High-density polyethylene (HDPE) pipes have become a pivotal component in modern infrastructure, providing unmatched durability, flexibility, and resistance to corrosion and chemical degradation. The SDR (Standard Dimension Ratio) system, which defines the relationship between a pipe’s outer diameter and wall thickness, is fundamental in determining an HDPE pipe’s structural integrity and pressure capabilities. This article focuses specifically on HDPE SDR 11 pipes—one of the most robust standard options—highlighting their detailed dimensions, material properties, and performance under various operational conditions. Additionally, we explore their widespread applications across industries ranging from water supply systems to gas transportation and beyond, offering a technical framework for understanding and leveraging these conduits in diverse engineering projects.
What are the key specifications of HDPE SDR 11 pipes?
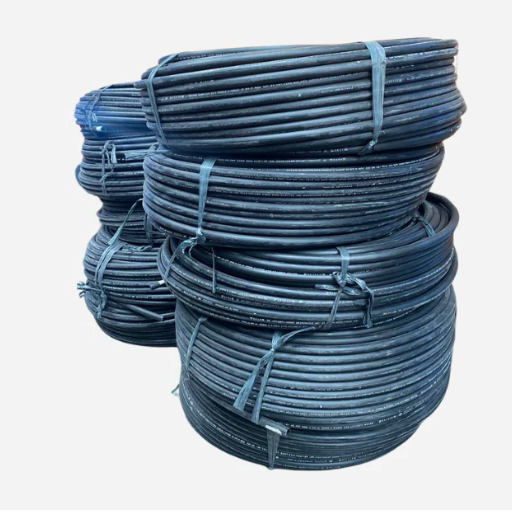
Material properties and pressure ratings
I am certain about the pressure ratings and material properties of HDPE SDR 11 pipes. Their dimensions have been defined by strict operational requirements. The pipes are also incredibly flexible and highly resistant to chemicals, thanks to the high-density polyethylene HDPE raw material used to produce these pipes. The quality of HDPE used in the SDR 11 pipes usually conforms to ASTM or ISO grade, thus ensuring its structural integrity and uniform quality.
The pressure rating of an SDR 11 pipe is defined by its Standard Dimension Ratio, which indicates the relation between wall thickness and diameter meant for internal pressure. SDR 11 specifically indicates that the pipe has thicker walls compared to pipes with higher SDR numbers, which means a higher working pressure. For instance:
- Maximum operating pressure at 73°F (23°C): 200 psi (13.8 bar) for water applications in compliance with industry standards.
- Tensile strength: 3200 to 3500 psi.
- Thermal performance: Up to 60°C (140°F), stress factors will affect performance.
For these reasons, SDR 11 pipes are easily utilized for high gas-pressure transportation and municipal water supply systems as well.
SDR 11 pipe performance in various applications
SDR 11 pipes perform exceptionally in numerous industrial and municipal applications thanks to their unique structural and thermal attributes. For water supply systems, these pipes are capable of supporting a maximum operating pressure of 200 psi and 73 F (23 C) ensuring proper performance functionalityand “standard” usage conditions. Their tensile strength ranging between 3200 and 3500 psi also compliments supporting heavy-duty scenarios enabling long service life.
For gas transportation, SDR 11 pipes are preferred out of all options due to their thermal resistance ranging up to 140 F (60 C) along with high-pressure tolerance. Adherence to industry standards set for pressurized gas systems ensures dependable and safe working conditions. While some stress factors like long exposure to high temperatures could marginally impact their performance, their compliance to moderate temperature levels guarantees satisfactory results.
It is important to remember, when selecting SDR 11 pipes for certain conditions, that the operating pressure and temperature compatibility along with stress factors must pass the application requirements. Such heavily technical specifications easily justify the use of SDR 11 pipes in diverse municipal infrastructure and industrial fluid transfer systems.
How are HDPE SDR 11 pipes used in different industries?
Water supply and sewage system applications
High-density polyethylene (HDPE) SDR 11 pipes are determined to have high durability and resistance which makes them frequently used in water supply and sewage systems. The corrosion, pressure-raising ability, and chemical reaction resistance of the pipes are the bane of their existence.
- Pressure Rating: SDR 11 pipes are known to maintain a pressure rating of up to 200 PSI. This makes them reliable for use in high-pressure water distribution networks.
- Temperature Tolerance: These pipes can withstand a temperature range from -40°F to 140°F, these pipes help them befit different climatic conditions.
- Longevity: The composition of HDPE grants these pipes a whopping life expectancy of over 50 years, especially under constant operating conditions.
