High-density polyethylene (HDPE) pipes have revolutionized modern piping systems due to their durability, flexibility, and efficiency. Among the various types of HDPE pipes, SDR 11 is a commonly used classification that offers a robust balance between strength and pressure capacity. SDR, or Standard Dimension Ratio, determines the pipe’s wall thickness about its diameter, and SDR 11 represents a specific ratio vital for applications requiring high-pressure handling. This guide provides a comprehensive analysis of HDPE SDR 11 pipes, detailing their construction, technical specifications, key advantages, and applications across industries.
What Are the Related Products for HDPE SDR 11 Pipe?
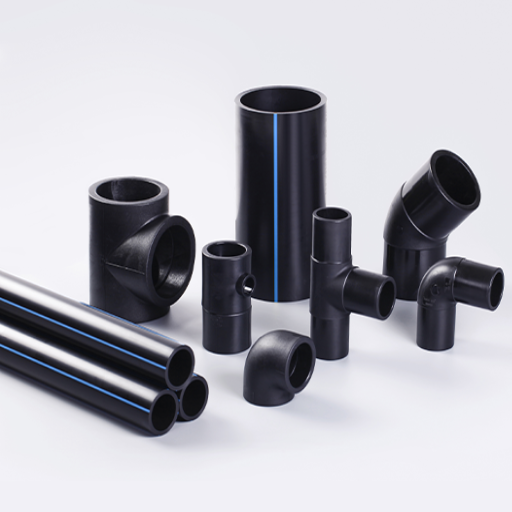
Exploring HDPE Pipe Accessories
While looking for a accessories to use with the HDPE SDR 11 pipes, there are a few competitve choices that will allow for effortless integration. The primary accessories consist of fusion fittings, electrofusion couplers, flange adapters, and pipe saddles.
- Fusion Fittings: The very definition of these fittings is these fittings establish a reactively tight connection that is not prone to leakage through the employment of fusion methods. These fittings are most suitable for high-pressure systems and are used for joint construction.
- Electrofusion Couplers: These couplers are specific for high working pressures and applied these couplers have wires with spin heating elements embedded in the insulation of the pipe bits for provision with consideration of the fusion bit.
- Flange Adapters: These are used in transitions from HDPE pipe systems to systems with other pipes or equipment. They are largely used on the flanges in industrial applications and waterworks.
- Pipe Saddles: Pipe Saddles are great for direc branch connections, these fittings are bolts that are then clamped to the surface of the pipe to create free flow holes without ruins the pipe integrity.
He accessories must be consistent with the outer diameter of the pipe, pressure rating, system factors, and application to commensurate system operation and security.
Understanding Polyethylene Pipe Compatibility
To assess polyethylene pipe compatibility and its interrelations effectiveness, the following attributes must be evaluated so the system functions properly over time: functionality integrity, safety, and longevity. For example, I would start by checking if the volumetric strain of the pipe material meets the estimated operational pressure system. To determine this, the pipe’s pressure rating (PR) should equate to, or be greater than, the pressure class specified by the application. The common pressure ranges for polyethylene pipes are usually between 4 bar (58 psi) and 20 bar (290 psi), which depend on the grades of pipes, such as PE80 and PE100, as well as the wall thickness.
Another crucial measurement required to ensure proper fitting connections is the outer diameter (OD). A good example is PE pipes featuring an SDR of 11. While they tend to be more rigid and much more likely to withstand greater pressures than SDR 17 pipes, they are not as flexible.
Lastly, considerations should be made on the surroundings, including the pipe material, the temperature extremes, and UV radiation as well as the chemical makeup of the media which will be conducted. Polyethylene is more delicate due to the increased temperatures, where the operating conditions in all likelihood need to be restricted to 60°C.
Aligning with these guidelines will guarantee compatibility across fabricated components and accessories needed to fulfill operational objectives.
Choosing the Right Fusion Machines
While picking a fusion machine, I consider several factors to ensure they fit the particular application and pipeline. These machine features include compatibility with the material of the pipe, operating temperature, and pressure range. For example, while operating with high-density polythene pipes, I make sure the fusion machine provides adequate heating and alignment for butt fusion or electrofusion techniques.
