They resist corrosion, chemical action, and environmental influences such as UV radiation and, therefore, are safe for long-term use where environmental conditions are harsh. These characteristics imply very low maintenance and long service life, which consequently reduces operational costs.
Another big benefit of HDPE pipes stems from their flexibility and ability to absorb impacts from great external pressure such as soil movement and heavy loads without cracking or breaking. Further, thanks to their low weight, handling, transporting, and installing them becomes easier and thus saves on labor and equipment during vast infrastructure job sites.
Unlike other pipe materials, HDPE provides the best protection for the conveyed fluid, with interiors so smooth that friction losses are kept to a minimum and there is hardly any buildup of scale, sediment, or biofilm. This ensures interception pressure and also reduces disturbances within the pipelines due to malfunctions. This makes them a safer and more reliable type of pipeline that solves some of the challenges in such applications and meets regulatory standards; hence, these HDPE pipes are widely suitable for the gelatinization of water distribution, gas transmission, and industrial system installations.
Technical Specifications of SDR 11 HDPE Pipes
Understanding Dimensions and Sizes
SDR 11 HDPE pipes are so named using the Standard Dimension Ratio (SDR), which represents the ratio of their outer diameter to wall thickness. This ratio is directly related to the pipe’s pressure rating and ability to withstand the structural loads. For an SDR 11, the wall is nearly 1/11 of the outside diameter, making the pipe strong and suitable for high-pressure applications.
Common sizes of SDR 11 HDPE pipes have a nominal diameter range from ½ inch to 63 inches, thus accommodating a wide variety of applications. For example, a 4-inch SDR 11 pipe measures about 4.50 inches in outside diameter and has a wall thickness of approximately 0.409 inches, providing for a pressure rating at nearly 200 psi at 73°F. Both measurements adhere to ASTM International standards, ensuring that the pipe will fit well into a variety of systems with reliability.
From the perspective of material properties, HDPE is highly ductile and resistant to cracking, even under extreme temperature conditions, thus offering sufficient flexibility for a diverse range of uses. The selection of pipe sizes needs to take into account the flow rate requirements, operating pressures, installation environment, etc., to ensure the pipe will perform well and will have a long service life in its intended use.
Pressure Ratings and Performance
The materials of density and Standard Dimension Ratio give way to the pressure designation for High-Density Polyethylene (HDPE) Pipes. SDR is an inverse proportionality between pressure rating and wall thickness. HDPE pipes are manufactured and classified into typical pressure ratings, denoted by PN values, with the design working pressure in bars, subjected to a working temperature range with basis on 20°C (68°F).
For example, a pipe with an SDR of 11 will have a working pressure of about 16 bars under standard conditions, with such rating decreasing with an increase in temperature level, as is the thermal nature of the polymeric material. The elasticity and stress absorption capacity of HDPE give it water-hammer resistance, by which it withstands shock waves caused by a sudden change in flow rate—a particularly important property in hydraulic applications and settings prone to high surge pressures.
Such performance is verified via hydrostatic pressure resistance tests and fatigue tests to comply with international specifications such as ISO 4427 or ASTM D3035, which look into short-term performance and long-term durability (under sustained pressure loads). Because of its special properties to resist and withstand chemical attack and environmental stress cracking, HDPE remains the preferred material for the distribution of potable water, gas pipelines, and industrial applications where a great magnitude of durability and safety is required.
Comparing SDR 11 with SDR 17
Thicker walls characterize SDR 11 pipes, with pressure ratings set above those of the SDR 17, giving durability. In contrast, SDR 17 pipes, being thinner and lighter, work well in lower-pressure applications.