- Leak-Free Joints: Installation of the pipes through fusion welding results in seamless joints which reduces the chances of leakage in both water supply and sewage systems.
- Chemical Resistance: HDPE SDR11 pipes are highly resistant to sediment building, acids, bases, and other aggressive compounds found in sewage environments.
The above-stated properties of SDR 11 pipes make them the best for municipal water supply systems and wastage drains and treatment plants.
Gas distribution and industrial pipeline systems
Pipes made of Polyethylene with a standard dimension ratio or HDPE SDR 11 are extensively used in the gas distribution industry and other industrial pipeline systems due to their excellent capabilities in difficult working environments. Such pipes withstand tremendous amounts of pressure while enduring environmental stress cracking. Such capabilities guarantee the safe transport of natural gas along with other gaseous fuels. They are also capable of fusion welding, doing so creates joints that do not leak, the do not compromise the integrity and safety of the system.
- Pressure Rating: Regarding usage and applicable standards, HDPE SDR 11 can be used with pressures of 160 psi for some governed applications.
- Temperature Range: -40 F to 140 F is the operational range for these pipes and therefore can be utilized in many industrial and environmental applications.
- Durability: Under normal working conditions, the powerful structure of the material guarantees a life span of over 50 years.
- Flexibility: HDPE requires very few fittings due to its powerful structure, making it easy to install them in expensive layouts and ensuring cost-effective installations.
These criteria support the conclusion for extensive use in primary gas distribution systems as well as in gas which is used for industries where reliability, safety, and long-term goals cannot be compromised.
What are the advantages of using HDPE SDR 11 pipes?
Durability and resistance to environmental factors
The structure and functionality of HDPE SDR 11 pipes make them very useful since their resistance and durability are exceptional. I can confidently say that it can survive harsh enforcement. Their resistance to chemical corrosion, even when exposed to aggressive substances such as acids, bases, and salts, makes them ideal for demanding applications. As a bonus, HDPE SDR 11 pipes are highly resistant to UV rays, UV radiation, extreme temperatures, and even stress-cracking—one of the requirements in harsh conditions.
- Chemical Resistance: It assures integrity in chemical and industrial business operations as it is non-reactive to HDPE most chemical substances.
- Thermal Performance: The pipes reliably function from -40°F to 140°F and get extreme conditions without breaking down.
- UV Resistance: Ultraviolet-caused HDPE aging is effectively dealt with by built-in stabilizers.
- Flexural Strength: It helps pipes manage high stress by compromising the structure’s stability and maintaining its elasticity.
Therefore, my stance that HDPE SDR 11 is the most reliable solution there is for all industrial and environmental uses is reassured by all the previously listed properties.
Cost savings and installation efficiency
Because of their features and technical advantages, HDPE SDR 11 pipes save money and time in installation. Their lightweight nature alone saves significantly on transportation and handling, especially in large-scale projects. Furthermore, the fusion welding process used on HDPE pipes makes connection maintenance-free over time. Their flexibility during installation allows for simple maneuvering around obstacles, thus eliminating the need for expensive fittings and reducing labor in more complex tasks.
- Density (0.94–0.96 g/cm³): Ensures durability while remaining lightweight.
- Flexural Modulus (900 MPa): Has enough flexibility for trenchless installation procedures.
- Thermal Expansion Coefficient (1.5-2.5 x 10⁻⁴/°C): Lowers the chances of varying temperature stress fractures.
- Joint Integrity (Fusion Welding): Seamless and dependable systems are achieved guaranteeing lower repair and many operational costs.
These advantages illustrate how HDPE SDR 11 provides a nearly complete maintenance system and why its use is economical in the end.
Long-term performance and minimal maintenance requirements
The reliability of HDPE SDR 11 pipes is proven in real-world applications, and its long-term performance can be credited to a multitude of factors: It is Low in Operational and Environmental Stress HDPE SD11 pipes have high endurance against freak operational and environmental conditions, which means they can withstand a lot of stress.
- Creep Resistance: HDPE’s molecular structure does not allow much deformation over time which lessens the probability of pipe rupturing due to stress.
- Chemical Resistance: SD11 pipes have exceptional strength against most industrial or wastewater chemicals as well as acids and alkalis which ensures their minimal degradation over time.
- UV Stability (with Carbon black Addition): Enhanced carbon black allows above-ground installation under direct sunlight without fear of pipe damage Deteriorating the integrity of the pipes.