- Operating temperature range: The machine should be able to operate within the fusion technical requirements of 400°F-450°F or 204 °C-232 °C for HDPE pipes, to adequately bond the joints.
- Pressure settings: There should also be adjustable pressure control features that ensure a uniformly strong fusion while avoiding damage to the pipe material.
- Power supply requirements: The unit’s voltage and wattage rating also has to match with the available power source at the worksite which ranges from 120V to 240V and above.
- Automated features: These modern features enhance the repeatability and accuracy of the welding process, which is very important for industrial purposes.
- Pipe size compatibility: The machine should be rated for the pipe diameter range that needs to be welded, e.g., from 1 inch to 63 inches mating surfaces is available to the machines.
Keeping these technical requirements in mind, I can suggest a fusion machine that allows for dependable joint functioning over time and under operational conditions with a high level of assurance.
How to Address Common Installation Challenges?
Common Installation Errors and Solutions
Based on my experience, the loosest possible machine error is two sides of a pipe being aligned in a fusion process. Sloppy alignment of pipes can cause pore joints and a potential failure of the entire system. Because of this, I double-check that the machine’s alignment clamps are positioned properly and that the pipe is rigidly fixed in the clamps at the beginning of the process. For instance, some fusion machines have and industry-acceptable slack of greater than 10% of the thickness of the wall of the pipe open to misalignment and still be fusion capable.
Another category of issue is that fusion can be absent if there is not enough time for heating. This problem can be solved by following the recommended heating cycle preset by the manufacturer due to the size and material of the pipes. HDPE pipes with a diameter of ten inches have to be superheated for an estimated time of 180-220 seconds to ensure melting and fusing quality atthe temperature.
To sum up, maintaining cleanliness at the ends of pipes or the heating plate is another persistent challenge that I have faced many times. Even the smallest particles of dirt on the pile surfaces may weaken the bond. My approach to solving this problem is to clean the ends of the pipes and the heating plate in great detail and inspect every surface for dirt, grease, or moisture before each welding cycle.
There is no doubt that with proper adherence to the technical instructions, the installation processes will improve in quality and reliability with every new cycle.
Ensuring Proper Fusion Techniques
To make sure I use the right fusion techniques, I do the following:
- Control of Temperature: I work with the heating plate set to a temperature which does not exceed 450 degrees Fahrenheit or drop below 400 degrees Fahrenheit. This is the recommended operating temperature range. Heating plates set above or below these values risk over or under heating the material which will ultimately ruin the quality of the joint being made.
- Control of Time: The time during which the heating is done is calculated based on the type and diameter of the pipe being worked on. As an example, pipes made from polyethylene usually need to be heated for a duration related to the thickness of the walls of the pipe to allow melting to take place without overheating.
- Application of Pressure: During the process of achieving fusion, I follow the guidelines given by the manufacturer regarding the amount of pressure that needs to be applied consistently (for instance, 60 to 90 psi for HDPE pipes where the specific pressure to be used depends on the size of the pipe). This confirms that the interface has been fused correctly without having air or gaps in between them.
- Period of Cooling: I make sure to give enough time for solidifying of the material under pressure prior to releasing my grip. Releasing the grip too soon can lead to an internal weakness at the joint space.
- Preparation of Surfaces: I do a careful examination and cleansing of all surfaces before fusion to get rid of contaminants like dirt and moisture as well and oil. If steps are not followed, there is a likelihood of creating loose joints, which will then lead to a loss of strength and reliability of the joint.
When I follow these technical requirements with discipline, I guarantee that the fusion joints are intact and I obtain consistent results of superior quality for all installations.
Preventing Corrosion in HDPE Pipes
Even though HDPE (High-Density Polyethylene) pipes are not metallic in nature, and thus are not prone to corrosion damages, there are some corrosion measures I take to ensure reliabilility and longevity while various operational conditions are applied.
- Material Selection: The specific resin of HDPE utilized has to be to a compatible standard, for example, ASTM D3350, that specifies the strength, flexibility, and oxidative degradation resistance of the material. Otherwise, the pipe material will not maintain its needed anti-corrosive properties.