Aspect |
SDR 11 |
SDR 17 |
---|---|---|
Thickness |
Thicker |
Thinner |
Pressure |
Higher |
Lower |
Strength |
Greater |
Lesser |
Mass |
Heavier |
Lighter |
Capacity |
Lower |
Higher |
Usage |
High-pressure |
Low-pressure |
Expense |
Higher |
Lower |
Benefits of Using SDR 11 HDPE Pipes
Durability and Longevity
SDR 11 HDPE pipes are designed for very high pressures and, therefore, are often assigned a central role in critical applications. Thicker walls of SDR 11 pipes give them better mechanical strength so that they can resist external forces such as ground movements and vehicle loads without deformation. SDR 11 pipes almost have double the pressure rating compared to SDR 17 pipes, which are suitable for lower pressure applications and generally rated up to 200 psi, subject to pipe diameter.
SDR 11 HDPE piping systems have longevity as another zoning factor. Laboratory analyses and field studies have shown consistently that the material will function effectively for more than 50 years under standard operating conditions. The pipes are naturally resistant to corrosion and scaling; hence, their internal diameters remain practically unchanged over time, maintaining flow efficiency. HDPE is also molecularly resistant to environmental stress cracking, which is vital in maintaining pipe integrity under variable soil conditions and cyclical loading.
Because SDR 11 HDPE pipes perform brilliantly, they require relatively little maintenance and consequently lower life cycle costs, which are important benchmarks for infrastructure and utility projects in quest of sustainability and efficiency.
Flexibility and Ease of Installation
The freedom offered by the piping system by SDR 11 HDPE pipes that I can speak directly about is their superior flexibility compared to the rigidity of other piping systems. The pipes adjust to awkward terrain and uneven ground, thereby greatly reducing the need to fabricate special fittings or go through complex alignment procedures during installation. Besides that, being capable of bending within tight radii without risking integrity, the pipes make for quick and simple installation even in tricky or restricted building environments.
Another hugely critical advantage concerning installation is time savings and reduced labor costs. Being lightweight, HDPE pipes are easy to transport to the construction site and do not need heavy lifting equipment, often required for commonly used materials like steel or concrete. This definitely reduces the logistical nightmare and also minimizes money spent on installation, thus making the pipes most ideal for big-scale uses.
Additionally, the fusion joining technique used for connecting HDPE pipes increases the efficiency of installation and aids in the long-term reliability of the system. Methods like butt fusion and electrofusion create permanent, leak-proof joints as strong as the pipe itself. Ever secured joints reduce the chance of maintenance requirements in the future. Based on my experience, this makes SDR 11 HDPE pipes the perfect alternative for infrastructure projects where durability, quick installation, and efficiency take priority.
Corrosion Resistance and Environmental Impact
One of the main advantages of SDR 11 HDPE pipes resides in their unrivaled corrosion resistance qualities that make them long-lasting pipes for application in various industries. In contrast to metal pipes, which emanate a certain reactivity depending on whether they are acidic or alkaline in nature, HDPE pipes stand apart as being inert and non-responsive to most substances. Synthetic HDPE pipes are environmentally safe and demonstrate the credibility of being a sustainable choice. The following are five significant details about SDR 11 HDPE pipe corrosion resistance and environmental issues:
- Chemical Resistance: HDPE pipes resist chemical degradation. They can survive in contact with various chemicals, including salts, acids, and alkaline substances, thereby functioning well under chemically intensive industries.
- Non-Corrosive Material: Polyethylene, being a noncorrosive material, offers rust resistance that commonly affects other metallic pipes, especially in underground installations or underwater.
- Extended Service Life: HDPE pipes having a higher degree of endurance against environmental and chemical corrosion could survive for about 50-100 years under some well-defined operating conditions, thereby reducing installation, replacement, and maintenance costs.
- Lower Carbon Footprint: In all phases of installation and production, HDPE pipes need less energy as compared to the conventional material, thus further reducing the carbon footprint in piping life.
- Recyclability: HDPE is a recyclable material, so pipes can be recovered and reused in a harmless way after their service life, giving impetus to sustainable development.
Therefore, combining these factors, among others, proves SDR 11 HDPE pipes to be a practical solution with a deep relevance to the environment for use in various infrastructural, industrial, and environmental sectors.