- Expected Lifespan (>50 years): SD11 pipes are durable due to high-quality polymer composition and robust design, which means their operational life is bound to be over five decades.
- Low Leak Risk (Fusion Joints): Electro Fusion or butt fusion joints reduce the chances of welded joints leaking which is much more common with traditional gasket joints.
In summary, these features of HDPE SDR 11 systems promote reduced upkeep, elongated service periods, and increased cost benefits for infrastructure projects.
How do you select the right HDPE SDR 11 pipe for your project?
Factors to consider when choosing pipe dimensions
While determining the right dimensions of the pipe for your project, you will need to evaluate various aspects to ensure proper fit and function:
- Flow Requirements: I check for maximum flow rate and pressure so that I can figure out the internal diameter needed. For example, if you are working with high-flow applications, larger diameters (e.g. 6-inch or 8-inch) are more helpful. Smaller diameters (e.g. 2-inch or 3-inch) work fine with lower-flow systems.
- Operating Pressure: I review the pressure rating of the HDPE SDR 11 pipe which usually has a pressure rating of 200 psi at 73°F. This means that the selected diameter aids as a factor of the system’s demand for pressure without being a safety risk.
- Environmental Conditions: I take into consideration soil type and UV rays for selecting wall thickness and outer diameter of the pipe to provide durability over time.
- Installation Method: I think about whether the project is conducted with trenchless installation, direct burial, or above-ground placement. For the trenchless method, specific outer diameters are a must to optimize boring equipment and reduce friction during insertion.
- Maintenance and Expansibility: I consider future maintenance tasks and any possible expansion the system can go through. If operations need scaling up, larger diameters are a must to reduce the cost of the project over its entire lifecycle.
By studying every tiny detail, I can choose sizes that fit both the requirements and the operational limits, thus maintaining system efficiency and reliability.
Matching SDR 11 specifications to project requirements
To align the specs of the SDR 11 to the project requirements, first I check the pressure and flow rate needs of the system. SDR 11 pipes are built to withstand high internal pressures, which is why they have a standard dimension ratio. For example, they tend to have a norm of about 160 psi for room temperatures when it comes to conventional PE materials. This is crucial for applications that require high-pressure fluid transmission.
Next, I check how well the material will work with other substances. SDR 11 polyethylene pipes can withstand a majority of chemicals, which makes them ideal for industrial and municipal use, especially where corrosion is often present. I do this by checking the pipe’s technical datasheets and matching them with the specific chemical environment.
In addition, I look at the installation conditions. For trenchless installations where external loads or impact are in play, SDR 11 pipes are thick enough to ensure structural integrity. For above-ground systems, I check if the material is UV-resistant to ensure longevity.
Lastly, I think about future scalability. SDR 11 pipes offer strength and a wide range of uses at the same time. Their inner diameter provides for enough flow capacity and permits some moderate performance expansion without huge setbacks in key performance indicators. These characteristics can be aligned with technical requirements so that precise and dependable project demands can be met.
Consulting with professionals for pipe selection
As much as the professionals value my opinion on their selection of pipes, I ensure that each technical specification relates to the project, starting from the compatibility of the piping materials. Such as checking whether polyethylene is suitable because it has excellent resistance to different types of chemicals like acids and bases.
I then focus on the installation requirements, which are also physical conditions. For trenches that require minimal ground disturbance, I check whether the pipe has the minimum wall thickness of SDR 11, to confirm that it is still usable. For above-ground uses, I check the manufacturer’s certifications for UV stabilization parameters to ensure material performance under the sun for a long time.
Then I look into operational aspects like temperature and pressure ratings. Just to provide an example, SDR 11 HDPE pipes have a maximum pressure rating of 200 psi at 73 degrees Fahrenheit but can get relatively higher with the retention of specific de-rating components set by the manufacturer.
Finally, the flow capacity and anticipated future demand address scalability. I determine the flow rate through the pipe using the stated internal diameter of the pipe and the anticipated pressures within the system. The design is shaped in a way that while achieving maximum levels of flow velocity, the energy consumption and efficiency levels will not be jeopardized.
What installation methods are used for HDPE SDR 11 pipes?
Butt fusion and other joining techniques
Butt fusion has earned the top spot as the most common joining technique of HDPE SDR 11 pipes, as it is the most reliable and yields a homogenous joint. The process consists of setting the pipe ends in alignment, heating them with electrically heated plates to a temperature between 400°F and 450°F, and fusing them. The ends are pressed under controlled pressures for a strong bond, free from leaks. Particular care must be taken on surface preparatory processes, alignment, and the fusion parameters prescribed by ASTM F2620 to get the best possible outcome.