- Protective Coatings: Even though HDPE pipes will not rust or corrode like metallic pipes, if the HDPE pipes are used in extremely chemically reactive environments, I check to see if any external protective coatings are applied, as those will provide greater strength and durability.
- Seamless Fusion Joints: Homogeneous joints that are created using appropriate fusion techniques such as butt fusion or electrofusion are known to create leak proof joints. These joints are also corrosion resistant as they do not contain any contaminant or moisture ingress points due to being sealed.
- Oxidation Resistance: Protection from oxidative or ultraviolet deterioration is further guaranteed by in conjunction with compliance with ISO 4437 standards, the use of Antioxidants or UV stabilizers are employed in the manufacturing are used in the construction of the used pipes.
- The Checkups Before Installation: I begin with the working conditions, such as the land’s soil type, average temperature, and any chemical exposures, and use this data to specify the pipe to be used. This incorporates choosing HDPE grades that are more resistant to certain corrosive materials and are corrosion-resistant themselves.
Following these factors during every step performed throughout the installation enables me to provide the HDPE piping systems with superior resistance to corrosion so that they can function effectively, remain structurally sound, and do so over a long service life.
What are the Key Category Benefits of HDPE SDR 11 Pipe?
Advantages of High-Density Polyethylene
The unique features of high-density polyethylene (HDPE) make it so that its use as a piping material is simply unavoidable, especially in harsh conditions.
- Great Corrosion Resistance: One of the advantages of HDPE is that it does not react with a great number of chemicals, including acids, bases, and many salts. This resistance is because of its non-polar molecular structure, which reduces its likelihood of being corroded.
- Strong and Long-life: HDPE pipes, under the right conditions, can be expected to serve well for over 50 years, demonstrating an excellent strength-to-weight ratio along with fatigue resistance. This is likely to lower the maintenance costs in the long term.
- Flexibility and Impact Resistant: High flexibility of HDPE pipes reduces chances of breakage due to ground movements or slow cyclic loading. This property, combined with other factors, makes such pipes ideal for regions with seismic activities or areas with shifting soils.
- Enhanced Hydraulic Efficiency: The smooth surface of the interior of HDPE pipes, having a very low friction coefficient (Manning’s roughness coefficient of 0.009), leads to minimum energy losses and maximized fluid transfer.
- Leak-Proof System: HDPE pipes are normally connected through heat fusion methods such as butt or electrofusion welding. When properly installed, these joints create a solid monolithic system with no leaks.
- Pressure Resistance: For SDR 11, the pipe’s design corresponds to a pressure rating of 160 psi (PN 10.9), which confirms that the material is suitable for medium to high-pressure applications without structural failure.
Overall, these technical requirements guarantee that HDPE SDR 11 installations are reliable for a wide range of engineering and industrial uses.
Benefits of Resistance to Corrosion
The resistance to corrosion in HDPE SDR 11 pipes provides numerous advantages, especially in harsh industrial and environmental conditions. In contrast to metal pipes that tend to rust and corrode with time due to moisture and chemical exposure, HDPE pipes do not lose their integrity from corrosive agents. This ensures that there is no deterioration in performance over time, especially in instances where reactive materials such as acids, bases, or salts are frequent.
From a technical point of view, HDPE has a high degree of chemical inertness allowing for a wide range of pH values (about 1 to 14) without damaging the material’s strength. This means no additional protective linings or coatings are required which reduces maintenance costs and service life. Furthermore, non-corrosive nature of HDPE pipes improves flow efficiency as they do not corrode internally like metallic pipes.
Incorporating the SDR 11 design further improves the pipes’ strength by having thicker walls about their diameter, improving durability under chemical attack and high operating pressures of 160 psi. Overall, these features make HDPE SDR 11 pipes an economical option for transporting fluids in corrosive environments.
The Role of SDR 11 in Pipe Performance
SDR (Standard Dimension Ratio) represents the ratio of the outer diameter of the pipe to its wall thickness. For 11 SDR pipes, a robust wall means a relatively thick wall to the diameter, which increases strength and reliability to operational stresses.
- Operating Pressure: SDR 11 pipes have a maximum working pressure that can reach 160 psi. This capability is crucial for performing applications which require high pressure without the damaging the pipe.