Applications of SDR 11 HDPE Pipes
Industrial Piping Systems
Since SDR 11 HDPE pipes exhibit a high defensive character due to all-around protection on piping systems, industrial piping systems could never function without them. The dark bronze pipes find uses in various industries, such as chemical processing, oil and gas, power generation, and mining. These pipes hold excellent corrosion- and chemical-resistance characteristics, making them particularly suited to handle aggressive or reactive substances, such as acids, alkalis, and other corrosive chemicals, without risking leakage or material breakdown over a period.
Further, the flexibility and strength of SDR 11 HDPE pipes enable them to withstand dynamic changes in pressure and temperature that come about in an industrial environment, often occasioning other mediums of containment to yield. These pipes can handle transient pressure surges, a common occurrence in industrial processes, without losing the weakest link due to mechanical fatigue. Also, the inner surface of these pipes is smooth, which lowers frictional losses and promotes flow efficiency, thereby reducing the energy cost in pumping.
Being thermally resistant and abrasion-resistant further enables SDR 11 HDPE pipes to perform better in tough operating conditions, such as a high-temperature system or with abrasive particles carried by the flow medium. This means that they greatly contribute to the enhancement of the life span of any piping system while simultaneously restricting maintenance costs; thereby, cutting down huge expenses over time. Another advantage is that, owing to their lighter weight, even difficult or remote locations are not a challenge to transport and install them, which reduces the schedule and labor cost in general.
Water Supply and Distribution
Water supply and water distribution are among the main ingredients of modern infrastructure that provide water services to residential, commercial, and industrial establishments. The water distribution system is usually composed of a complex network of pipelines and pumping stations, reservoirs, and water treatment plants, all working together to maximize the conveyance of water. When designing and constructing any such system, many considerations are taken into account, such as daily demands for water, peak hourly demands, and potential future extension of the system.
Efficient water distribution would seek to minimize losses related to leakage from the distribution system itself. In some cases, in fact, studies indicate that up to 30% of treated water never reaches consumers because of leakages, hence the need for vigilant monitoring, maintenance, and proper implementation of leakage detection methods. More importantly, the development in materials science has provided pipes made from corrosion-resistant and highly durable materials such as ductile iron and HDPE, which further strengthen the life expectancy of distribution networks.
Smart water management is, of course, the newest innovation to penetrate the industry. IoT-enabled sensors and automated control systems can give you real-time information on water flow/pressure/water quality, thereby allowing for predictive maintenance and more flexible system operation. These innovations contribute to greater operational efficiencies, at the same time strongly ensuring that water meets quality criteria for the protection of public health and sustainability of the environment.
Gas Transportation
Efficient gas transportation is perhaps the core of modern energy infrastructure, which includes natural gas and other gaseous fuels delivered in a safe, cost-effective, and viable manner to meet the requirements of energy demand worldwide. Gas transportation systems typically operate through a network of pipelines, supported by modern technologies that provide an added dimension of survival control. High-pressure transmission forms the heart of this gas infrastructure. To avoid losses of any significant amount of energy during long-distance transmission, the transmission lines are laid at very high pressures. Depending on the environmental conditions and pressure requirements, the pipes are made of high-grade materials, such as carbon steel.
From the standpoint of transport, proper and efficient pipelines are installed and monitored. Among other things, systems of SCADA allow real-time monitoring and control over transportation, including flow, pressure, and leak detection. Through them, operators can immediately recognize, disclose, and remedy potential vulnerabilities. Apart from SCADA systems, the usage of offline inspection tools and smart pigging technologies is on the rise to maintain pipeline integrity by checking corrosion, deformation, and other anomaly occurrences.
Where transportation of gas by pipeline is not possible, LNG transportation proves to be a lucid and pragmatic solution. LNG is created by liquefying, i.e., cooling gas to very low temperatures, thereby diminishing its volume for transport by specially built cryogenic carriers. This is most useful for intercontinental gas trade, where pipeline infrastructure would be extremely limited.