Electrofusion, one of the other techniques, involves the use of specific couplings that encase embedded heating elements. It can be utilized in areas with limited space, where butt fusion equipment cannot be used. The electrofusion technique also can pre-program the voltage and heating duration with set standards stipulated by ASTM F1055. Moreover, non-HDPE materials that require disassembly can be connected through flanges and mechanical joint adapters.
Without regard to the selected method, I make sure that jointing processes respect the relevant specifications of temperature, pressure, and cooling time to preserve the systems and the objectives of the project.
Trenchless installation and directional drilling
Trenchless technology and directional drilling are two methods I use to install pipelines while causing minimal disturbance to the surface. I follow the methodology of trenchless installation by ensuring technical aspects such as the drill path, the lubrication used during boring, and the tension on the pipe being installed into the ground. For instance, the path that is drilled will have to be designed in a way such that it is not overly tight radiused to avoid damaging the pipe. Additionally, the drilling mud used has to be of appropriate viscosity and density to stabilize the borehole as well as optimize cutting removal, which is the primary purpose including soil makeup and needs of the project.
Directional drilling requires the control of the angles, both the entry and exit ones, to be able to control the stress imposed on the HDPE pipe during the pullback. The pulling force should not exceed the permitted tensile strength of the pipeline material which is dictated by the size, wall thickness, and grade of the material classed under ASTM D3350. The appropriate cooling times have to be respected and be observed post-installation to permit cooling molecular relaxations to secure the integrity of the pipeline by ensuring its shape is not altered.
With these stone-by-stone guidelines and adhering to the relevant industry standards, I can ensure optimal results and maintain the long-term functionality of these systems.
Reference sources
Frequently Asked Questions (FAQs)
Q: What are the standard dimensions for HDPE SDR 11 pipe?
A: HDPE SDR 11 pipe dimensions vary based on the pipe’s nominal size. Common sizes range from 1/2 inch to 65 inches in diameter. The outside diameter of the pipe and wall thickness are precisely calculated to maintain the Standard Dimension Ratio (SDR) of 11. For specific dimensions, it’s best to refer to manufacturer specifications or contact us for detailed information.
Q: What is the typical length of HDPE SDR 11 pipes?
A: HDPE SDR 11 pipes are often supplied in standard lengths of 20 ft or 40 ft. However, some manufacturers offer custom lengths to suit specific project requirements. For large-scale projects, longer lengths may be available to minimize the number of joints and improve installation efficiency.
Q: How does the wall thickness of HDPE SDR 11 pipe compare to other SDR ratings?
A: HDPE SDR 11 pipe has a thicker wall compared to higher SDR ratings like SDR17. The thicker wall allows SDR 11 pipes to resist higher pressures and provide greater durability. For example, an SDR 11 pipe will have a thicker wall and higher pressure rating than an SDR17 pipe of the same diameter.
Q: What are the common applications for HDPE SDR 11 pipes?
A: HDPE SDR 11 pipe is often used in various applications due to its strength and durability. Common uses include potable water distribution, irrigation systems, drainage systems, and industrial fluid transfer. It’s also utilized in construction projects, mining operations, and for protecting underground cables. The pipe’s resistance to corrosion makes it an excellent alternative to traditional materials like iron.
Q: How do I calculate the minimum pull strength for the HDPE SDR 11 pipe?
A: To calculate the minimum pull strength for HDPE SDR 11 pipe, you need to consider factors such as the pipe’s diameter, wall thickness, and material properties. It’s crucial to consult with a professional engineer or pipe manufacturer to determine the correct pull strength for your specific application. You can contact us for assistance in calculating the appropriate pull strength for your project.
Q: Are HDPE SDR 11 pipes suitable for drinking water systems?
A: Yes, HDPE SDR 11 pipes are suitable for potable water systems. They are manufactured to meet strict standards for use with drinking water and do not impart any taste or odor to the water. These pipes are resistant to chemicals and corrosion, making them a safe and long-lasting choice for transporting potable water.
Q: What are the advantages of using HDPE SDR 11 pipe over other pipe materials?
A: HDPE SDR 11 pipe offers several advantages over other materials. It is lightweight, flexible, and resistant to corrosion and chemicals. The pipe has excellent flow characteristics, low friction loss, and can withstand high pressures. HDPE pipes are also more environmentally friendly, have a long service life, and require less maintenance compared to traditional pipe materials. These qualities make them efficient and cost-effective for various applications.