- Wall Thickness: The greater resistance of SDR 11 pipes to mechanical stress and soil movement or external loading is attributed to the increase in wall thickness of these pipes.
- Chemical Resistance: The combination of high-density polyethylene (HDPE) and the SDR 11 configuration increases resistance to abrasive and corrosive chemicals, making the pipes appropriate for a wide range of industrial and municipal uses.
- Durability and Longevity: Long term durability is expected with the combination of thick walls and the inherent characteristics of HDPE due to repeatedly challenging conditions of changing temperatures, chemicals and high external pressures.
Keeping an SDR 11 ratio ensures that the operational and structural functioning of the projects is met, making them ideal for use in SRSD critical infrastructure projects. This type of design is cost-effective because it assures maximum efficiency over a longer life cycle while guaranteeing dependable fluid transfer.
How to Read the Product Description of HDPE SDR 11 Pipe?
Decoding SDR 11 HDPE Specifications
To be able to comprehend the product description of HDPE SDR 11 pipe, few important technical requirements need to be studied carefully to guarantee proper use and effectiveness.
- SDR (Standard Dimension Ratio): The thick wall pipe structure capable of enduring higher internal pressures in comparison with pipes of higher SDR value is an SDR 11 pipe. This is because the SDR 11 categorization specifies outer diameter of the pipe to be 11 times the pipe wall’s thickness. This is why an SDR 11 pipe is most appropriate for the transfer applications of high-pressure gas or fluid.
- Pressure Rating: The pipe’s diameter and grade (PE4710 or PE100) determine the SDH 11 HDPE pipe’s pressure rating which rests between 160 to 200 psi. This rating ensures reliable performance during demanding conditions.
- Wall Thickness: For pipes with SDR 11, wall thickness is proportional to pipe diameter. As an illustration, a 6-inch SDR 11 pipe provides necessary structural integrity for having approximately 0.545 inches wall thickness.
- Standards of the materials: Like with most things, there are standards to follow when creating pipes, such as the HDPE SDR 11 . These provide assurance that the pipes will function and last for a long time while resisting breaking down chemically.
- Application: The superior strength-to-thickness ratio makes SDR 11 HDPE pipes a preferred choice in water distribution, gas pipelines, industrial usage, and even sewers cyclically. These pipes, along with other critical infrastructure components, are essential as they can withstand higher pressures and environmental stresses.
Through a rigid analysis of these aspects, users can easily establish whether SDR 11 HDPE pipes are compatible with their requirements while making sure that operational pressures and legislations are met.
Understanding 200 PSI Ratings
A container, with a 200 PSI rating, means that it is capable of operating with an internal pressure of 200 pounds per square inch and will cope with a certain amount of stress. This rating must be observed in working pipes for water distribution, gas distribution, and for industrial piping systems which have high pressures as it determines the reliability of a pipe.
- Wall Thickness: For SDR 11 HDPE pipes, the pipe’s wall should not let the structure go under deformation or failure while coping with 200 PSI internal pressure; it must ensure structural integrity.
- Material Strength: The construction material of the pipe has to be high density polyethylene (HDPE), which has to meet or exceed the minimum requirements for tensile strength and durability to resist long term creep and fatigue, ensuring proper resistance.
- Temperature Resistance: 200 PSI-rated HDPE pipes must be able to operate at the allowable temperature ranges, which are 140° F (60° C) for continuous service, as having to cope with thermal stress can dampen the ability to relieve internal pressure.
- Design Factor (DF): This is a value that is frequently predetermined to avoid operating a pipe at negative margin conditions. This is most commonly set at 0.5, allowing an additional margin of safety of variable conditions during pipe operation.
- Cyclic Loading Tolerance: The pipe has to be able to withstand multiple cycles of pressurization and not lose structural integrity for it to be used.
Compliance with the norms like ASTM D3350 and the Pressure Rating Index from PPI TR4 need attention when evaluating SDR 11 HDPE pipes designed for use in 200 PSI-rated systems.
How Can You Ensure Proper Size and Fit for Your Project?
Choosing the Right IPS Size for Installation
In order to find the pipe’s SDR (Standard Dimension Ratio) rating, I check the system’s working pressure against requirements in documents such as ASTM D3350 and PPI TR4. For a system rated at 200 PSI, an SDR 11 HDPE pipe is suggested because its wall thickness relative to stress over a given time is quite reasonable.