In general, integration of modern technologies with a strict safety regime in gas transportation systems points toward the preservation of this business as a profitable, environmentally sustainable one.
Installation Guidelines for SDR 11 HDPE Pipes
Preparation and Tools Needed
Good preparation will ensure that each stage of SDR 11 HDPE (High-Density Polyethylene) pipe installation is done to the best quality and for a lasting service life. Before commencing installation, the following tools and materials should be ensured to be available.
- Pipe Cutting Tools: The pipe can be cut by appropriate pipe cutters or a power saw fitted with a fine-toothed blade, ideally without causing any damage or deformation to the pipe edges.
- Pipe Fusion Equipment: Fuse pipe segments together using butt fusion equipment. The equipment should be calibrated strictly as per the manufacturer’s Welding Procedure Specification for weld integrity.
- Alignment Clamps: Used to align the pipe ends accurately, thereby providing an even and strong weld during the fusion process.
- Measurement Instruments: Measuring tapes, levels, and calipers will be required to check for proper length, diameter, and alignment during the installation process.
- Cleaning Supplies: Clean the pipe ends before fusion with non-abrasive cleaning pads and isopropyl alcohol to wipe off dirt, oil, and oxidation.
- Excavation and Placement Tools: For trench-type installations, these include shovels and compactors for trench construction as per standard excavation methods and trench shields for ensuring trench safety.
- Safety Equipment: Ensure that all personnel are wearing hard hats, safety goggles, gloves, and ear protection. Also, check if the work site is hazard-free or in compliance with OSHA standards.
Such a good preparation will lead to faster installation and fewer operational failures. Combining such preparation with thorough knowledge of industry standards means a robust and efficiently running SDR 11 HDPE piping system.
Step-by-Step Installation Process
- Worksite Preparation: Start by verifying that the trench complies with OSHA standards for depth and slope, ensuring the site is safe for excavation and pipe installation. Remove all debris or obstacles from the worksite that could damage the installation.
- Inspection of SDR 11 HDPE Pipes: Conduct inspections of pipes for visible damages like cracks, warping, or weaknesses. Check that pipes satisfy diametric, wall thickness, and quality requirements as per ASTM specifications.
- Welding and Joining of Pipes: Join pipes with electrofusion or butt fusion methods. Prepare and calibrate all fusion machines, ensuring clean surfaces and correct temperatures (usually between 400°F and 450°F) to make a strong and lasting weld.
- Laying of Pipes in the Trench: Lay the welded pipe gently into the trench by ensuring the use of suitable lifting equipment to prevent stress on the joints. Place the pipes with very minimal bending and a uniform slope according to design specifications.
- Pressure Testing: Test hydrostatically or pneumatically to ensure the system’s integrity is being upheld. Raise the pressure slowly to the test pressure level and maintain it for the time recommended, so leaks or weaknesses can be observed.
- Backfilling of the Trench: Start by backfilling using fine granular material considered free of any sharp objects to protect the pipes. Compact the material in layers, making sure that they are stable with no space that would equally compromise their integrity.
- Final Inspection and Quality Assurance: Conduct a thorough review of the entire installed system to guarantee compliance with engineering plans and quality standards. Document the process, eliminating all records of flaws. This shall be done before initiating operation of the system.
Since this detailed process is followed, one can imply that the system is installed efficiently and safely, thereby reducing the risk of any failures faced in operation in the future.
Best Practices for Optimal Performance
Here are some of the good practices for installation and operation to ensure the ideal performance of SDR 11 HDPE piping systems:
- Material Handling and Storage: Do not stack HDPE pipes on an uneven or unstable surface; also, they should be protected from extended direct sunlight that may alter their material properties. Do not drag pipes on rough ground surfaces to lessen the chance of scratches or gouging that could impair durability.