- Flow Rate Requirements: The efficiency of the system is directly proportional to the internal diameter of the pipe and the number of cubic feet per second (CFS) or gallons per minute (GPM) needed.
- Pressure Rating (PR): SDR 11’s ability to withstand 200 PSI maximum working pressure can be easily achieved by the pipe as it is designed under standard conditions.
- Temperature Range: The performance of an HDPE pipe is affected by the temperature. As it is proposed for installation for regions with changing climates, it has to be temperature derated for long term reliability.
These factors help me determine the desired IPS size of the pipe so that it can be integrated into the project design with little chance of misfit or malfunction.
Determining Flow Rates and Pressure Needs
To establish the operational requirements needed to calculate flow rates and pressure requirements for the HDPE pipe system, specific flows need to be evaluated. These include, but are not limited to:
- Flow Rate (Q): The flow is calculated volumetrically using the equation Q=A×V where A is the area, which equals π times radius squared, and V is the flow velocity. There is a requisite flow rate that needs to be met based on the system’s operational needs and predefined project requirements so that the required performance can be achieved.
- Operating Pressure (P): The pressure rating of the HDPE pipe has to be higher than the operating maximum pressure of a system, which includes parameters like static pressure and surge pressures from flow changes. Depending on material grade and wall thickness, pressure ratings for HDPE pipes can range from 50 psi to 250 psi.
- Pipe Diameter and Thickness of the Wall: With the Hazen-Williams equation or the Darcy-Weisbach friction factor, it is noted that friction losses are proportional to internal diameter, roughness coefficient of the pipe and flow speed. Designing a pipe configuration with strong energy loss will achieve optimal hydraulic efficiency.
- Effects of Temperature: Changes in temperature influence flow rate and pressure handling capabilities. If a system is to function within exceptionally hot or cold conditions, derating factors must be applied to pressure ratings in order to operate outside standard design constraints.
It is feasible to adjust these factors in conjunction with project specifications in such a way that allows a pipe system to be designed for uniform flow while simultaneously reducing the chances of pressure problems.
Reference sources
Frequently Asked Questions (FAQs)
Q: What is an HDPE SDR 11 pipe?
A: An HDPE SDR 11 pipe is a high-density polyethylene pipe with a standard dimension ratio of 11. This means the pipe’s outer diameter is 11 times its wall thickness, providing a balance of strength and flexibility. It is commonly used for potable water, reclaim water, and raw water and waste water applications.
Q: How is the SDR 11 pipe used in geothermal applications?
A: SDR 11 pipes are used in geothermal applications due to their durability and resistance to environmental stress. They efficiently transfer heat and can be installed in thousands of feet of pipe, making them suitable for large geothermal projects.
Q: What are the shipping options for SDR 11 HDPE pipes?
A: Shipping options for SDR 11 HDPE pipes can vary depending on the supplier. Charges are typically calculated at checkout, and freight options are available to accommodate large orders, ensuring that pipes are delivered efficiently and securely.
Q: Are HDPE SDR 11 pipes available in various diameters?
A: Yes, HDPE SDR 11 pipes are available in various diameters, allowing for customization based on the specific needs of a project. This ensures that they can be used for a range of applications, from potable water to ranch water projects.
Q: What are the benefits of using IPS SDR11 PE4710 Black HDPE pipes?
A: IPS SDR11 PE4710 Black HDPE pipes offer numerous benefits, including high resistance to corrosion, chemical resistance, and the ability to withstand high pressure. They are widely used for potable water systems, reclaim water, and intake water due to their durability and efficiency.
Q: What are some suitable applications for SDR11 HDPE pipes?
A: Suitable applications for SDR11 HDPE pipes include potable water supply, geothermal systems, reclaim water, raw water and waste water management, and ranch water projects. They are versatile and can be used in a wide range of industries due to their strength and flexibility.
Q: Are there any warranties provided for SDR11 HDPE pipes?
A: Warranties for SDR11 HDPE pipes can vary by manufacturer. It is important to check with the supplier regarding warranty terms, which typically cover defects in material and workmanship for a specified period.