- Correct Procedure of Pipe Fusion: Use certified fusion equipment with the procedures recommended by the equipment manufacturer for butt fusion and electrofusion methods. Ensure that the fusing temperature is proper, and the alignment will give you a good joint that is strong and leak-proof.
- Pressuring of the System: Pressure testing can be hydrostatic or pneumatic pressure testing. It would ensure the lining from damage in case of sudden application of pressure after installation, with the leakage or weakness detected at lower pressure.
- Regular Monitoring and Maintenance: Set up a preventive maintenance system that calls for periodic inspection of all critical joints and fittings. Consider expansion, pressure surges, or any external damages very seriously to avoid any surprises from failure.
- Adherence to Industry Codes and Standards: Follow codes and standards applicable, such as ASTM F2620 for fusion procedure or ISO 4427 for HDPE pipes, and duly get the procedure in written form to meet regulatory requirements and ease future maintenance or upgrades.
Undoubtedly, assimilating the best practices, practice of the latest advancements in the industry, and keeping guidelines under constant review will surely provide a boost to the reliability and efficiency of SDR 11 HDPE piping systems over a longer life span.
References
Frequently Asked Questions (FAQ)
Q: What are the standard dimensions of SDR 11 HDPE pipes?
A: The standard dimensions of SDR 11 HDPE pipes include a range of nominal diameters that typically vary from 20 mm to 1200 mm. The outside diameter and wall thickness are designed according to the pressure ratings and applications specified by ISO 4427.
Q: What is the pressure rating for SDR 11 HDPE pipes?
A: SDR 11 HDPE pipes are designed to withstand high-pressure applications, with a typical pressure rating of 160 psi. The pressure in bars tthat he pipe supports can vary based on the outside diameter and wall thickness.
Q: How do SDR 11 HDPE pipe dimensions compare to other SDRs?
A: SDR 11 pipes have a lower dimension ratio compared to SDR 17 pipes, meaning they have thicker walls and can handle higher pressures. This makes SDR 11 suitable for applications requiring higher pressure ratings.
Q: What materials are used to manufacture SDR 11 HDPE pipes?
A: SDR 11 HDPE pipes are primarily manufactured from high-density polyethylene (HDPE), specifically grades such as PE100 and PE80, which offer excellent mechanical properties and UV resistance.
Q: Can SDR 11 HDPE pipes be used for potable water supply?
A: Yes, SDR 11 HDPE pipes are suitable for potable water applications. They are designed to meet the requirements for safe drinking water and are often certified for this use by third-party organizations.
Q: What are the common applications for SDR 11 HDPE pipes?
A: SDR 11 HDPE pipes are commonly used in various industries, including water supply, oil and gas, and chemical transportation. Their flexibility and resistance to corrosion make them ideal for a wide range of applications.
Q: How is the installation of SDR 11 HDPE pipes typically performed?
A: The installation of SDR 11 HDPE pipes often involves methods such as butt fusion welding, which ensures reliable performance and strong joints. Proper fitting of the pipes is crucial to maintain their pressure rating and functionality.
Q: What is the significance of the wall thickness in SDR 11 HDPE pipes?
A: The wall thickness of SDR 11 HDPE pipes is critical as it determines the pipe’s ability to withstand internal pressure and external loads. A thicker wall enhances the pipe’s strength and durability, making it suitable for high-pressure applications.
Q: How does the density of the material affect SDR 11 HDPE pipes?
A: The density of high-density polyethylene used in SDR 11 HDPE pipes contributes to their strength, flexibility, and chemical resistance. Higher density materials enhance the pipe’s ability to withstand different pressures and environmental conditions.
Q: What testing standards do SDR 11 HDPE pipes comply with?
A: SDR 11 HDPE pipes comply with various ASTM and ISO standards, ensuring they meet rigorous quality and performance criteria. These standards help specify the physical properties and performance requirements of the pipes in different applications.